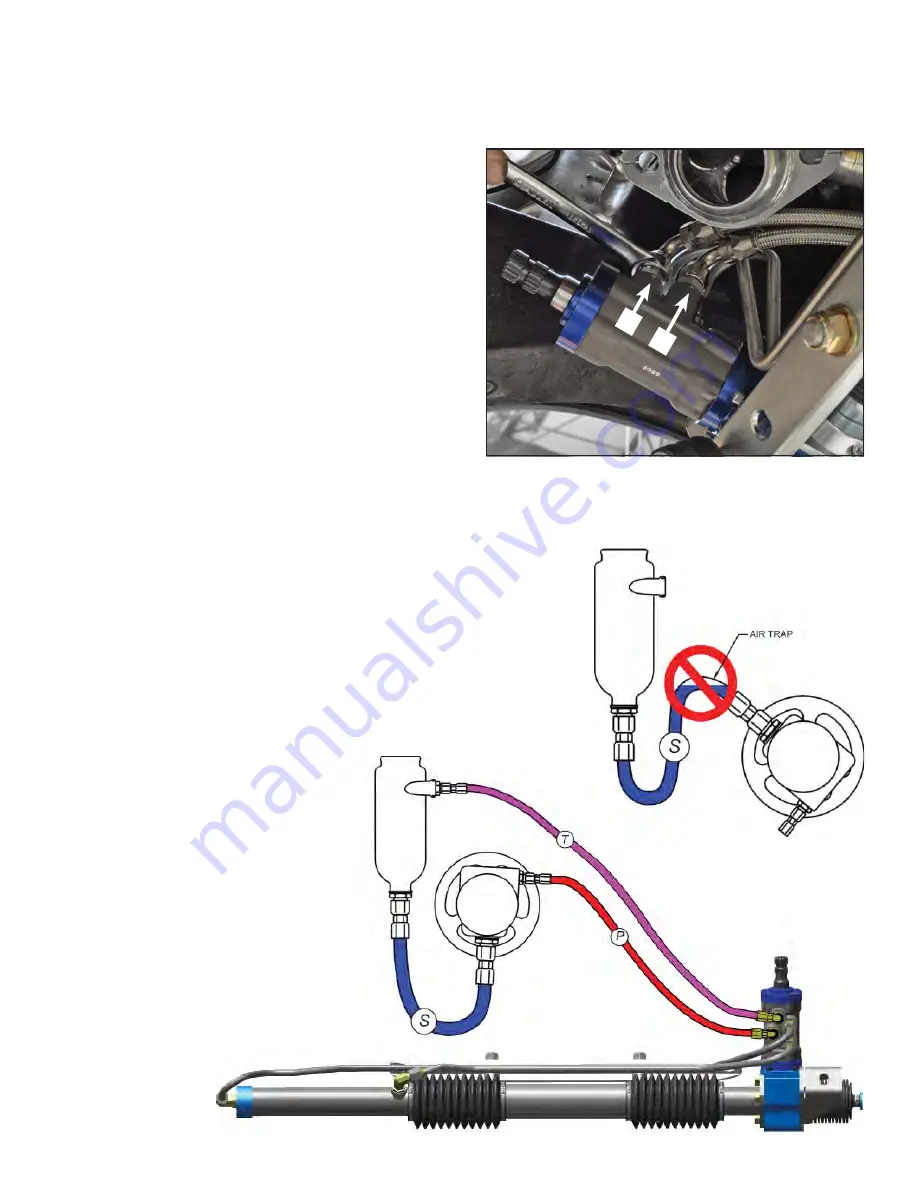
11
• The clamp is not square to the bracket-side clamp. Check by measuring the gap at the opposite ends
of the clamp.
• There is debris, a burr, or other imperfection on the clamp or rack tube that must be removed.
• Recheck for binding.
Connect Power Steering Pump and Lines
48. The power steering pump must be installed before
proceeding.
49. Instructions for assembly and installation of the TCP
hose kit (TCP HOSE-XX), power steering pump
(TCP PSP-FD), and bracket set (TCP PBS-FD-XX)
are packaged with their respective kits.
50. Power steering hoses and fi ttings must meet or
exceed a pressure rating of 2000 psi., and vacuum
rating of 28 in./Hg to safely handle potential spikes
in system pressure from wheel impacts and prevent
the pump feed hose from collapsing during periods of
high fl uid demand.
51. When connecting hoses to the pump, rack-and-
pinion control servo, and reservoir, carefully inspect
all fi ttings and hose ends for defects or debris. Even minor damage, such as a nick or dent, on an exposed
male fi tting or tapered fl are can prevent the fi tting from forming a tight seal, resulting in a leak.
• The control servo ports are marked:
• “P” for the high-pressure line from the pump output
• “T” for the low-pressure return line to the reservoir
52. Avoid Air Traps
- In general the Supply line (“S” in diagram) should
be as short and direct as possible, but above all it must not trap air.
A hose which approaches the pump from below and enters it from
above–as in the illustration–will have an air pocket at the top of the
bend, which de-primes the pump. The slightest high point in a level-
appearing run of hose can trap air.
T
P
High-Pressure Lines:
pump
output (P) and rack hard lines
Low-Pressure Line:
return line
to reservoir
No-Pressure Line:
supply line
from reservoir to pump
Diagrams courtesy of Woodward Steering
53. Verify that all fi ttings and hose
ends are tight and that the area
around each connection is
completely dry before fi lling the
system with fl uid. If the lines must
be removed use two wrenches
to remove the hose end without
unscrewing the fi tting.
Summary of Contents for RCKP214
Page 3: ...2 1967 70 Mustang Optional use Included in TCP EE 02 Manual Rack assembly is shown in diagram...
Page 15: ...14 NOTES...
Page 16: ...15...
Page 28: ...7 NOTES...
Page 35: ...6 NOTES...
Page 36: ...7 NOTES...