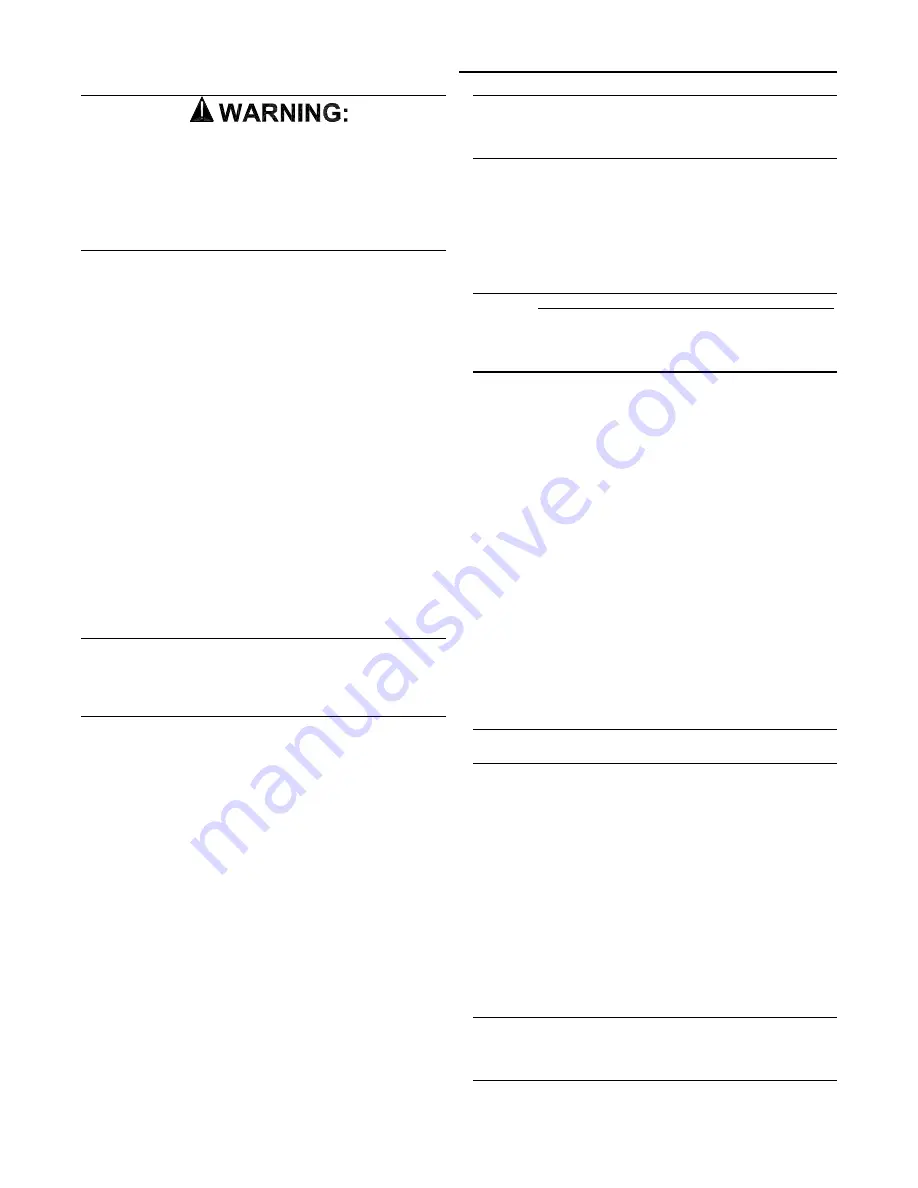
54
Note: To prevent compressor damage due to no
refrigerant flow, do not utilize the compressors to
pump the system down below 7 PSIG under any
circumstances.
11. After the compressors and condenser fans for the oper-
ating circuit have been operating for approximately 30
minutes, observe the operating pressures. Use the ap-
propriate pressure curve in Table 5-6 to determine the
proper operating pressures. If the operating pressures in-
dicate a refrigerant shortage, measure the system super-
heat and system sub-cooling.
Note: Do Not release refrigerant to the atmosphere!
If adding or removing refrigerant is required, the
service technician must comply with all Federal,
State and local laws. Refer to general service
bulletin MSCU-SB-1 (latest edition).
Sub-Cooling
The outdoor ambient temperature must be between 65
o
F
and 105
o
F and the relative humidity of the air entering the
evaporator must be above 40 percent. When the tempera-
tures are outside of these ranges, measuring the operating
pressures can be meaningless.
