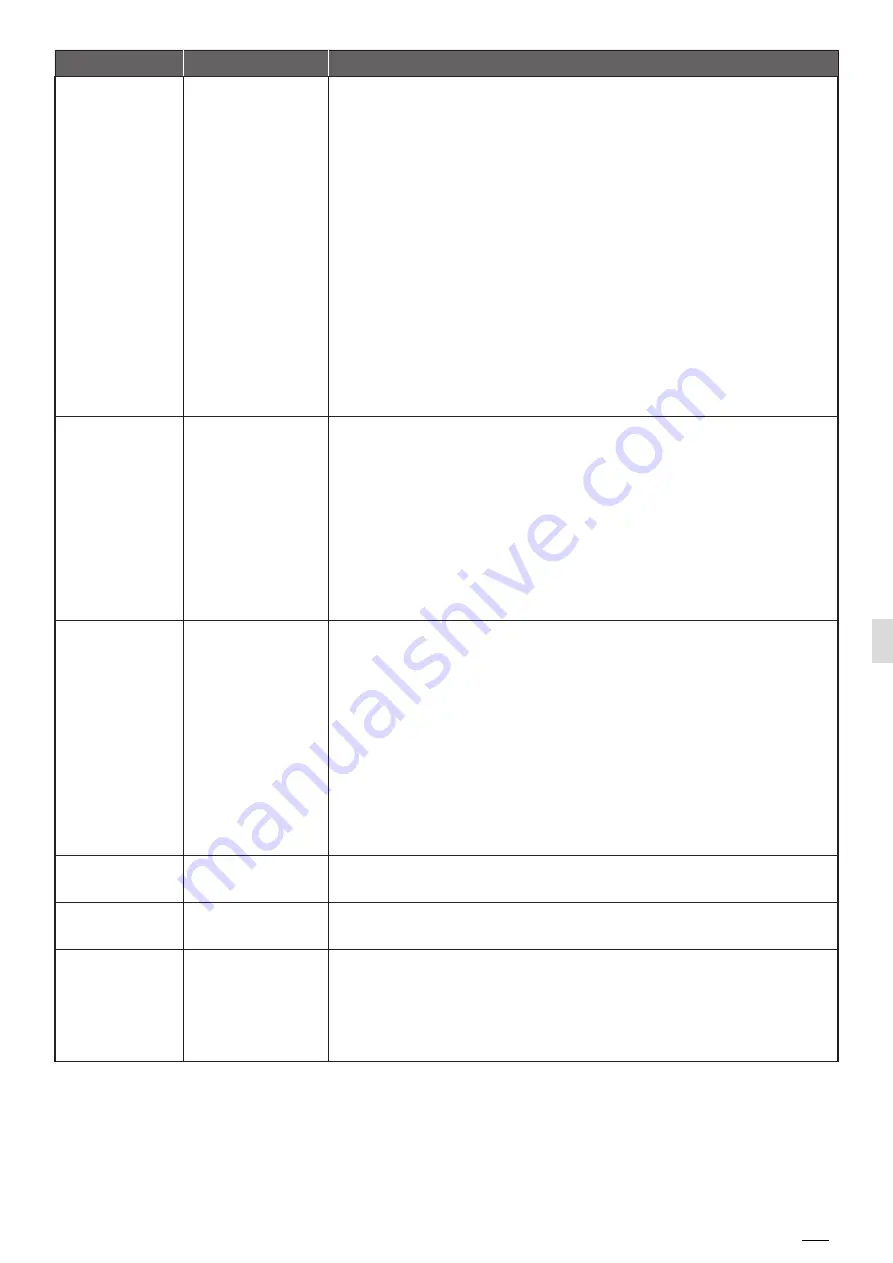
Symptom
problem
Solution
When the oven
is running a
cooking program,
the circuit
breaker trig-gers
Set a cooking program, t = inf, T = 30 °C, v = 2 and run the oven.
• If the circuit breaker triggers, it means that at least one motor is
shorted. Test between the black and red wire of the motor
socket. If there is electrical continuity with the multimeter set to
ohms, replace the faulty motor.
If the circuit breaker does not trigger, set T = 260 °C and run the oven.
• If the circuit breaker triggers it means that at least one heating
element is shorted. Test between the cable harness of the heating
element coils. If there is electrical continuity with the multimeter
set to ohms, replace the damaged heating element.
If with T = 260 °C the circuit breaker does not trigger, set STEAM.Plus to
100 % and run the o ven.
• If the circuit breaker triggers , it means that the steam solenoid
valve is shorted. Test between the cable harnesses of the solenoid
valve. If there is electrical continuity with the multimeter set to
ohms, replace the faulty solenoid valve.
The
electrical
oven does not
heat
A phase is missing
Try to plug the oven to another socket and run the oven. If the oven
works properly call an electrician, otherwise follow the next steps
The
electrical
oven does not
heat
Either the heat-
ing elements or
the contactors are
damaged
Measure the amp consumption of the oven with the clamp meter di-
rectly on the terminal block.
• If the phase consumption does not match the technical data avail-
able on Infonet, check if the contactors close the circuit.
• If they do not close the circuit, check between A1 and A2 PIN with
the multimeter set to V AC if the power board supplies 230 V AC to
the contactor coil.
• If the power board does not feed the contactors replace it,
otherwise replace the contactors;
Measure the amp consumption of each heating element turn.
If you find 0 A in at least one coil replace the element
The oven does
not cook evenly
The gasket is dam-
aged
Replace the gasket
The oven does
not cook evenly
The chimney is
clogged
Clean the chimney with a metal brush
The oven does
not cook evenly
The motors do not
invert the sense of
rotation
Measure the resistance of the braking element with the multimeter
set to ohm. Do you have the right resistance value according to the
technical data?
• If not, replace the braking element
• If yes, replace the power board
The circuit
breaker
triggered
100
Summary of Contents for MINDMaps BAKERTOP
Page 1: ...SERVICE MANUAL...
Page 138: ...OVEN Test to do Test 1 138...
Page 139: ...OVEN Pt100 Temperature Probe Resistance table 139...
Page 150: ...Test to do test 1 Measure the electrical conductivity of the micro switch OVEN 150...
Page 155: ...163 OVEN Pt100 Temperature Probe Resistance table 155...
Page 166: ...OVEN test 1 Measure the power supply to the washing solenoid valve 166...
Page 189: ...OVEN Pt100 Temperature Probe Resistance table 189...
Page 215: ...214...