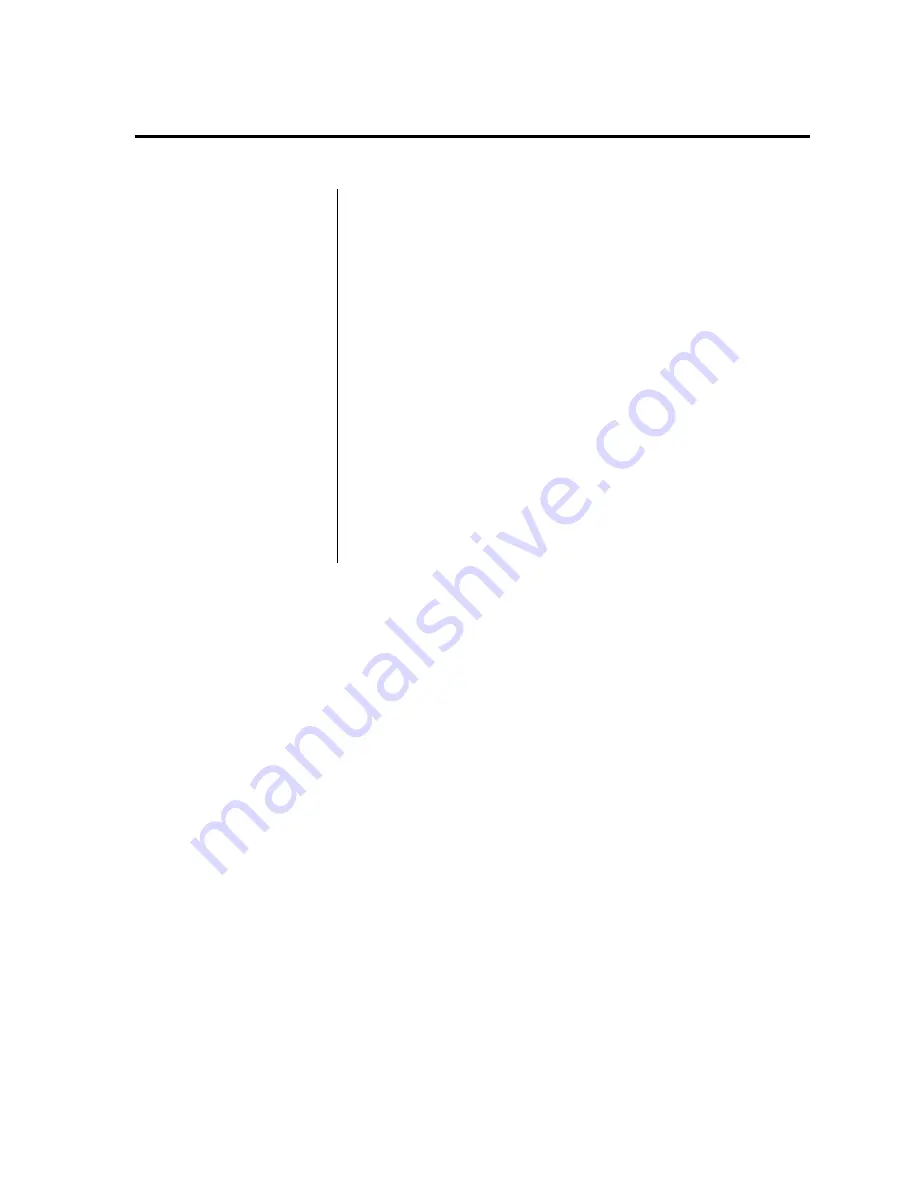
TABLE OF CONTENTS
Introduction
General Information
Installation
Operation
Service
Notes, Cautions, and Warnings ..........................................................i
Important Safety Precautions ............................................................ ii
Statement of Warranty .....................................................................xiv
1.1 Specifications................................................................................ 1
1.2 Duty Cycle .................................................................................... 2
2.1 Site Selection................................................................................. 3
2.2 Transporting Methods ................................................................ 4
2.3 Weld Output Connections .......................................................... 5
2.4 Shielding Gas Connections ........................................................ 8
2.5 Remote 14 Connections .............................................................. 9
2.6 Electrical Input Connections .................................................... 10
3.1 Operator Controls ...................................................................... 13
3.2 Sloper and Pulser Controls ...................................................... 19
3.3 Operating Precautions .............................................................. 22
3.4 Sequence of Operation .............................................................. 23
3.5 Electrode Preparation ............................................................... 26
3.6 Electrode Selection .................................................................... 27
4.1 General Maintenance ................................................................ 29
4.2 Troubleshooting Guide ............................................................. 30
Summary of Contents for 400 GTSW AC/DC
Page 2: ......
Page 46: ...OPERATION 28 NOTES ...