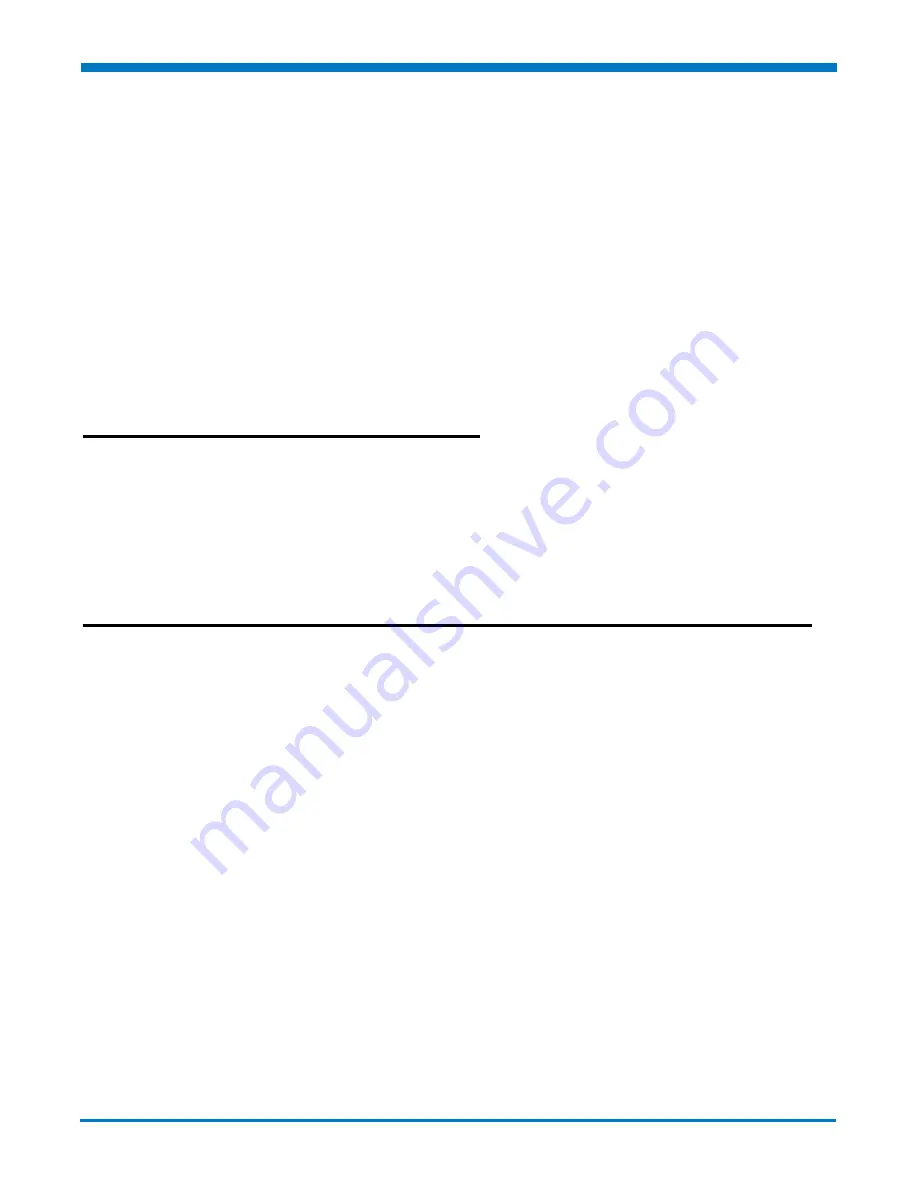
STAC6 Drives and Microstepping Motors:
User Manual
(Discontinued Product)
• 3.5 •
3:
C O N F I G U R A T I O N
lowering the current when the motor is at rest. In most cases, the
default value of 50% works well. Reduce motor heating further by
lowering the idle current percentage.
The idle current delay can also be adjusted. This determines the
delay between the instant the motor stops moving and the actual
reduction of the current. Allow time for the motor to settle out after a
move before going into idle reduction.
LOAD INERTIA
The anti-resonance feature of the STAC6 is most effective when the
load inertia is precisely set. If this value is known, click on the first option
button, enter the inertia in the box and select the units (oz-in-sec2,
g-cm2, etc) from the list. If the exact inertia value of the load is not
known, choose the second option button and enter a load
to motor inertia ratio in the box.
DEFINING A MOTOR NOT IN A RECOMMENDED LIST
Tolomatic highly recommends selecting an Applied Motion Products
Motor from the standard motor dropdown matched listing in the
configuration software. These are high quality motors whose torque,
rotor inertia, and harmonic waveform content are precisely known. The
motors also include shielded cables to reduce electrical emissions and
enhance safety. They come with prewired mating connectors further
reducing the risk of error.
If a motor not on the list is to be used, detailed information from
the manufacturer, including electrical specification (holding torque, rated
current and rotor inertia) plus a wiring diagram will be required. It is
important the motor be constructed from high quality magnetic
materials that are suitable for operation with a 160 volt bus such as that
of the STAC6.