With the unit operating at “Full Circuit Capacity”, acceptable
sub-cooling ranges between 14
o
F to 22
o
F.
Measuring Sub-Cooling
a. At the liquid line service valve, measure the liquid
line pressure. Using a Refrigerant 22 pressure/
temperature chart, convert the pressure reading into
the corresponding saturated temperature.
b. Measure the actual liquid line temperature as close
to the liquid line service valve as possible. To ensure
an accurate reading, clean the line thoroughly where
the temperature sensor will be attached. After
securing the sensor to the line, insulate the sensor
and line to isolate it from the ambient air.
Note: Glass thermometers do not have sufficient
contact area to give an accurate reading.
c. Determine the system sub-cooling by subtracting the
actual liquid line temperature (measured in b) from
the saturated liquid temperature (converted in a).
Measuring Superheat
a. Measure the suction pressure at the outlet of the
evaporator as close to the expansion valve bulb
location as possible.
b. Measured the suction line temperature as close to
the expansion valve bulb, as possible.
c. Using a Refrigerant/Temperature chart, convert the
pressure reading to a corresponding saturated vapor
temperature.
Note: On many Trane fan/coil units, an access
valve is provided close to the expansion valve bulb
location. This valve must be added on climate
changers and other evaporators.
HAZ A R D O U S V O L TA G E
R O T A T I N G P A R T S !
UNIT STARTS AUTOMATICALLY
Make sure all personnel are standing clear of the unit
before proceeding. The system components will start
when the power is applied.
9. Turn the 115-volt control circuit switch 1S2 to the “On”
position.
a. Once each compressor or compressor pair has
started, verify that the rotation is correct. If a scroll
compressor is rotating backwards, it will not pump
and a loud rattling sound can be observed.
b. Check the condenser fans for proper rotation. The
direction of rotation is clockwise when viewed from
the top of the unit.
All Motors are Rotating Backwards;
1. Turn the field supplied disconnect switch or
circuit protector switch that provides power to
the condensing unit to the “Off” position. Lock
the disconnect switch in the open position while
working at the unit.
2. Interchange any two of the field connected main
power wires at the unit terminal block 1TB1 or
the optional factory mounted non-fused
disconnect switch (1S1) in the unit control panel.
Note: Interchanging “Load” side power wires at the
contactors will only affect the individual fan
rotation. Ensure that the voltage phase sequence at
the main terminal block 1TB1 is ABC as outlined in
the “Electrical Phasing” section.
Some Motors are Rotating Backwards;
1. Turn the field supplied disconnect switch or
circuit protector switch that provides power to
the condensing unit to the “Off” position. Lock
the disconnect switch in the open position while
working at the unit.
2. If the electrical phasing is correct, interchange
any two of the motor leads at the contactor for
each motor that is rotating backwards. Before
condemning a compressor, interchange any two
leads (at the compressor Terminal block) to
check the internal phasing. Refer to the
illustration in Figure 5-5 for the compressor
terminal/phase identification. If the compressor
runs backward for an extended period (15 to 30
minutes), the motor winding can overheat and
cause the motor winding thermostat to open.
10. With the compressors operating, slowly open the “Low
Side” valve on the manifold gauge set. The remainder of
the refrigerant will be drawn into the system.
System Start-Up (Continued)
Summary of Contents for RAUC-IOM-15
Page 8: ...8 Figure 3 2A RAUC C80 Unit Dimensional Data Recommended Clearances...
Page 9: ...9 Figure 3 2A Continued RAUC D10 Unit Dimensional Data Recommended Clearances...
Page 10: ...10 Figure 3 2A Continued RAUC D12 Unit Dimensional Data Recommended Clearances...
Page 11: ...11 Figure 3 2B EVPB C80 Evaporator Chiller Dimensions...
Page 12: ...12 Figure 3 2B Continued EVPB D10 Evaporator Chiller Dimensions...
Page 13: ...13 Figure 3 2B Continued EVPB D12 Evaporator Chiller Dimensions...
Page 14: ...14 Figure 3 2B Continued EVPB C80 through D12 Chill Water Pipe Stubout Dimensions...
Page 35: ...35 Installation Continued Field Connection Diagram Notes for all System Control Options...
Page 57: ...57 Figure 5 5 Typical Scroll Compressor Terminal Block System Start Up Continued...
Page 67: ...67...
Page 68: ...68...