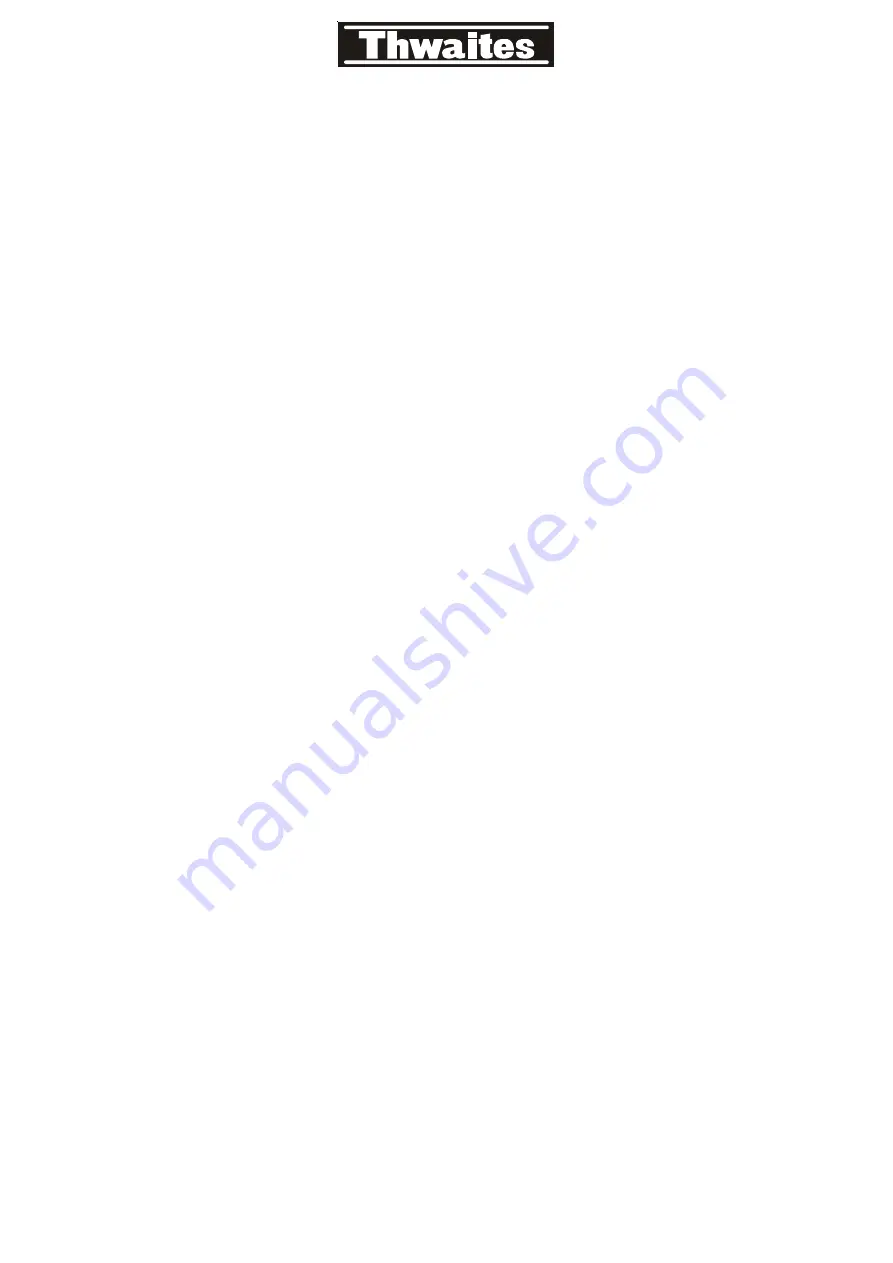
CORRECT MAINTENANCE SAVES MONEY
In our experience clean machines work better and successful plant operation
depends largely on the operator; his skill and efficiency Influence the speed of the
work and the safety of others. The operator must be allowed time for maintenance
and should be encouraged to take pride in his machine. The principle of one
machine/one operator should be adopted whenever possible. Regular maintenance
reduces the risk of breakdown and consequent loss of production and could prevent
costly repairs.
There are three important stages of maintenance:
1.
Daily check, usually by the operator, of the oil, fuel, water, tyres, brakes, steering
and controls. All defects. Including loose nuts and bolts, must be reported to the
plant manager. The machine should be cleaned daily.
2.
Weekly inspection by a competent mechanic incorporating the items checked daily
but in greater detail.
3.
Periodic servicing and overhaul in a workshop. Each stage of maintenance must be
carried out strictly in accordance with the manufacturer’s instructions, particularly
the engine, gearbox and axles.
PRACTICAL REMINDERS
1.
Spare grease should be kept covered, never use dirty grease.
2.
Use the correct grade of lubricating oil as recommended and see that funnels and
containers used are clean and dry. Do not mix different grades of oils and greases.
3.
Clean fuel and oil caps and oil filter covers before re-assembly.
4.
Do not dip rag or waste into the fuel tank.
5.
Pneumatic tyres must have the correct pressures maintained.
6.
Driving chains must be correctly adjusted.
7.
Hoses should be kept as straight as possible and must not chafe against rough
edges.
8.
Do not miss routine maintenance schedules, as detailed in handbook.
9.
Keep clear of unpropped skips whether they are hydraulically operated or otherwise.
Never work under a machine unless it is standing on hard ground. If a machine is
raised to Improve access substantial supports must always be placed under the skip
using main or track frame as base.
10. Any defects discovered during the daily check should be reported. Dangerous
machinery must be taken out of service until it can be repaired. Particularly with
machines on hire.
11. Check that brakes are working correctly before using the machine.
12. Brakes and driving chain to be correctly adjusted.
13. Oil Bath Air Cleaner to be checked every 60 working hours and oil to be changed
daily where severe and sandy conditions prevail.
Summary of Contents for SPRITE NIMBUS
Page 1: ...SPRITE NIMBUS...
Page 6: ...B...
Page 7: ...Turn square headed screw in clutch back plate for adjustment 1 1...
Page 8: ...CLUTCH AND HOUSING 1 2...
Page 12: ...GEARBOX ASSEMBLY T5260 SPRITE NIMBUS...
Page 19: ...Axle Shaft End Float Measurement dial gauge shims 3 b...
Page 20: ......
Page 21: ...3 1 10...
Page 26: ...3 2 3...
Page 34: ...3 2 11...
Page 43: ...Drive Shaft Assembly Servicing...
Page 49: ...5 1...
Page 51: ...OLD TYPE TAPER STEERING COLUMN CHANGE NEW TYPE SPLINED 5 3...