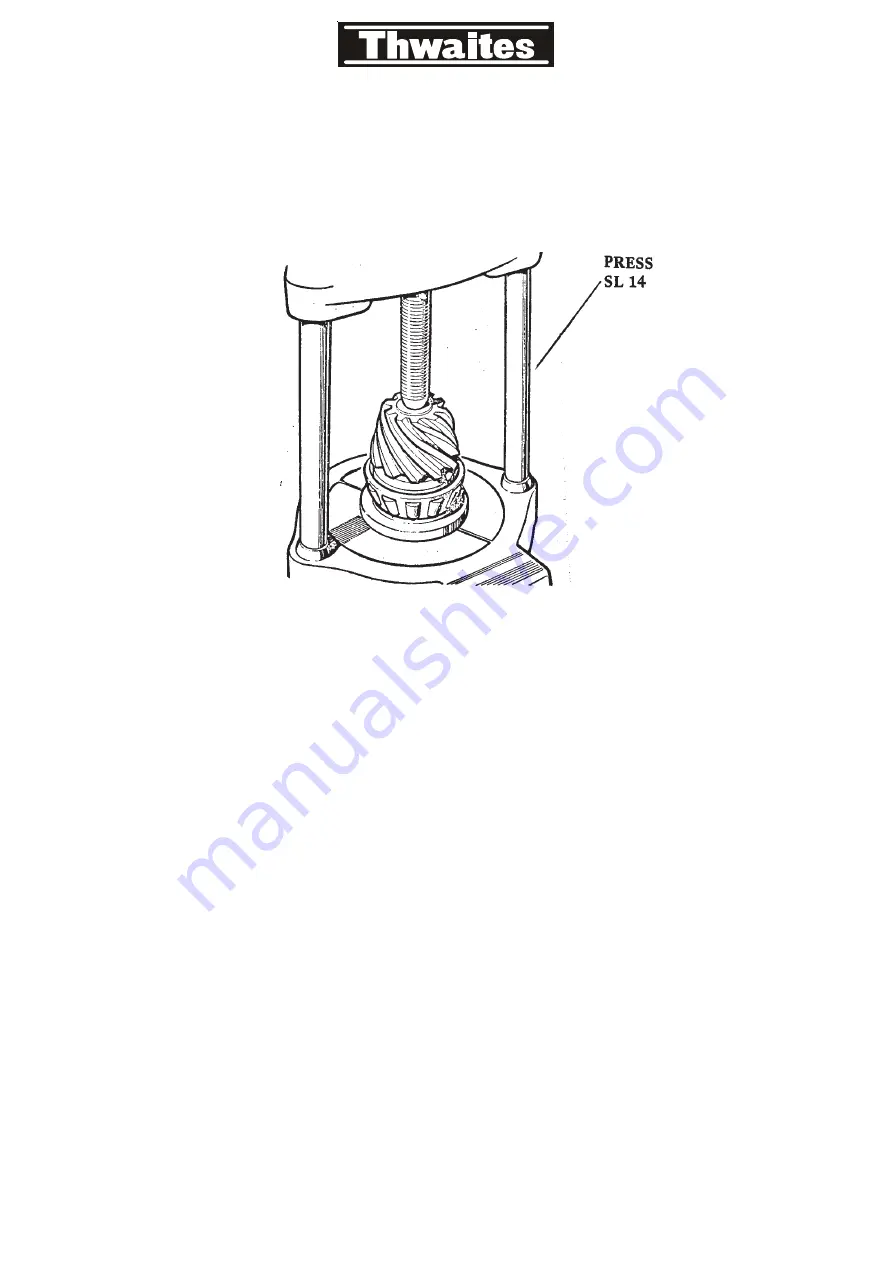
RE-ASSEMBLY OF PINION:
21. Check that pinion and gear are matched in that the serial number on the end face of
the pinion and on the outer diameter of the gears are identical. (It should be noted
that marks on the pinion end adjacent to serial number have no significance in
service.)
22. Assemble inner bearing cone onto pinion using service tool or suitable press.
23. Select new shim pack the size of that removed from the inner bearing. Insert into
carrier. Press inner bearing cup into housing, using press and suitable adaptor. (If
new gear set of bearings are used, the shim pack is to be chosen to give the correct
pinion height setting as described later.)
Fig. 9.
3-2-6
Summary of Contents for SPRITE NIMBUS
Page 1: ...SPRITE NIMBUS...
Page 6: ...B...
Page 7: ...Turn square headed screw in clutch back plate for adjustment 1 1...
Page 8: ...CLUTCH AND HOUSING 1 2...
Page 12: ...GEARBOX ASSEMBLY T5260 SPRITE NIMBUS...
Page 19: ...Axle Shaft End Float Measurement dial gauge shims 3 b...
Page 20: ......
Page 21: ...3 1 10...
Page 26: ...3 2 3...
Page 34: ...3 2 11...
Page 43: ...Drive Shaft Assembly Servicing...
Page 49: ...5 1...
Page 51: ...OLD TYPE TAPER STEERING COLUMN CHANGE NEW TYPE SPLINED 5 3...