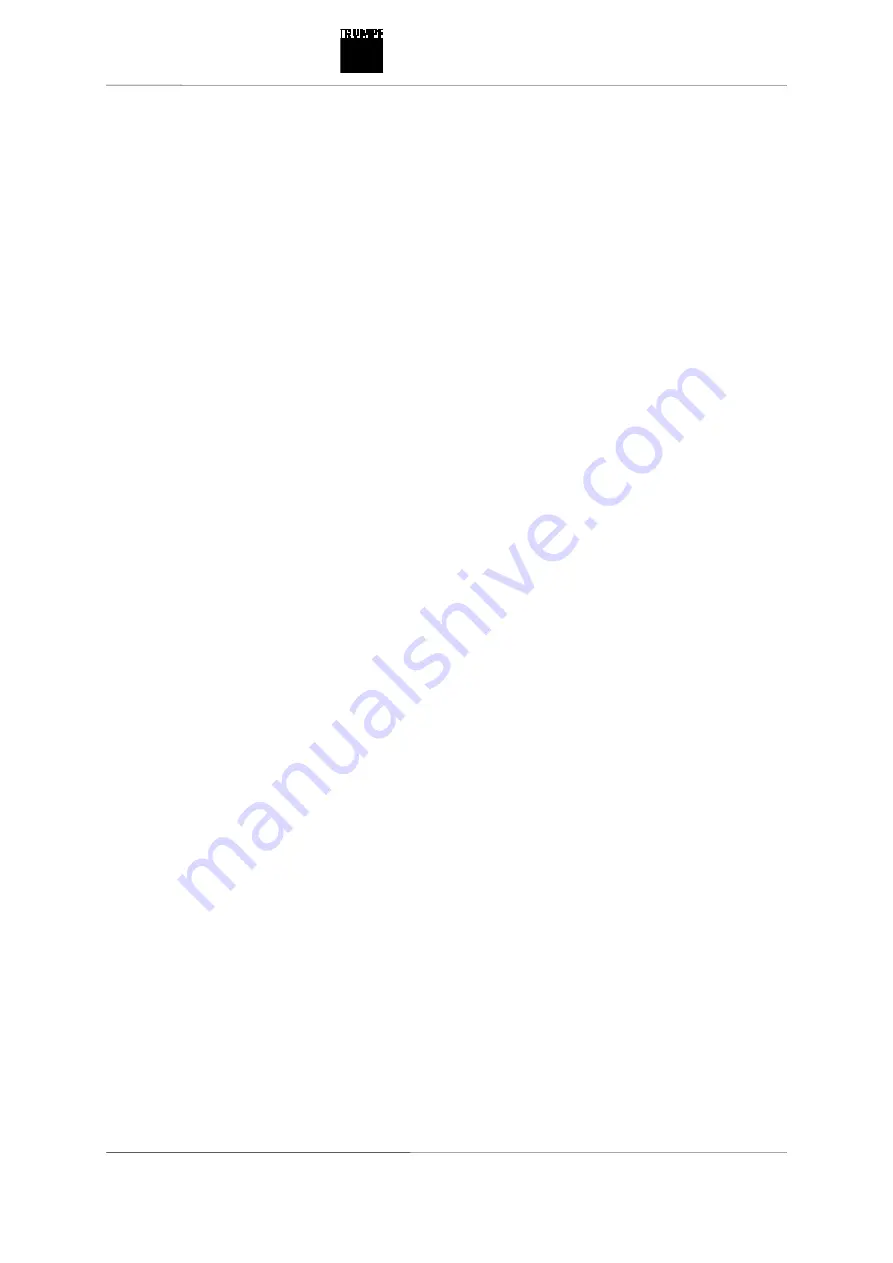
20
Operation
E459EN_05.DOC
4.2 Changing the cutting direction
In situations where space is limited, the tool and/or the cutting
direction can be turned by 90° to the right or to the left.
(see Fig. 13470, Pg. 22)
1. Open locking mechanism (15).
2. Rotate die carrier (1) by 90° in the desired direction.
3. Close locking mechanism (15).