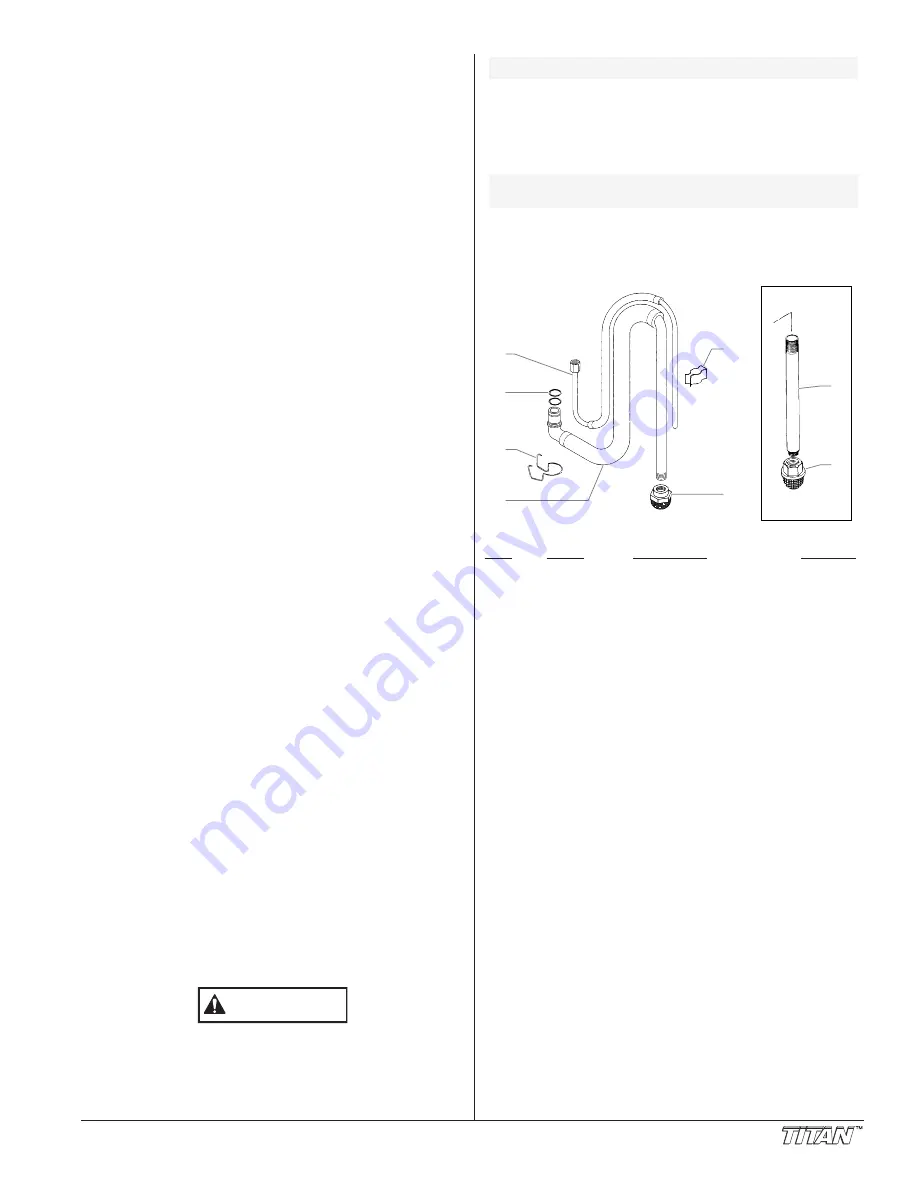
© Titan Tool Inc. All rights reserved.
21
Servicing the Seat
The design of the fluid section allows access to the inlet and
outlet valves and seat without completely disassembling the
fluid section. It is possible that the valves may not seat
properly because of debris stuck in the inlet or outlet seat.
Follow the instructions below for access to those areas.
5. Place a wrench on the foot valve housing (22) and
unthread.
6. Clean out all debris. Examine the foot valve parts and the
inlet valve seat (20). If damaged replace. Continue if
necessary or re-install.
7. Place a 3/4" socket on the outlet valve housing (15) and
remove.
8. Clean out all debris. Examine the outlet valve parts and
the seat (13). If damaged, reverse or replace.
9. Reassemble and test the unit. Should the unit not
perform properly, consult the “Troubleshooting” section in
this manual or continue with the valve repair and packing
replacement instructions below.
Servicing/Replacing the Outlet Valve
10. To clean or replace the outlet valve, remove the outlet
valve housing (15) while piston assembly (23) is still
attached to pump. This will prevent the piston from
rotating.
11. Remove upper cage (11), the seat (10), and the outlet
valve ball (12). Clean and inspect along with the outlet
valve housing (15). Replace if worn or damaged. Use
fine sandpaper to remove dried paint.
12. Reattach items 10–15 to the piston rod (9), and secure
tightly with a wrench.
Replacing the Packings
13. Unscrew the hose (see the “Filter Block Assembly” parts
list) from the fitting.
14. Remove the screws (7) with a 3/8" hex wrench and slide
the fluid section down so that the piston rod (9) is clear to
slide off.
15. Inspect the polyethylene gasket (5) on the fitting after
removing the fluid section. Clean or Replace.
16. Remove the retainer (2) and slide the piston rod down
through the pump housing (6) by lightly tapping on top of
piston assembly (23). Clean and inspect the piston rod
for wear. Replace if necessary.
17. Remove the upper packings (4) and the lower packings
(8) from the pump housing (6) and replace with a new set.
Always insert the packings with the raised side facing into
the pump housing.
18. Reattach the retainer (2) and make sure that the upper
guide (3) is clean and undamaged.
19. Place the pump housing (6) into a vise, leaving enough
room to slide the piston rod through the bottom of the
pump housing.
20. Using the piston guide tool (included in the repacking kit),
which slides over the top of the piston assembly (23),
insert the piston rod through the bottom of the pump
housing (6) and tap lightly with a rubber mallet on the
bottom of the piston rod until inserted.
21. Align the flats on the piston rod so that they are
perpendicular to the pump housing (23) and will line up
when reattaching to the connecting rod (1). This can be
achieved by rotating the piston rod by placing a wrench
on the outlet valve housing assembly (15) and turning.
Never use a wrench on the piston rod itself. This could
cause damage to the piston rod and cause leakage.
22. Slide the assembled pump housing with the piston
assembly onto the connecting rod and secure with the
screws (7). Be certain that the outlet hole is facing
towards the pump motor.
CAUTION
23. Reattach the hose (see the “Filter Block Assembly” parts
list) to the fitting. Be sure that polyethylene gasket (5) is
in place.
24. Reattach the foot valve assembly (24).
26. Reattach the return tube and the siphon assembly.
Siphon Assembly (P/N 700-1025)
Item
Part #
Description
Quantity
1
700-847
Return tube ......................................1
2
704-121
O-ring (standard) .............................2
704-109
O-ring, solvent-resistant (optional) ..2
3
704-127
Retaining clip ...................................1
704-129
Retaining ring
(alternate, included in literature set)
4
700-1023
Siphon hose
(includes items 2, 3, and 6 ..............1
5
755-135
Clip...................................................1
6
700-805
Intake screen ...................................1
For high rider only:
7
710-018
Siphon down tube ............................1
8
710-046
Inlet screen, 10 mesh ......................1
710-191
Inlet screen, 30 mesh (optional)
1
5
2
3
4
7
8
6
NOTE: Repacking Kit P/N 730-401 is available. For
best results use all parts supplied in this kit.
NOTE: Packing does not need to be adjusted.