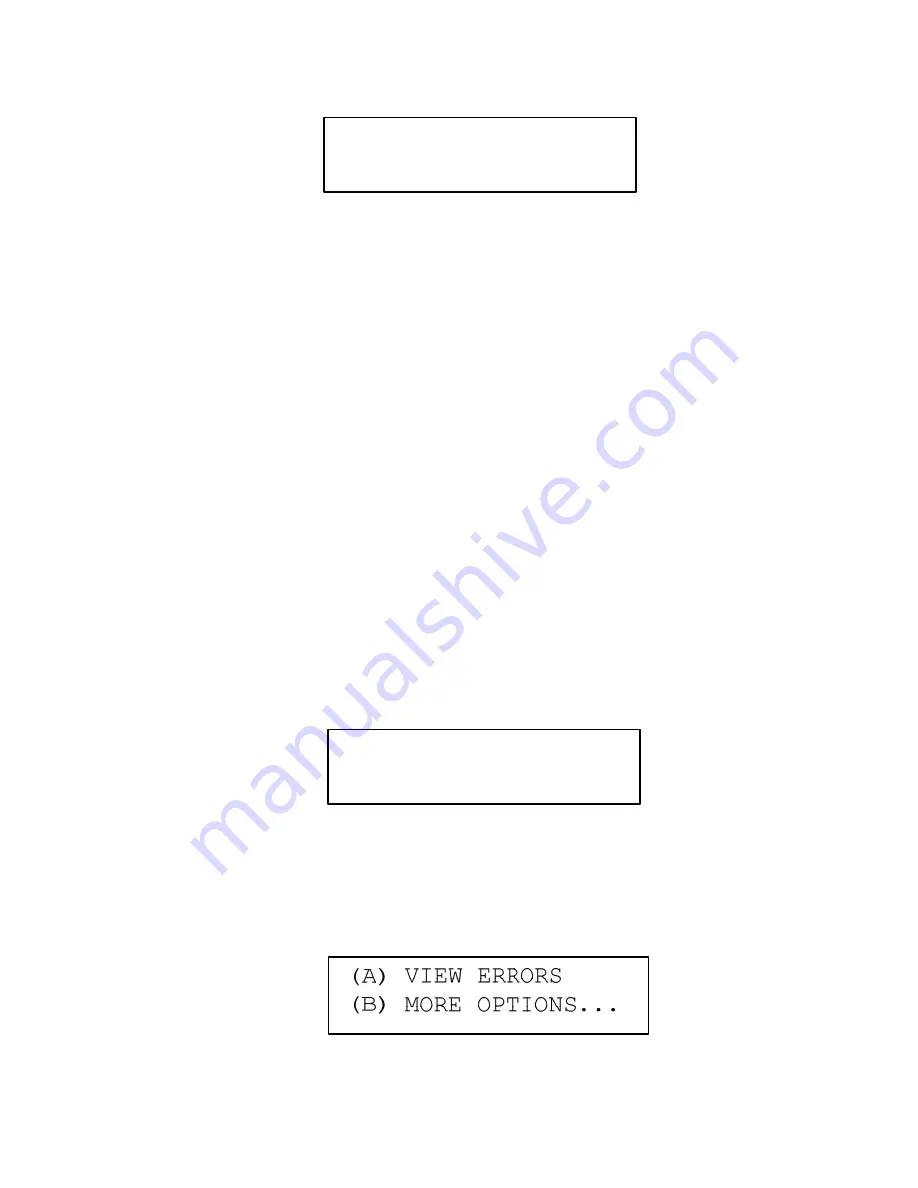
Basic Operation
Status Conditions
2-22
PDM 3600 Instruction Manual
Thermo Fisher Scientific
DONE 08:00 E
EOS: 1.75
Figure 2–35.
Sampling Complete
‑
Screen #1
The Sampling Complete Screen #1 contains the following information:
●
DONE
. This field contains the entire sample time duration
(minutes:seconds) for the first primary sample run.
●
EOS
. This field contains the total mass concentration value (mg/m
3
)
measured from the beginning of the first primary sample run.
When in the Sampling Complete - Screen #1, you can start another first
primary sample run, or you can view any status conditions (“errors”) that
may have occurred during the primary sample run. Refer to the following
section “Status Conditions” for more information on errors.
After 30 seconds of inactivity in the Sampling Complete Screen #1, the
PDM will turn off its LED display. Press the “A” button to reactivate the
LED display.
The TEOM 3600 PDM monitors its performance during a sample run and
registers any status conditions (errors) logged during the sample run(s). The
unit displays a blinking “E” in the upper right-hand corner of the First
Sample - Screen #1, Second Sample Screen, Sampling Complete - Screen
#1, and the Sampling Complete - Screen #2 to identify that a status code
(“error”) has occurred during an primary or programmed sample run
(
Figure 2–36
).
DONE 08:00 E
EOS: 1.75
Figure 2–36.
Screen with “E” in corner designating a status condition
The View Errors screen (
Figure 2–37
) allows users to view status conditions
(“errors”). Errors can be viewed both during the sample run and after the
sample run has ended.
Figure 2–37.
View Errors screen
Status
Conditions
View Errors Screen
Summary of Contents for 3600 PDM
Page 1: ...Model 3600 PDM Personal Dust Monitor Part Number 42 009904 8Oct2013...
Page 16: ......
Page 52: ......
Page 70: ......