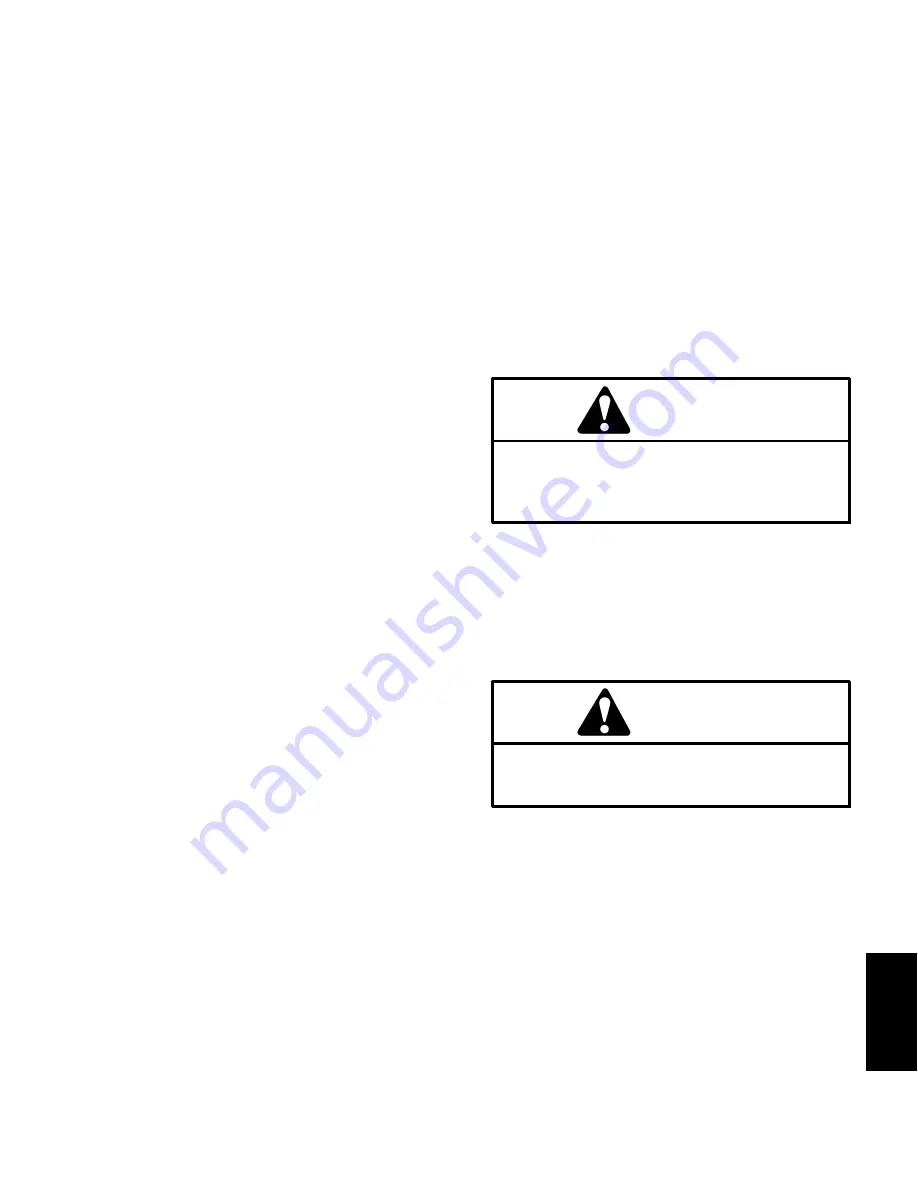
Multi Pro 1750
Chassis
Page 8 - 13
6. If necessary, remove parking brake assembly from
brake rotor:
A. Remove two (2) cap screws and flange nuts that
secure caliper bracket to rear axle.
B. Raise caliper bracket assembly (bracket, cable
and parking brake caliper) from brake rotor. Position
bracket assembly away from rotor.
7. If parking brake caliper removal is needed:
A. Loosen brake cable jam nuts that secure parking
brake cable to caliper bracket.
B. Remove return spring end from clevis pin on
parking brake lever.
C. Disconnect parking brake cable from caliper
bracket and caliper lever.
D. Slide parking brake caliper from caliper bracket. If
parking brake caliper needs to be serviced, see
Parking Brake Caliper Service in this chapter.
8. Inspect brake rotor for wear or damage. Minimum
brake rotor thickness is
0.154” (3.9 mm)
.
9. If necessary, remove brake rotor from wheel bearing
hub.
Installing (Fig. 7)
1. If brake rotor was removed, place brake rotor onto
studs in wheel bearing hub.
2. If parking brake caliper was removed from caliper
bracket:
A. Slide parking brake caliper onto caliper bracket.
B. Connect parking brake cable to parking brake le-
ver with clevis pin.
C. Secure clevis pin by inserting return spring end
into clevis pin.
