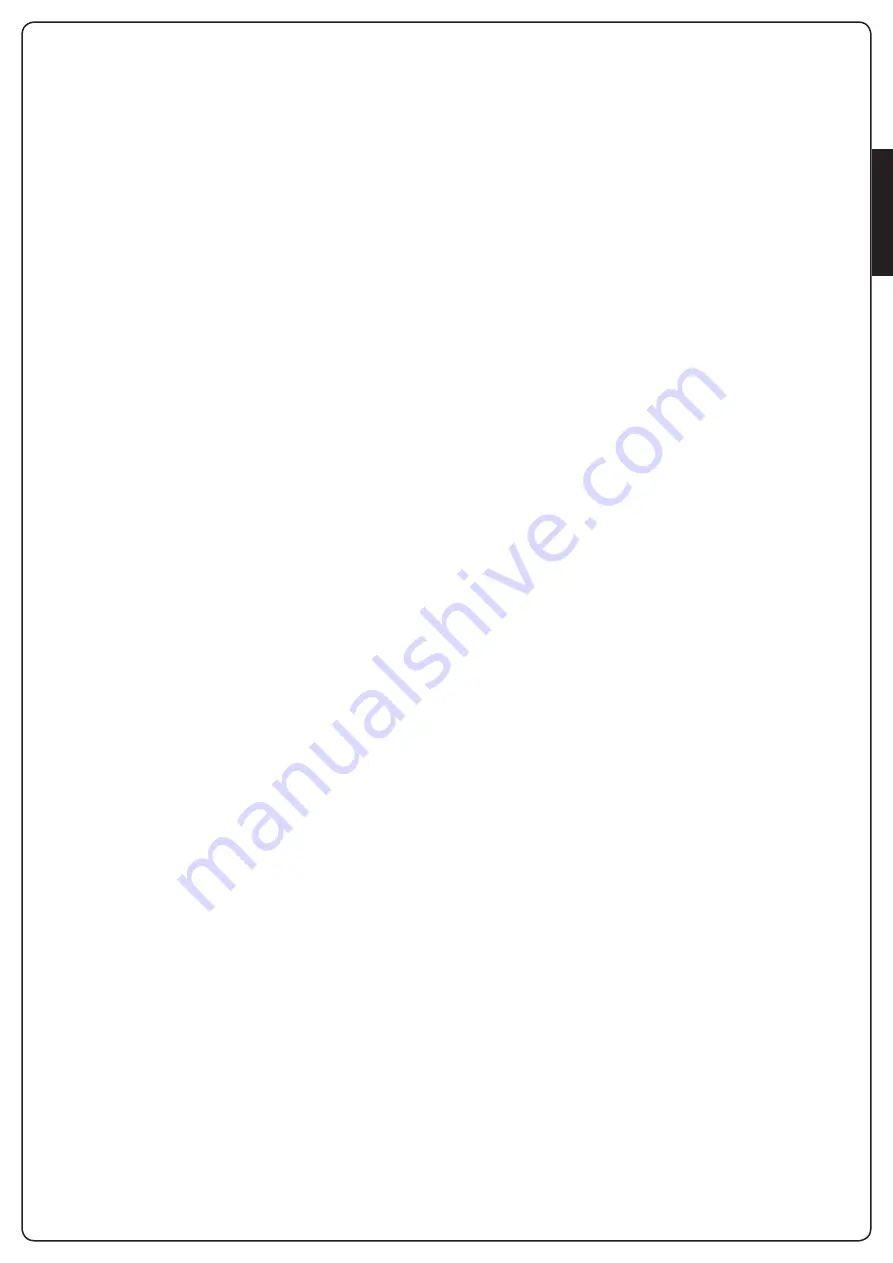
ENGLISH
- 47 -
9.7 - SAFETY RIBBONS
They can be installed located on the anti-shock rubber bumper
strip, which normally comes provided with the boom kit.
In case of intervention during the closing, reopening and disabling
of the automatic closing occurs.
The control unit is able to carry out either the classic safety
ribbons with normally closed contact, or conductive rubber safety
ribbons with 8,2 kohm nominal resistance.
Connect the cables between terminals
M5
and
M6
of the control
unit.
m
ATTENTION
: In order to meet the requirements of the
EN12978 rules, it is necessary to install safety ribbons controlled
by a control unit continuously checking the proper working.
If using control units suited to the test by power outage, connect
the power supply cables of the control unit between terminals
M10 (+)
and
M9 (-)
of the control unit. Otherwise, connect them
between terminals
G1 (+)
and
G2 (-)
.
m
ATTENTION:
• If more safety ribbons with normally closed contact are used,
their outputs must be connected in series.
