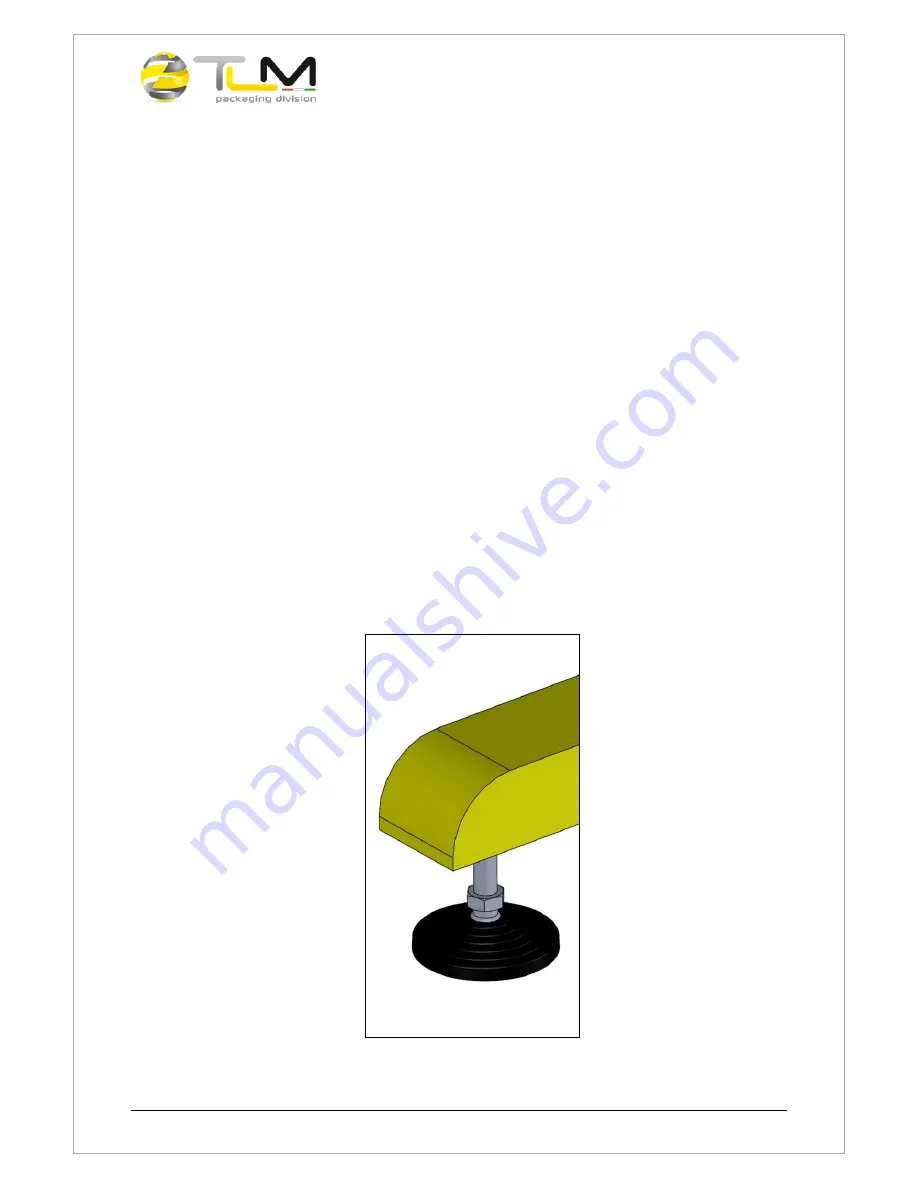
Use and Maintenance Handbook
– Prime 400 Packaging Machine
Page 19 of 71
9. INSTALLATION
The machine that this manual refers to is installed in a workshop environment.
For the purpose of making installation possible, the floor on which the equipment
is to be placed must be checked to make sure it is flat and solid. To get the best
results in the production cycle, the floor must not be subject to vibrations. It is
advisable to make preliminary study in such a way as to optimise the accessibility
to the machine so as to be able to:
Carry out the installation,
Obtaining the spaces for manoeuvre,
Carrying out Use and Maintenance interventions
To check the exact levelling of the machine proceed as indicated below:
Place the bubble level on the machine plan.
Check the levelling eventually insert specifics thickness
Complete the operation by pulling the fastening nuts in order that the machine
stand uniformly on the floor.