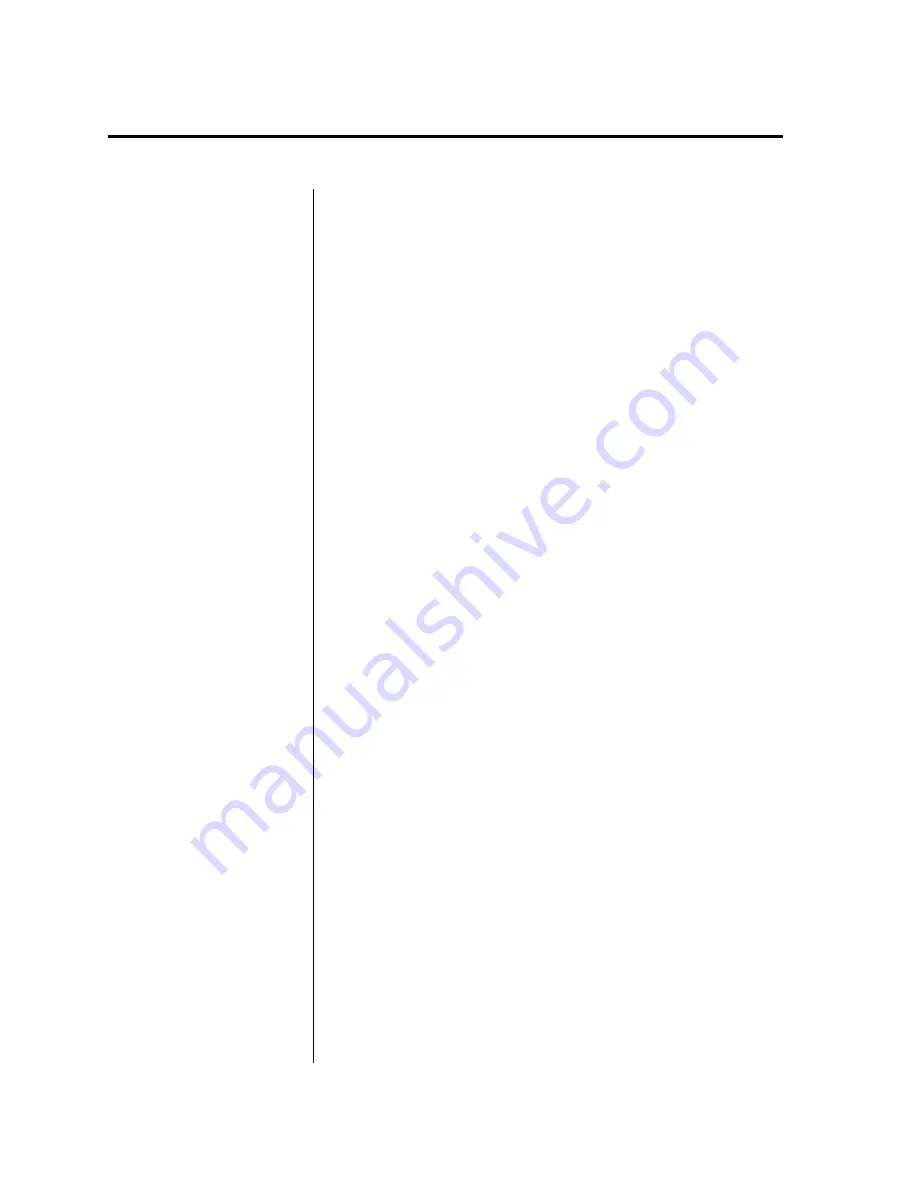
SERVICE
32
4.2 TROUBLESHOOTING GUIDE (continued)
2. Incorrect welding cable size
a. Use proper size and type of cable (see Table 2-A, page 5)
3. Improper input connections
a. Refer to Section 2.6
4. Electrode condition
a. Replace electrode
5. Remote amperage control (when applicable)
a. Check remote amperage control potentiometer and
connections. Repair or replace if necessary
D. Remote device completely inoperative
1. Remote control not connected or connected improperly to RE-
MOTE 14 receptacle
a. Connect remote control to REMOTE 14 receptacle
2. Remote control defective
a. Replace with known good device
E. Wandering arc; poor control of arc direction
1. Use of tungsten considerably larger than recommended
a. Use proper size tungsten (Refer toSection 3.5)
2. Improperly prepared tungsten
a. Prepare tungsten
3. Gas flow rate too high
a. Reduce flow rate
4. Drafts blowing shielding gas away from tungsten electrode
a. Shield weld zone from drafts
5. Loose gas fittings on regulator or gas line drawing air into weld
zone
a. Check and tighten all gas fittings
F. No high frequency
1. PROCESS SELECTOR switch not in HF TIG position
a. Place switch in the HF TIG position (see Section 3).
2. Drafts blowing gas shield away from tungsten.
a. Shield weld zone from drafts.
Summary of Contents for 400 GTSW AC/DC
Page 2: ......
Page 46: ...OPERATION 28 NOTES ...