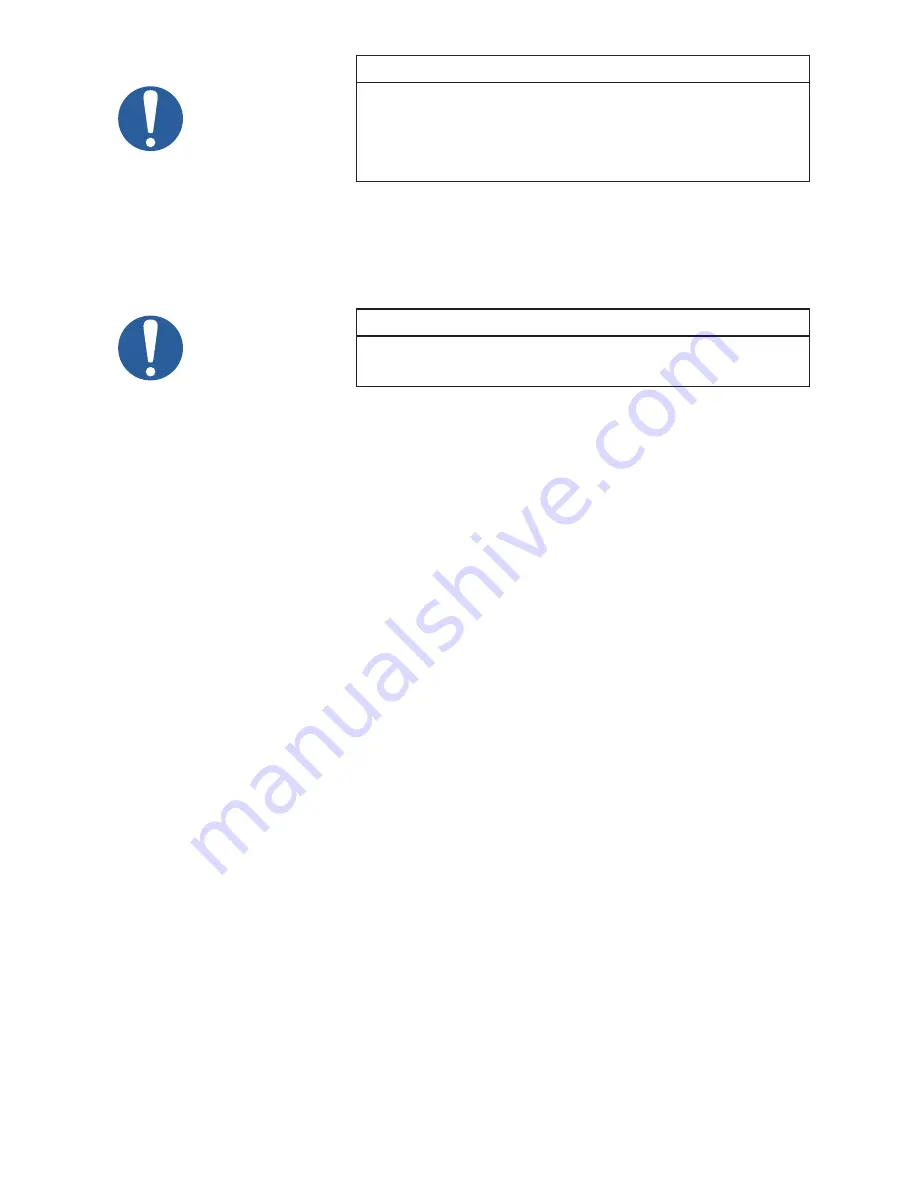
31
NOTE
On model 4000, it is not necessary to remove item 15 unless the end plate
is being replaced.
The flat head screws have nylok in their threads and may be difficult to
remove. Strike the head a couple of blows with a flat face hammer for easy
removal.