• If more safety ribbons with pressure conductive rubber are
used, their outputs must be connected in cascade style and
only the last one must be ended on the nominal resistance.
• The active edges, connected to the accessory power supply,
are not active when the control unit switches to ENERGY
SAVING mode
9.8 - COURTESY LIGHT
The COURTESY LIGHT output consists of a simple N.O. contact
(Normally Open Circuit) and does not provide any power supply.
Thanks to the COURTESY LIGHT output, the control unit PD16
allows the connection of a utility light (a courtesy light or a garden
light, for example), which is programmed automatically, or by
arming channel 4 of the MR receiver.
The courtesy light terminals can be used as an alternative for a
230V / 120V flashing light with integrated intermittence.
m
ATTENTION
: when the control unit is operated by battery,
the 230V / 120V output flashing signal does not work.
The COURTESY LIGHT output consists of a simple N.O. contact
and does not provide any power supply. The maximum output of
the contact is of 230V - 5A.
Connect the cables to terminals
B1
and
B2
.
9.9 - LOW VOLTAGE LIGHT OUTPUT
The control unit has a 24 VDC output that allows connection of a
maximum load of 3 W.
This output can be used to connect a warning light, indicating the
status of the barrier, or for a low voltage flashing light.
Connect the low voltage signal light or flashing light wires to
terminals
G6 (+)
and
G7 (-)
.
m
CAUTION
: Pay attention to the polarity of the connected
device if necessary.
9.10 - EXTERNAL AERIAL
We suggest to use the external aerial (model: ANS433) in order to
guarantee the maximal range.
Connect the antenna hot pole to terminal
A2
of the control unit
and the braiding to terminal
A1
9.11 - HOLDING MAGNET
The control unit PD16 is equipped with an output for feeding
an holding magnet. Through a dedicated menu it is possible to
regulate the output voltage up to a maximum value of 24Vdc.
The power supply to the holding magnet is interrupted at the
beginning of every opening (with adjustable anticipation from
the menu) and restored at the end of the closing (with adjustable
delay from the menu).
Connect the power supply to the holding magnet between
terminals
M8 (+)
and
M7 (-)
PLEASE NOTE: The locking electromagnet is connected
to the accessory power supply. Hence, it is essential to
deactivate the energy saving function to use it.
9.12 - LOCK-OUT (PREWIRED)
The input BLOCCO is connected to a microswitch set in action
from the blocking lock of the inspection access flap.
In case of opening of the inspection access flap, the control unit
gets blocked: in this condition the boom movement commands
coming from the activation inputs or the remote controls are not
accepted.
For viewing of the programming menu and for setting the boom’s
actions, only the functions operated with the pushbuttons
h
,
i
,
OK
are allowed.
9.13 - ENCODER (PREWIRED)
The control unit PD16 controls the barrier’s set in motion through
the encoder.
Moreover, the encoders also allow recognizing if the barrier jams
in an abnormal position because of an obstacle.
For the encoders operation it is indispensable that the barrier’s
closing position is noticeable through a mechanical stop.
With every ignition of the control unit, the first working cycle
causes the alignment of the encoder on the point of arrest in
closing.
Summary of Contents for NIUBA-24V
Page 2: ...1153 mm 320 mm 287 mm 218 mm 897 mm 1168 mm 374 mm 239 mm 319 mm 897 mm ...
Page 7: ...ITALIANO 5 NIUBA4 NIUBA6 ...
Page 11: ...ITALIANO 9 FIG 3 FIG 4 ...
Page 13: ...ITALIANO 11 A D E C F F G E A B D C O N M ...
Page 31: ...ITALIANO 29 ...
Page 34: ...ITALIANO 32 ...
Page 39: ...ENGLISH 37 NIUBA4 NIUBA6 ...
Page 43: ...ENGLISH 41 FIG 3 FIG 4 ...
Page 45: ...ENGLISH 43 A D E C F F G E A B D C O N M ...
Page 63: ...ENGLISH 61 ...
Page 66: ...ENGLISH 64 ...
Page 71: ...FRANÇAIS 69 NIUBA4 NIUBA6 ...
Page 75: ...FRANÇAIS 73 FIG 3 FIG 4 ...
Page 77: ...FRANÇAIS 75 A D E C F F G E A B D C O N M ...
Page 95: ...FRANÇAIS 93 ...
Page 98: ...FRANÇAIS 96 ...
Page 103: ...ESPAÑOL 101 NIUBA4 NIUBA6 ...
Page 107: ...ESPAÑOL 105 FIG 3 FIG 4 ...
Page 109: ...ESPAÑOL 107 A D E C F F G E A B D C O N M ...
Page 127: ...ESPAÑOL 125 ...
Page 130: ...ESPAÑOL 128 ...
Page 131: ......