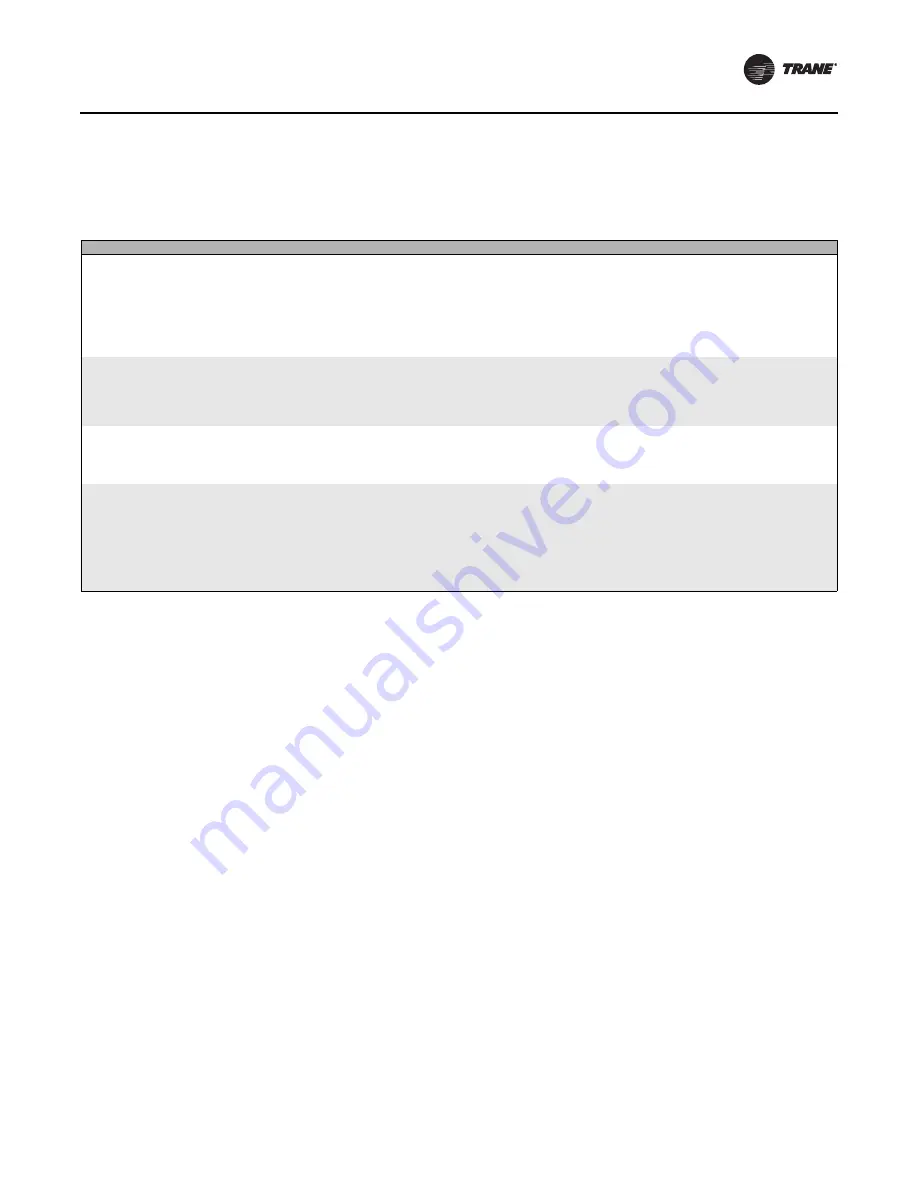
Diagnostics and Troubleshooting
UNT-SVX041D-EN
85
Motor
The motor connections and motor plug connections to the
adapter boards should be secure. Unit should be powered
off to check the fit of the connectors.
When configured correctly, the system will always
respond positively to direct, indirect, and conflicting speed
requests with very few exceptions.
Typical equipment and controls design practice will
ensure that the fans will come on if there is a call for heat,
cool, or ventilation. In most cases, we will depend on the
controller/thermostat to call for the fan to come on when
appropriate, but during calls for electric heat, or calls for
heat on CSTI units equipped with electric heat, as a call for
the appropriate fan speed. This behavior, as described
previously, is an indirect request.
When a call for electric heat is made, the system will
positively drive the fan on to the correct speed, regardless
of whether the controller has asked for fan operation or
not. The unit design incorporates an interlock instead of a
lock-out. (It does not lock out electric heat if the fan is set
to off; it brings the fan on.)
Notes:
•
In many cases, indirect requests will result in fan
behavior change regardless of whether the end-device
fails to actuate (due to device failure, or safety/down-
stream lockouts). If there is hot water available on CSTI
units with changeover coils and electric heat, we will
still drive the fan to the appropriate electric heat speed.
If the preceding conditions do not describe the behavior of
the unit, the following checks should be performed:
Table 47. Motor does not spin, spins too slowly
Situation
Probable Cause
Solution
Motor has been locked out
due to engine locked rotor
protection
Motor 1 has an obstruction. “Status Display” will be
interrupted to display:
• Remove obstruction from the fan wheel.
• Ensure that motor plugs and all plugs to adapter boards and
the ECM engine board are secure
• Verify that the configuration does not specify a motor that
is physically missing. Most units require only one motor. The
controller is made aware of the missing motor by specifying
all speeds related to Motor 2 to 0 rpm.
• Verify that
and
, the low motor signal output
limits, are set correctly.
Motor has been locked out
due to overspeed or runaway
condition
Motor 1 has an overspeed condition. The “Status Display”
will be interrupted to display:
• Ensure that set-screw is attached firmly to the motor shaft.
• Ensure that motor plugs and all plugs to adapter boards and
the ECM engine board are secure.
• Verify that the configuration does not specify a speed lower
than 500 rpm for the affected motor. Speeds below 500 rpm
are not supported on fan-coil units.
VSP Inputs (0–10V inputs)
are of the wrong polarity
Variable speed (VSP) inputs may not be properly wired to
1TB4
• Do not short the courtesy 10 VDC supply to chassis or loads
that require greater than 10 mA of DC current.
• Observe proper polarity of 0–10 VDC inputs. Failure to
observe proper polarity can cause failure of the VelociTach
motor control board, the customer-supplied controller.
Customer Controller output
signal to VSP Inputs are too
low.
Note:
If the customer supplied
controller outputs
signals that are below
the noise threshold, they
will be ignored by the
ECM Engine.
Noise floor is set too high.
• The VelociTach motor control board contains an adjustable
noise floor parameter,
that can be configured to
reject signals below the noise floor.
• The noise floor parameter is set too high, it can be lowered
as long as there are acceptable noise levels on the inputs
lines.