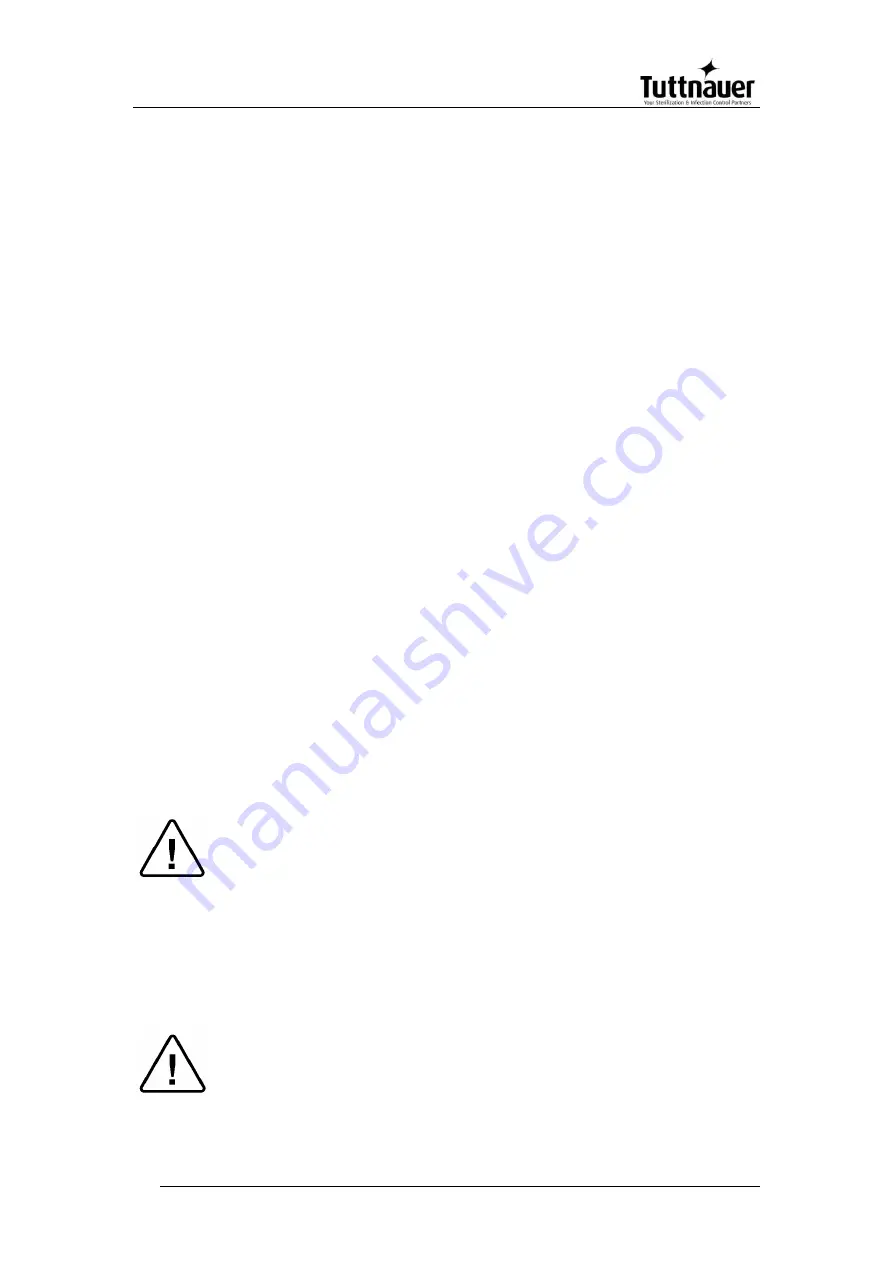
Page 5
The temperature and pressure are controlled through sensors placed
inside and outside the media container or bottles.
The sterilizer is fully automatic with a choice of 10 programs,
eliminating any need for operator intervention during a cycle (program
7-10 are for vacuum test only). A computerized control unit enables
precise control and monitoring of physical parameters and clear
documentation of the sterilization cycles.
The autoclave is equipped with a safety valve, which will discharge at
an overpressure of over 2.8 Bar (40 psi), which is located on the
chamber near the pressure switch and the steam pressure gauge. The
control system provides adequate protection, to ensure the safety of
personnel and reliable operation with a minimum of down time.
The sterilizer has multiple built - in safety devices, which provides
adequate protection to ensure the safety of operating personnel.
The printer prints the preset and actual parameters of the cycle
(temperature, time and pressure).
The autoclave is provided with a pressure gauge that is used as guide
only. Should there be a power failure during the operation of the
autoclave, the pressure gauge indicates to the operator that there is
pressure in the chamber.
A deviation of +1.6% is accepted.
Note:
After operating the sterilizer, brown stains might appear on the bottom
of the chamber. These stains are a result of the heating elements that
are located at the lower external part of the chamber. The brown color
is a common phenomenon, can easily be removed, and will not have
any effect on the sterilized goods.
This manual is intended to give the user a general understanding of
how the autoclave works and indicates the best ways to operate and
take care of it in order to obtain optimum results and a trouble-free
operation. After reading this manual, operating the autoclave should be
straightforward. However, since the autoclave is built using high
technology sensitive components, no attempt should be made by the
user or any other unauthorized person to repair or recalibrate it.
Only technical personnel having proper qualifications, holding
technical documentation and adequate test instrumentation are
authorized to undertake repair or service.