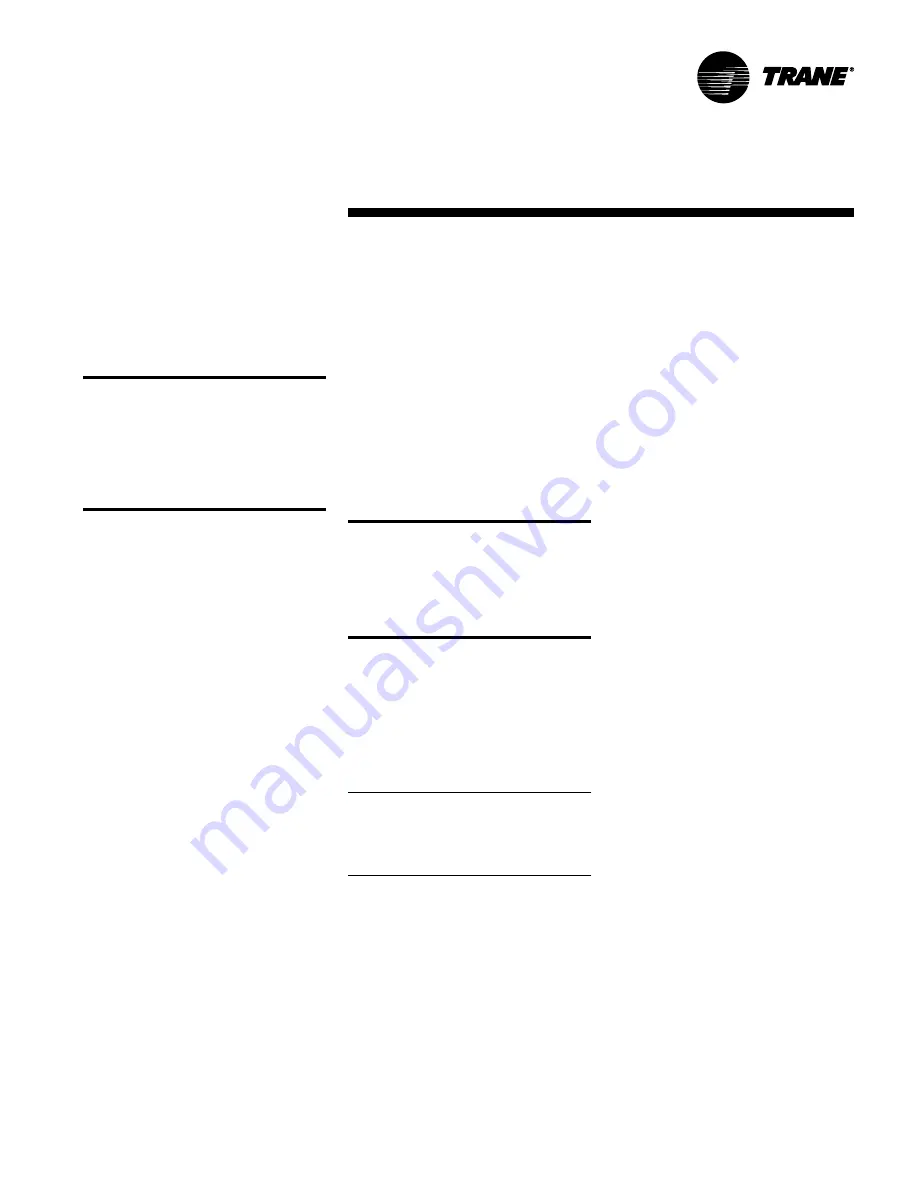
UNT-SVX07A-EN
41
installation
procedure
Installation
Installing the Unit
Follow the procedures below to install the
unit properly. Reference the “Dimensions
and Weights” section for specific unit
dimensions and mounting hole locations.
Vertical Units
CAUTION
Electrical Wiring!
Do not allow electrical wire to fall
between the unit and installation
surface. Failure to comply may result
in electrical shorts or difficulty
accessing wires.
Install vertical units in an upright position
using the
5
/
8
-inch diameter double key slot
hanger holes, located on the back of unit.
The hanger holes allow a maximum
shank size of
5
/
16
-inch diameter threaded
rods or lag screws (installer provides).
1. Prepare wall openings for recessed
units. Reference unit submittal for each
unit size dimensions. When installing
vertical units, consideration should be
given for units with an outside air
intake.
2. If the unit has leveling legs, adjust them
correctly to level unit.
3. Mark the position of the keyslot hanger
holes on the wall according to the
dimensions given in the
Dimensions &
Weights section for each unit model
and size. Align the hole locations evenly.
