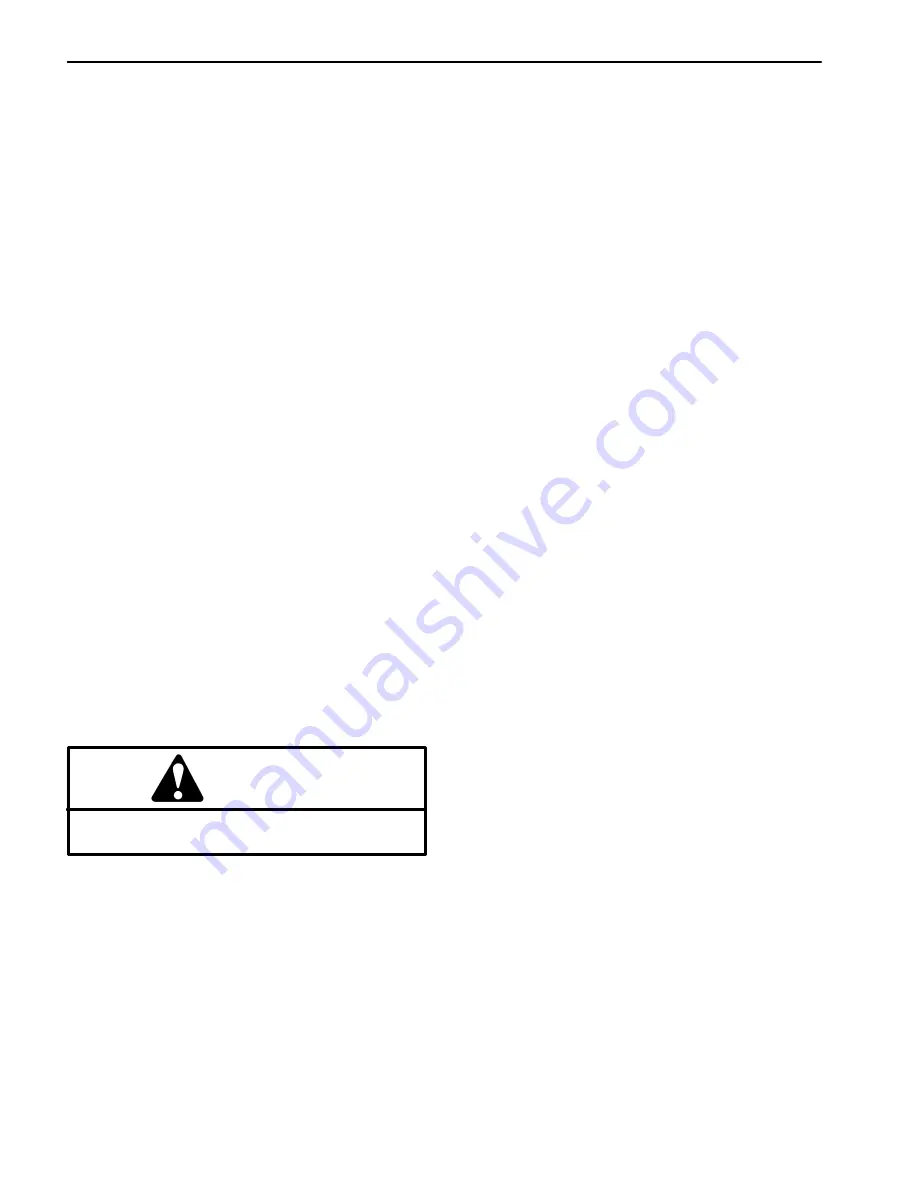
Multi Pro 1750
Hydraulic System
Page 4 − 48
Cartridge Valve Service
Removing a Cartridge Valve
1. Make sure the control manifold is clean before re-
moving the cartridge valve from the control manifold.
2. If cartridge valve is solenoid operated, remove nut
securing solenoid coil to the cartridge valve. Carefully
slide coil off the valve.
IMPORTANT: Use care when handling the cartridge
valve. Slight bending or distortion of the stem tube
can cause binding and malfunction. When remov-
ing cartridge valve from manifold, make sure that
deep well socket fully engages the valve base.
3. Remove cartridge valve from manifold using a deep
socket wrench. Note correct location for O−rings, seal-
ing rings and backup rings. Remove seal kit from car-
tridge valve and discard removed seals.
Inspecting and Cleaning a Cartridge Valve
1. Visually inspect the port in the manifold for damage
to the sealing surfaces, damaged threads and contami-
nation.
2. Visually inspect cartridge valve for damaged sealing
surfaces and contamination.
