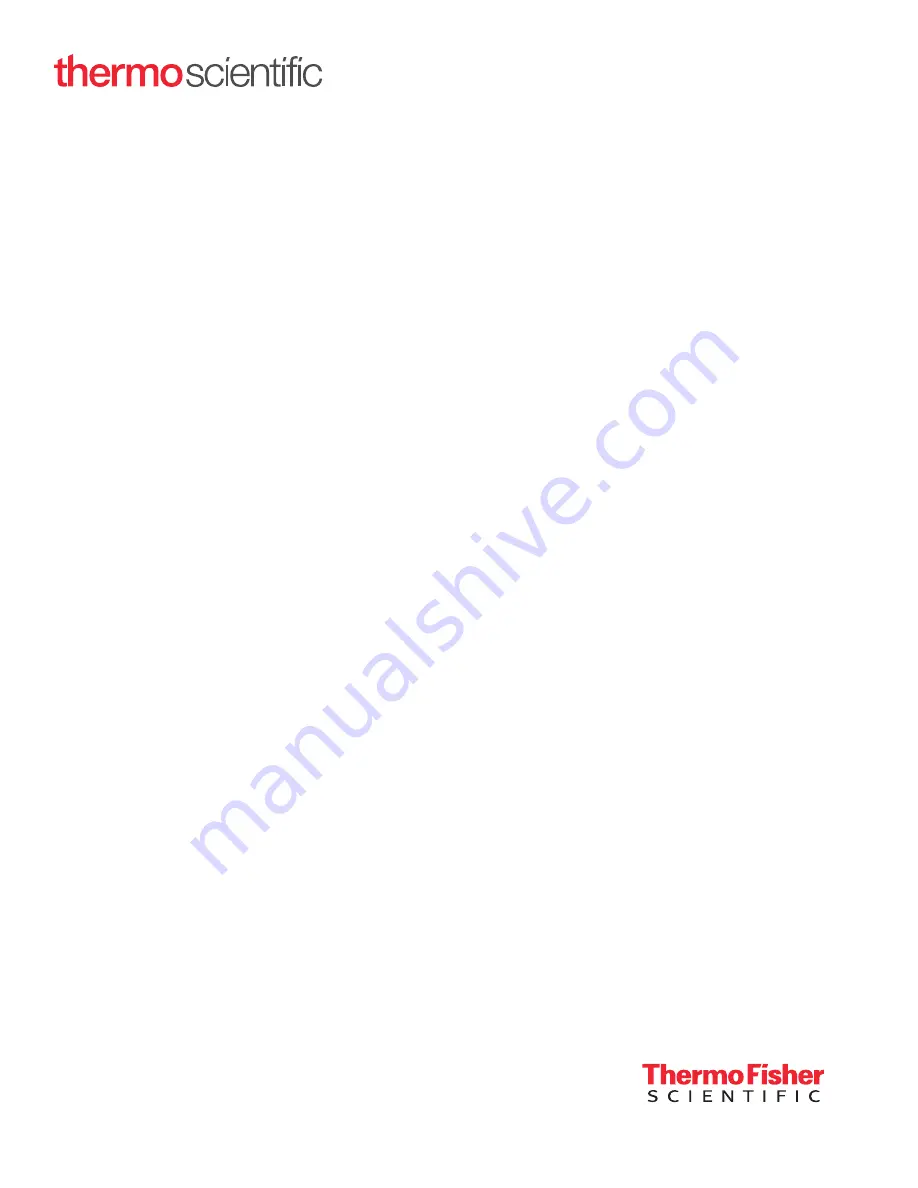
Find out more at
thermofisher.com/sut
For Research or Further Manufacturing. Not for diagnostic use or direct administration into humans or animals.
© 2020 Thermo Fisher Scientific Inc. All rights reserved. All trademarks are the property of Thermo Fisher Scientific and its
subsidiaries unless otherwise specified. Mettler Toledo is a trademark of Mettler Toledo. Sigma is a trademark of Merck KGaA,
Darmstadt, Germany and/or affiliates.
DOC0059 Revision A 0520