12. Using two yoke style pullers with pressure screws attached to free end plate bores, pull end plate
from housing. Dimensional drawings for the pullers are on page 44 (T29603-1). Tap out the bearings
[10].
Series 90/91:
Tap out mechanical seal [54], spacers [123], and labyrinth seal [51].
Series 92/93:
Tap out seal slinger [238] and spacers [123]. The oil slinger stator [79] should not be
removed unless it is damaged or the end plate is to be replaced.
NOTE
On some older units the oil seal slinger is made up of two separate parts
- items 238 & 129. The newer design combines these two parts and is
identified as item 238.
13. Using a single yoke puller with longer screws, push out one rotor at a time making sure the rotor is
vertical in the housing (for support) while removing.
14. Remove the two temporarily installed screws and tap gear end plate from housing and remove bearings
and seals.
15. Clean all parts with a good grade of clean solvent and replace any worn or damaged parts with factory
approved parts. New bearings, seals, and O-rings should be installed at each assembly.
9.2 ASSEMBLY OF 4000C AND 5500C SERIES BOOSTERS
The assembly procedure is generally the same for all series, but where there are differences, notations are
made. All vacuum joints, end covers, seal casings, and plugs should be sealed with an RTV Silicone Sealer
equal, unless O-rings have been provided.
Gaskets are never used between rotor housing and end plates. Dowel pins are used to locate end plates,
housing, and drive end cover in proper location relative to each other. Be sure they are in place.
It is recommended that the gear end rotor shaft bearings be purchased from Tuthill Vacuum and Blower
Systems, as they are specially ground to locate the rotors with correct end clearance relative to the gear end
plate. Do not use standard bearings which have not been flush ground within .001” (.025 mm) tolerance.
Use factory approved parts.
It is suggested that long feeler gauges (12” or 30 cm) be used to check the interlobe timing, preferably (2)
.006” (.15 mm), (1) .005” (.13 mm), (1) .004” (.10 mm), and (1) .003 (.08 mm). This will give you all the
combinations from .003” (.08 mm) to .021” (.53 mm) and also .024” (.61 mm) which is the total.
9.2.1 PREPARATION OF END PLATES FOR ASSEMBLY
1. Remove all nicks, scratches, etc. from all sealing surfaces. Clean all parts thoroughly. See Page 44 for
dimensions of seal pressing tool.
2.
90/91 Series
- Press in new labyrinth seals [51] into bores of both end plates [4] making sure the
scalloped areas of seal case are aligned with openings in vent area of seal bore. Coat O.D. of
mechanical seal with sealer and press into seal bore, coming to rest on top of labyrinth seal. Make
sure seals are fully seated without deforming case. Keep sealer from carbon surface. Carefully wipe
carbon with soft tissue and cleaning agent (acetone) before continuing assembly.
92/93 Series
- Press in new oil slinger stators [79] if required.
Summary of Contents for M-D Pneumatics 7010
Page 43: ...43 NOTES ...
Page 50: ...50 3200C CUTAWAY DRAWING 3200 90C 91C 92C 93C 1 OF 2 A ...
Page 51: ...51 3200C CONFIGURATIONS DRAWINGS 3200 90C 91C 92C 93C 2 of 2 A ...
Page 54: ...54 5500C CUTAWAY DRAWING 5500 90C 91C 92C 93C 1 OF 2 E OIL LEVEL SIGHT GAUGE DETAIL ...
Page 55: ...55 5500C CONFIGURATIONS DRAWINGS 5500 90C 91C 92C 93C 2 of 2 E ...
Page 56: ...56 7000C CUTAWAY DRAWING 7000 90C 91C 1 OF 3 ...
Page 57: ...57 7000C CONFIGURATIONS DRAWING 7000 90C 2 OF 3 ...
Page 58: ...58 7000C CONFIGURATIONS DRAWING 7000 91C 3 OF 3 7000 91C 7013 SHOWN ...
Page 68: ...68 NOTES ...