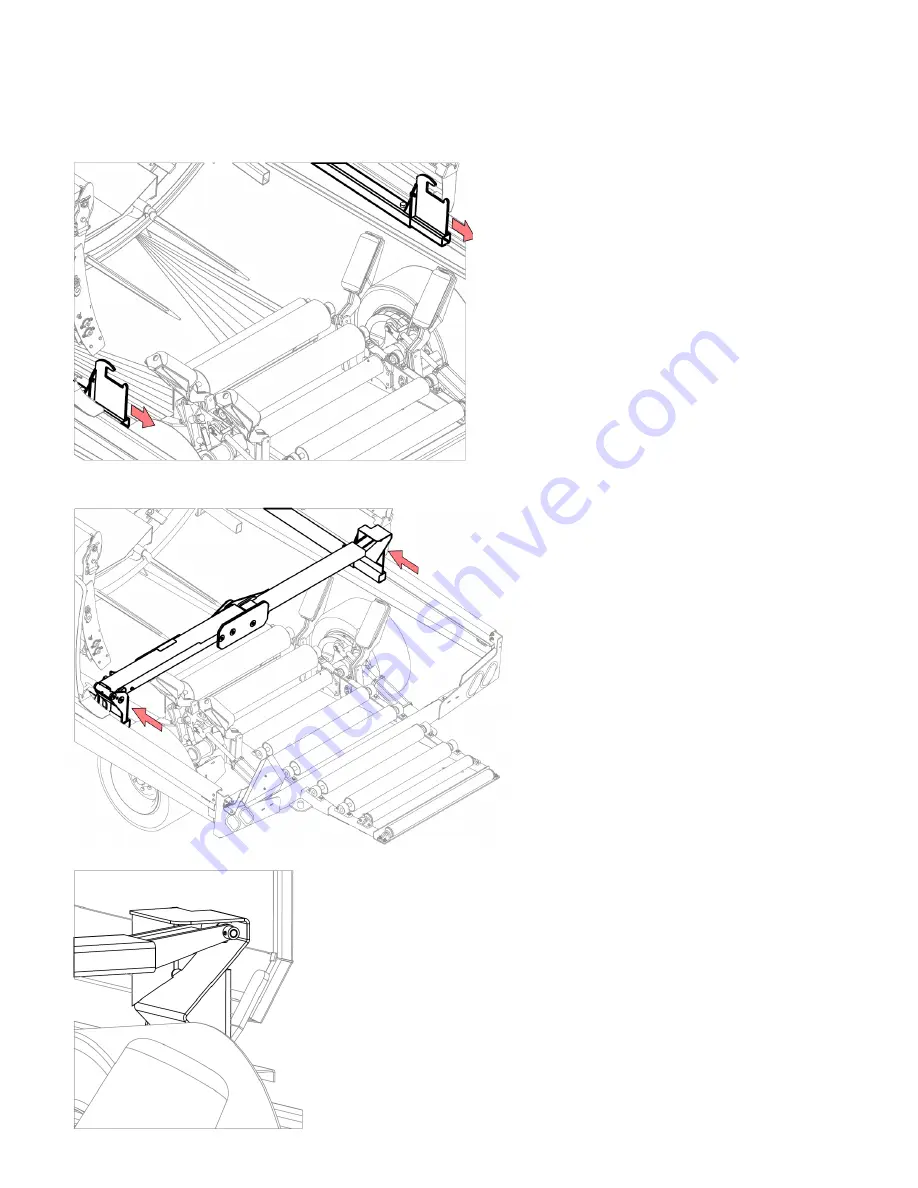
TL60ECV
-
Section 16: Option - Dispatch Arm 16-1
Section 16: Option - Dispatch Arm
Dispatch Arm Installation
Refer to
Parts Manual
to ensure all parts have been received.
1. Remove standard last bale pushoff hooks
from ram tubes. Keep unfastened hardware.
See
Fig.1
.
2. Insert right dispatch arm pocket into right ram
tube. Lock with existing bolt and nut. See
Fig.2
.
3. Use a lifting device to raise dispatch arm
assembly.
4. Slide dispatch arm into left ram tube. Bolt
with existing bolt and nut.
5.
Lower dispatch arm to ensure it fits into right
side pocket. See
Fig.3
.
Fig .2
Fig .3
Fig .1
Summary of Contents for TL60ECV
Page 7: ...Intentionally Left Blank...
Page 12: ...TL60ECV Section 2 Safety 2 3 Clearance Markers Part No DEAMBER Part No DERED...
Page 13: ...2 4 Section 2 Safety TL60ECV Safety Decal Locations NOTE Decals shown are not to scale...
Page 39: ...11 1 Section 11 Diagnostics TL60ECV Section 11 Diagnostics Manifold Solenoid Functions...
Page 59: ...VII Imperial Torque Value Chart TL60ECV Imperial Torque Value Chart...
Page 60: ...TL60ECV Metric Torque Value Chart VIII Metric Torque Value Chart...