4. Insert the threaded rods or lag screws
in the wall before setting the unit in
place.
5. Remove the front panel (cabinet unit
only) by lifting it upward.
6. Position the hanger holes, located on
the back of the unit, over the rod or lag
screw heads, pushing the unit
downward to properly position.
7. Complete piping and wiring
connections, in addition to any
necessary ductwork to the unit as
instructed in the following sections.
Ensure that the auxiliary drain pan is in
position on fan-coil units.
8. Install the front panel before starting
the unit.
On cabinet units, replace the front panel
by aligning the bottom tabs on the unit
with the respective slots on the panel
bottom. Slide the front panel down onto
the tabs while holding the panel close as
possible to the cabinet. While the bottom
tabs are engaged, slide the front panel
upward enough to allow the top engaging
edge of the front panel to lap over the
engaging edge of the unit. This should
allow the panel to drop down and lock
into position.
On recessed units, install the front panel
by aligning and locking together the
interlocking support channel of the panel
and unit. While holding the panel against
the unit, tighten the screws at the top of
the panel until it fits tight against the unit’s
front. Do not over tighten the screws.
CAUTION
Motor Overload!
All unit panels and filters must be in
place prior to unit startup. Failure to
have panels and filters in place may
cause motor overload.
Horizontal Units
Install horizontal units suspended from
the ceiling using the four
5
/
8
-inch diameter
double key slot hanger holes, located on
the top of the unit. The hanger holes allow
a maximum shank size of
5
/
16
-inch
diameter threaded rods or lag screws
(installer provided). Follow the installation
procedure below.
Note: Follow the requirements of
National Fire Protection Association
(NFPA) Standard 90A or 90B, concerning
the use of concealed ceiling spaces as
return air plenums.
1. Prepare the ceiling opening for
recessed units. Reference the unit
submittals for dimensions.
2. Position and install the suspension rods
or a suspension device (supplied by
installer) according to the unit model
and size in the
Dimensions & Weights
section.
3. On cabinet units, remove the bottom
panel by using a
5
/
32
-inch Allen wrench
to unscrew fasteners. Swing the panel
down and lift outward.
4. Level the unit by referencing the
chassis end panels. Adjust the
suspension device.
5. Complete piping and wiring
connections.
necessary ductwork as instructed in the
following sections. Ensure that the
auxiliary drain pan is in position on fan-
coil units.
6. Install the bottom panel before starting
the unit.
7. Ensure condensate drain line is pitched
one inch per ten feet of pipe away from
the fan-coil unit.
Cabinet units
Install the bottom panel by placing the
hinged end on the unit’s hinged end
(always at the return end of the unit).
Reference the
Dimensions & Weights
section for keyslot hanger hole locations.
Swing the panel upward into position.
Secure the panel with the fasteners
provided. Do not overtighten the
fasteners.
Recessed units
Reference the
Dimensions & Weights
section for mounting locations and unit
weights. Follow the procedure below and
reference Figure I-IP-1.
1. Insert the mounting bolts through the
panel brackets of the trim ring and
secure to the hanger holes on the unit.
Tighten the mounting bolts to pull the
trim ring snug against the finished
ceiling.
2. Install the bottom panel by placing the
hinged end on the trim ring hinged end
(always at the unit’s return end).
3. Adjust the expansion collar’s inner duct
(only on fan-coil units with a bottom
return) to ensure a tight fit against the
insulation located on the perimeter of
the bottom panel’s return louver.
4. Close the s-hook on each end of safety
chain assembly. Insert s-hooks through
holes in unit and door. Close s-hook on
door.
5. Insert retaining screws through bottom
panel door and place retaining rings on
screws.
6. Swing the bottom panel upward into
position. Hook the safety chain to the
bottom panel and the unit. Tighten the
panel to the unit with the fasteners
provided.
Summary of Contents for UniTrane FC
Page 71: ...UNT SVX07A EN 71 typical wiring diagram Maintenance CSTI Fan Speed Switch...
Page 72: ...72 UNT SVX07A EN typical wiring diagram Maintenance CSTI Non Fan Speed Switch...
Page 73: ...UNT SVX07A EN 73 typical wiring diagram Maintenance Line voltage fan speed switch...
Page 74: ...74 UNT SVX07A EN typical wiring diagram Maintenance Tracer ZN010 with electric heat...
Page 76: ...76 UNT SVX07A EN typical wiring diagram Maintenance ZN520 with 2 stage electric heat...
Page 77: ......
Page 78: ......
Page 79: ......