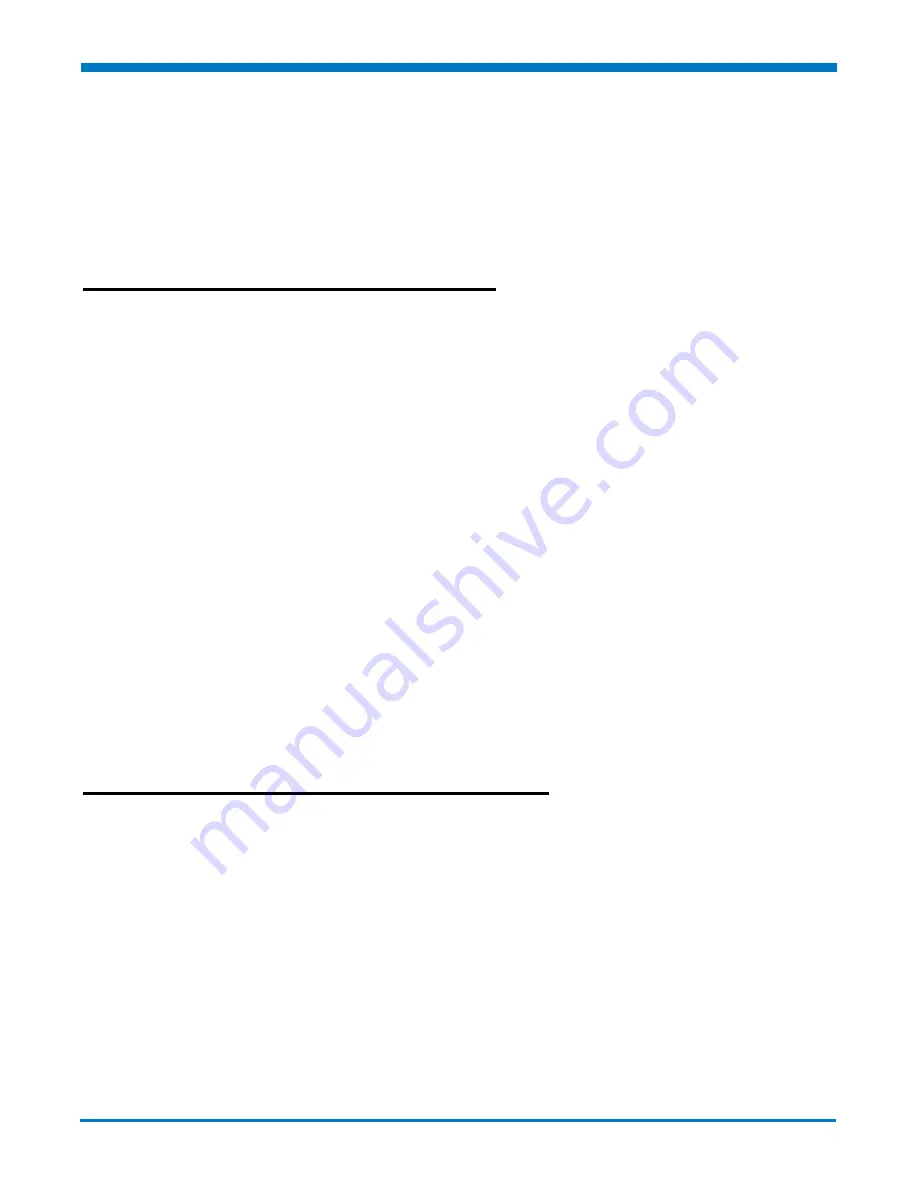
STAC6 Drives and Microstepping Motors:
User Manual
(Discontinued Product)
• 3.9 •
3:
C O N F I G U R A T I O N
by cycling the power. This is important as an alarm condition may
indicate a fault on the drive or it may indicate a error on your
machine or system. Resetting the drive at this point will make the
drive able to respond to any command signal present and could
result in damage to your machine or possibly injury.
BRAKE OUTPUT
A brake output is used when a motor is fitted with a fail safe holding
brake. These brakes are normally used to hold the load in position
when the motor is turned off, and are especially useful when the
motor must hold a load against gravity. Most brakes are fail safe,
requiring a voltage to hold the brake in the "released" position,
allowing the motor to move.
The brake output can be configured to open or closed on motor
enable. Care should be made when selecting this option to prevent
damage to your system.
The Brake Output has two time delay settings. The "release delay"
is the time delay between the brake being released and the drive
being available for moves. If a move is attempted immediately after
the drive is enabled this could create a time lag in the system as the
motor will not respond until after the brake release period.
The "brake engage" delay controls the time period between the
brake engaging and the drive disabling. This will ensure that the
brake is fully engaged before the load is no longer being held in
position by the motor.
LIMIT SWITCH INPUTS
The STAC6 has two inputs that can be configured as end of travel
limit switches. These are useful for linear applications such as
actuators.
The Limit Sensors dialog box is used to tell the drive whether input
switches or sensors are Open or Closed when activated. Select the
"Not Used" option when limit sensors are not present. SCL users
can configure these limit sensors to be used as programmable
inputs.