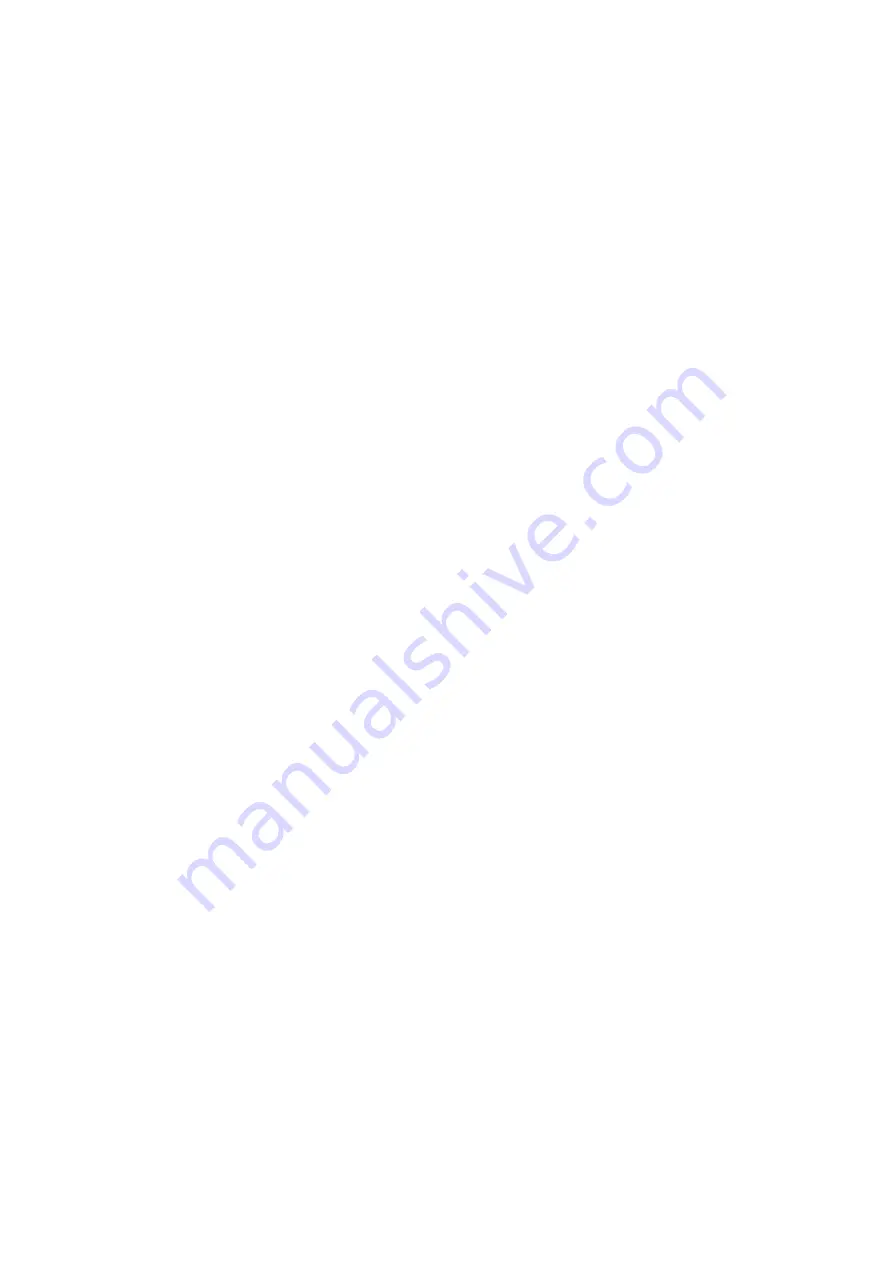
Page 30 of 77
8
PRINTER
8.1
Printer Output
The printing is on thermal paper with 24 characters per line and contains
the following information:
·
Date:
·
Time:
·
Ser. Num:
·
Model:
·
Version:
·
Cycle Num:
·
Cycle:
·
Ster Temp:
·
Ster Time:
When the sterilization cycle begins the printer starts printing the above
data.
After the preliminary printing, the autoclave starts performing the
sequence of operations of the cycle. The measured values of temperature
and pressure are printed at fixed time intervals, according to the phase of
the process, as shown in the table on the next page.
The data is printed from the bottom up, beginning with the date and
ending with "Cycle Ended". For an aborted cycle, "Cycle Failed" and the
Error message are printed (refer to "Displayed Error Messages/Symbols").
For an example of a typical printout, see next page.
Note: Please note that the print out goes from the bottom upwards.
Summary of Contents for 2840 EL-D
Page 4: ...Page 3 of 77 14 TROUBLESHOOTING 73 15 SPARE PARTS LIST 77 16 ACCESSORIES 77...
Page 5: ...Page 4 of 77 TABLE OF CONTENT Cont DRAWINGS PAGE NO FRONT VIEW 17 REAR VIEW 18...
Page 26: ...Page 25 of 77...
Page 34: ...Page 33 of 77...
Page 71: ...Page 70 of 77...
Page 72: ...Page 71 of 77 Cap Gasket Strainer element Strainer Housing WATER STRAINER...
Page 77: ......