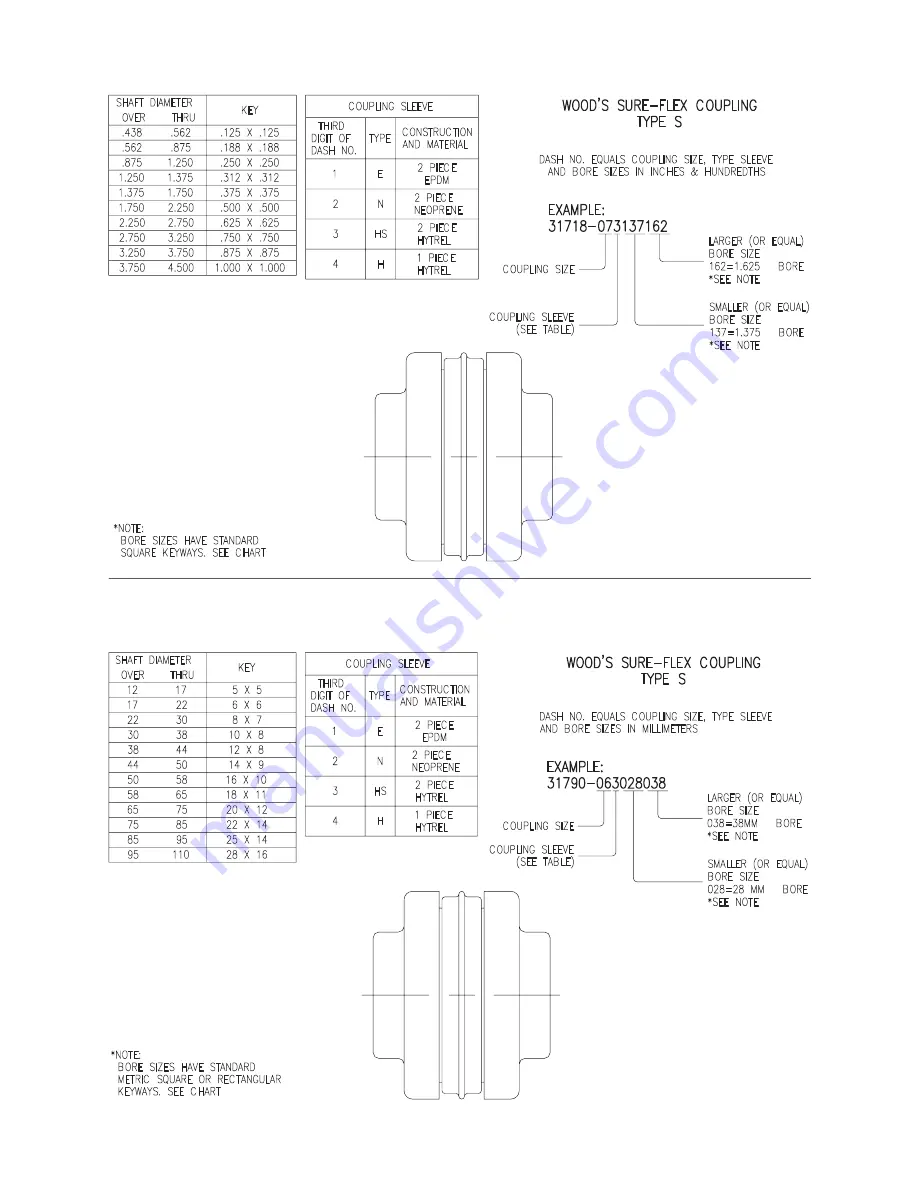
67
*NOTE:
BORE SIZES HAVE STANDARD
METRIC SQUARE OR RECTANGULAR
KEYWAYS. SEE CHART
THIRD
DIGIT OF
DASH NO.
95
85
110
95
58
65
75
50
44
65
75
85
58
50
28 X 16
25 X 14
18 X 11
22 X 14
20 X 12
16 X 10
14 X 9
22
38
30
17
12
30
44
38
22
17
SHAFT DIAMETER
OVER
THRU
8 X 7
12 X 8
10 X 8
6 X 6
5 X 5
KEY
N
2
2 PIECE
NEOPRENE
2 PIECE
HYTREL
1 PIECE
HYTREL
HS
3
4
H
COUPLING SLEEVE
2 PIECE
EPDM
CONSTRUCTION
AND MATERIAL
TYPE
1
E
EXAMPLE:
31790-063028038
COUPLING SIZE
COUPLING SLEEVE
(SEE TABLE)
DASH NO. EQUALS COUPLING SIZE, TYPE SLEEVE
AND BORE SIZES IN MILLIMETERS
WOOD'S SURE-FLEX COUPLING
TYPE S
THIRD
DIGIT OF
DASH NO.
.500 X .500
.625 X .625
.875 X .875
.750 X .750
1.000 X 1.000
*NOTE:
BORE SIZES HAVE STANDARD
SQUARE KEYWAYS. SEE CHART
2.750
3.250
3.750
1.750
2.250
3.250
3.750
4.500
2.250
2.750
.312 X .312
.250 X .250
.188 X .188
.125 X .125
.375 X .375
.875
1.250
1.375
.562
.438
1.250
1.375
1.750
.875
.562
SHAFT DIAMETER
OVER
THRU
KEY
2
N
2 PIECE
NEOPRENE
2 PIECE
HYTREL
1 PIECE
HYTREL
HS
H
3
4
COUPLING SLEEVE
2 PIECE
EPDM
CONSTRUCTION
AND MATERIAL
TYPE
E
1
EXAMPLE:
31718-073137162
COUPLING SIZE
COUPLING SLEEVE
(SEE TABLE)
WOOD'S SURE-FLEX COUPLING
TYPE S
DASH NO. EQUALS COUPLING SIZE, TYPE SLEEVE
AND BORE SIZES IN INCHES & HUNDREDTHS
LARGER (OR EQUAL)
BORE SIZE
162=1.625
Ø
BORE
*SEE NOTE
SMALLER (OR EQUAL)
BORE SIZE
137=1.375
Ø
BORE
*SEE NOTE
LARGER (OR EQUAL)
BORE SIZE
038=38MM
Ø
BORE
*SEE NOTE
SMALLER (OR EQUAL)
BORE SIZE
028=28 MM
Ø
BORE
*SEE NOTE
DRIVE COUPLING (U.S. CUSTOMARY) – 31718 (–)
DRIVE COUPLING (METRIC) – 31790 (–)
Summary of Contents for M-D Pneumatics 7010
Page 43: ...43 NOTES ...
Page 50: ...50 3200C CUTAWAY DRAWING 3200 90C 91C 92C 93C 1 OF 2 A ...
Page 51: ...51 3200C CONFIGURATIONS DRAWINGS 3200 90C 91C 92C 93C 2 of 2 A ...
Page 54: ...54 5500C CUTAWAY DRAWING 5500 90C 91C 92C 93C 1 OF 2 E OIL LEVEL SIGHT GAUGE DETAIL ...
Page 55: ...55 5500C CONFIGURATIONS DRAWINGS 5500 90C 91C 92C 93C 2 of 2 E ...
Page 56: ...56 7000C CUTAWAY DRAWING 7000 90C 91C 1 OF 3 ...
Page 57: ...57 7000C CONFIGURATIONS DRAWING 7000 90C 2 OF 3 ...
Page 58: ...58 7000C CONFIGURATIONS DRAWING 7000 91C 3 OF 3 7000 91C 7013 SHOWN ...
Page 68: ...68 NOTES ...