A. Contamination may cause valves to stick or hang
up. Contamination can become lodged in small valve
orifices or seal areas causing malfunction.
B. If valve sealing surfaces appear pitted or dam-
aged, the hydraulic system may be overheating or
there may be water in the system.
CAUTION
Use eye protection such as goggles when using
compressed air.
3. Clean cartridge valve using clean mineral spirits.
Submerge valve in clean mineral spirits to flush out con-
tamination. Particles as fine as talcum powder can affect
the operation of high pressure hydraulic valves. If car-
tridge design allows, use a wood or plastic probe to push
the internal spool in and out 20 to 30 times to flush out
contamination. Be extremely careful not to damage car-
tridge. Use compressed air for cleaning.
Installing a Cartridge Valve
1. Install the cartridge valve into the manifold:
A. Lubricate new seal kit components with clean
Dexron III ATF and install on valve. The O−rings,
sealing rings and backup rings must be arranged
properly on the cartridge valve for proper operation
and sealing.
B. Dip assembled cartridge into clean Dexron III
ATF.
IMPORTANT: Use care when handling the valve
cartridge. Slight bending or distortion of the
stem tube can cause binding and malfunction.
When installing cartridge valve into manifold,
make sure that deep well socket fully engages
the valve base.
C. Thread cartridge valve carefully into manifold
port by hand until the top O−ring is met. The valve
should go into manifold port easily without binding.
D. Torque cartridge valve using a deep socket
wrench to value identified in control manifold illustra-
tion.
2. If cartridge valve is solenoid operated, carefully
install solenoid coil to the cartridge valve. Secure coil to
valve with nut and torque nut to 60 in−lb (6.8 N−m).
3. If problems still exist after assembly, remove valve
and clean again or replace valve.
Summary of Contents for 41188
Page 1: ...Form No 15215SL Rev A Multi Pro 1750 Original Instructions EN...
Page 4: ...NOTES _...
Page 6: ...Multi Pro 1750 This page is intentionally blank...
Page 8: ...Multi Pro 1750 This page is intentionally blank...
Page 14: ...0 09375 Multi Pro 1750 Page 2 2 Product Records and Maintenance Equivalents and Conversions...
Page 48: ...Multi Pro 1750 Page 3 30 Kohler Gasoline Engine This page is intentionally blank...
Page 51: ...Multi Pro 1750 Hydraulic System Page 4 3 This page is intentionally blank Hydraulic System...
Page 71: ...Multi Pro 1750 Hydraulic System Page 4 23 This page is intentionally blank Hydraulic System...
Page 81: ...Multi Pro 1750 Hydraulic System Page 4 33 This page is intentionally blank Hydraulic System...
Page 85: ...Multi Pro 1750 Hydraulic System Page 4 37 This page is intentionally blank Hydraulic System...
Page 91: ...Multi Pro 1750 Hydraulic System Page 4 43 This page is intentionally blank Hydraulic System...
Page 97: ...Multi Pro 1750 Hydraulic System Page 4 49 This page is intentionally blank Hydraulic System...
Page 102: ...Multi Pro 1750 Hydraulic System Page 4 54 This page is intentionally blank...
Page 121: ...Multi Pro 1750 Page 5 19 Electrical System This page is intentionally blank Electrical System...
Page 127: ...Multi Pro 1750 Page 5 25 Electrical System This page is intentionally blank Electrical System...
Page 183: ...Multi Pro 1750 Page 6 9 Spray System This page is intentionally blank Spray System...
Page 191: ...Multi Pro 1750 Page 6 17 Spray System This page is intentionally blank Spray System...
Page 195: ...Multi Pro 1750 Page 6 21 Spray System This page is intentionally blank Spray System...
Page 201: ...Multi Pro 1750 Page 6 27 Spray System This page is intentionally blank Spray System...
Page 219: ...Multi Pro 1750 Page 6 45 Spray System This page is intentionally blank Spray System...
Page 226: ...Multi Pro 1750 Page 6 52 Spray System This page is intentionally blank...
Page 233: ...Multi Pro 1750 Page 7 7 Drive Train This page is intentionally blank Drive Train...
Page 237: ...Multi Pro 1750 Page 7 11 Drive Train This page is intentionally blank Drive Train...
Page 278: ...Multi Pro 1750 Page 7 52 Drive Train This page is intentionally blank...
Page 307: ...Multi Pro 1750 Chassis Page 8 29 This page is intentionally blank Chassis...
Page 340: ...Multi Pro 1750 Page 9 30 Ultra Sonic Boom Kit Optional This page is intentionally blank...
Page 352: ...Page 10 12 Ultra Sonic Boom Kit Optional Wire Harness Drawing...