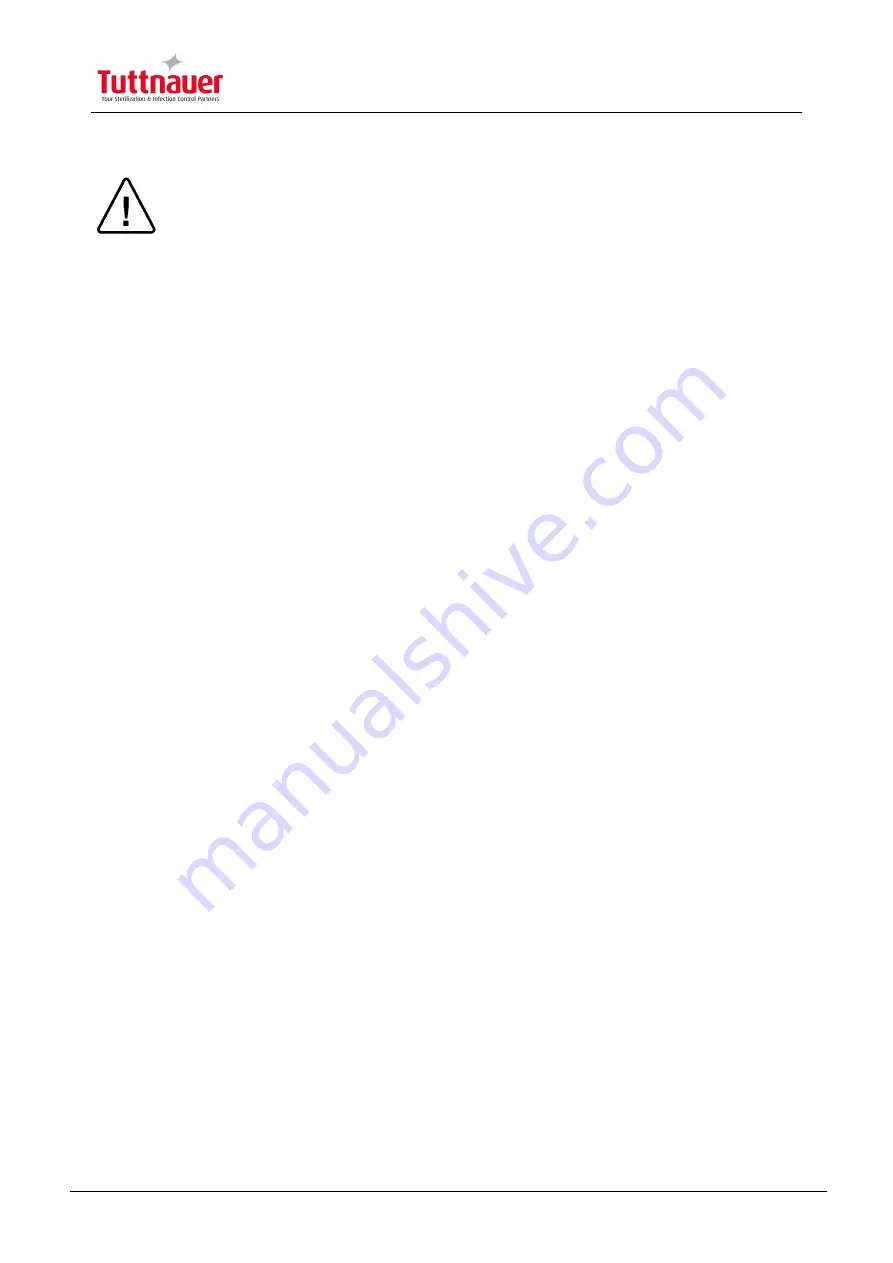
MAN205-0195042EN Rev. A
Aug. 2011
Page 107 of 137 pages
9.12
Testing the Safety Valves
Warning!
Before testing the safety valve, wear heat resistant safety gloves and keep all
body parts away from the steam flow.
Attention!
Make sure that the test is performed while the door is closed.
1. Testing the Generator Safety Valve
1.1
Ensure the autoclave green toggle switch is OFF.
1.2
Set the pressure of the working pressure switch and cut off pressure switch to
6 bar.
1.3
Operate the generator and verify that the pressure increases by checking the
generator pressure gauge.
1.4
Verify that the safety valve blows in the range of 5
–5.5 bar. (75 – 80 psi).
1.5
If the safety valve did not blow at the pre-set pressure stop the operation of
the generator, decrease the pressure to atmospheric pressure and replace
the safety valve with a new one.
1.6
If the safety valve was replaced, repeat step 1.1
—1.4 to test the new one.
1.7
Re-adjust the pressure of the working pressure switch to 3.5
—4 bar, and then
Re-adjust the cut off pressure switch to 5 bar.
1.8
Turn ON the autoclave green toggle switch when the test is done.
2. Testing the Jacket Safety Valve
2.1
Mark the position of the pressure regulator's adjustment knob.
2.2
Turn the adjustment knob one turn in the pressure increase direction.
2.3
On the solenoid valve battery, open manually valve 91. This is done by
turning the adjustment screw until the screw's slot is vertical.
2.4
Operate the autoclave and verify that the pressure increases.
2.5
Verify that the safety valve blows in the range of 2.8
–3.0 bar (40 – 44 psi).
Summary of Contents for 6671130
Page 2: ...Web site http www tuttnauer com...
Page 30: ...MAN205 0195042EN Rev A Aug 2011 Page 24 of 137 pages PIPING SYSTEM DRAWING...
Page 32: ...MAN205 0195042EN Rev A Aug 2011 Page 26 of 137 pages PNEUMATIC CONTROL SYSTEM DRAWING...
Page 84: ...MAN205 0195042EN Rev A Aug 2011 Page 78 of 137 pages This page intentionally left blank...
Page 128: ...MAN205 0195042EN Rev A Aug 2011 Page 122 of 137 pages This page intentionally left blank...
Page 129: ...MAN205 0195042EN Rev A Aug 2011 Page 123 of 137 pages XPCS MANUAL...