D. Tighten cable jam nuts to secure parking brake
cable to caliper bracket. Position jam nuts so that all
threads on cable are showing towards the rear of the
vehicle.
3. If removed, install parking brake assembly to brake
rotor:
A. Slide parking brake bracket assembly (bracket,
cable and parking brake caliper) onto brake rotor.
Make sure that rotor is between brake pads.
B. Secure parking brake bracket to rear axle with
two (2) cap screws and flange nuts. Tighten flange
nuts from
35 to 40 ft- lb (48 to 54 N- m)
.
4. Slide brake caliper onto brake rotor. Make sure that
rotor is between brake pads.
5. Align caliper with mounting holes and secure caliper
to machine hub with two (2) flange head screws. Tighten
screws from
35 to 40 ft- lb (48 to 54 N- m)
.
6. If brake line was removed from brake caliper:
A. Place a new sealing washer on each side of brake
line fitting.
B. Install banjo bolt through brake line fitting and
banjo washers and then thread into caliper. Tighten
banjo bolt from
108 to 132 in- lb (12 to 14 N- m)
.
C. Bleed brakes (see Bleed Brake System in this
chapter).
WARNING
Failure to maintain proper wheel lug nut torque
could result in failure or loss of wheel and may
result in personal injury. Torque wheel lug nuts
from 75 to 80 ft- lb (102 to 108 N- m).
7. Install wheel assembly to vehicle (see Wheel As-
semblies in this chapter).
8. Check parking brake operation and adjust if neces-
sary (see machine Operators manual).
9. Lower machine to ground.
CAUTION
After servicing the brakes, always check the
brakes in a wide open, level area that is free of
other persons and obstructions.
10.After assembly is completed, check brake operation.
Burnish Brake Pads
After brake pad replacement, burnish (break- in) the
brakes before use.
1. Bring the machine to full speed and apply the brakes
to rapidly stop the machine without skidding or locking
up the wheels.
2. Repeat this procedure 10 times. To avoid overheat-
ing the brakes, wait 1 minute between each stop.
Ch
as
si
s
Summary of Contents for 41188
Page 1: ...Form No 15215SL Rev A Multi Pro 1750 Original Instructions EN...
Page 4: ...NOTES _...
Page 6: ...Multi Pro 1750 This page is intentionally blank...
Page 8: ...Multi Pro 1750 This page is intentionally blank...
Page 14: ...0 09375 Multi Pro 1750 Page 2 2 Product Records and Maintenance Equivalents and Conversions...
Page 48: ...Multi Pro 1750 Page 3 30 Kohler Gasoline Engine This page is intentionally blank...
Page 51: ...Multi Pro 1750 Hydraulic System Page 4 3 This page is intentionally blank Hydraulic System...
Page 71: ...Multi Pro 1750 Hydraulic System Page 4 23 This page is intentionally blank Hydraulic System...
Page 81: ...Multi Pro 1750 Hydraulic System Page 4 33 This page is intentionally blank Hydraulic System...
Page 85: ...Multi Pro 1750 Hydraulic System Page 4 37 This page is intentionally blank Hydraulic System...
Page 91: ...Multi Pro 1750 Hydraulic System Page 4 43 This page is intentionally blank Hydraulic System...
Page 97: ...Multi Pro 1750 Hydraulic System Page 4 49 This page is intentionally blank Hydraulic System...
Page 102: ...Multi Pro 1750 Hydraulic System Page 4 54 This page is intentionally blank...
Page 121: ...Multi Pro 1750 Page 5 19 Electrical System This page is intentionally blank Electrical System...
Page 127: ...Multi Pro 1750 Page 5 25 Electrical System This page is intentionally blank Electrical System...
Page 183: ...Multi Pro 1750 Page 6 9 Spray System This page is intentionally blank Spray System...
Page 191: ...Multi Pro 1750 Page 6 17 Spray System This page is intentionally blank Spray System...
Page 195: ...Multi Pro 1750 Page 6 21 Spray System This page is intentionally blank Spray System...
Page 201: ...Multi Pro 1750 Page 6 27 Spray System This page is intentionally blank Spray System...
Page 219: ...Multi Pro 1750 Page 6 45 Spray System This page is intentionally blank Spray System...
Page 226: ...Multi Pro 1750 Page 6 52 Spray System This page is intentionally blank...
Page 233: ...Multi Pro 1750 Page 7 7 Drive Train This page is intentionally blank Drive Train...
Page 237: ...Multi Pro 1750 Page 7 11 Drive Train This page is intentionally blank Drive Train...
Page 278: ...Multi Pro 1750 Page 7 52 Drive Train This page is intentionally blank...
Page 307: ...Multi Pro 1750 Chassis Page 8 29 This page is intentionally blank Chassis...
Page 340: ...Multi Pro 1750 Page 9 30 Ultra Sonic Boom Kit Optional This page is intentionally blank...
Page 352: ...Page 10 12 Ultra Sonic Boom Kit Optional Wire Harness Drawing...