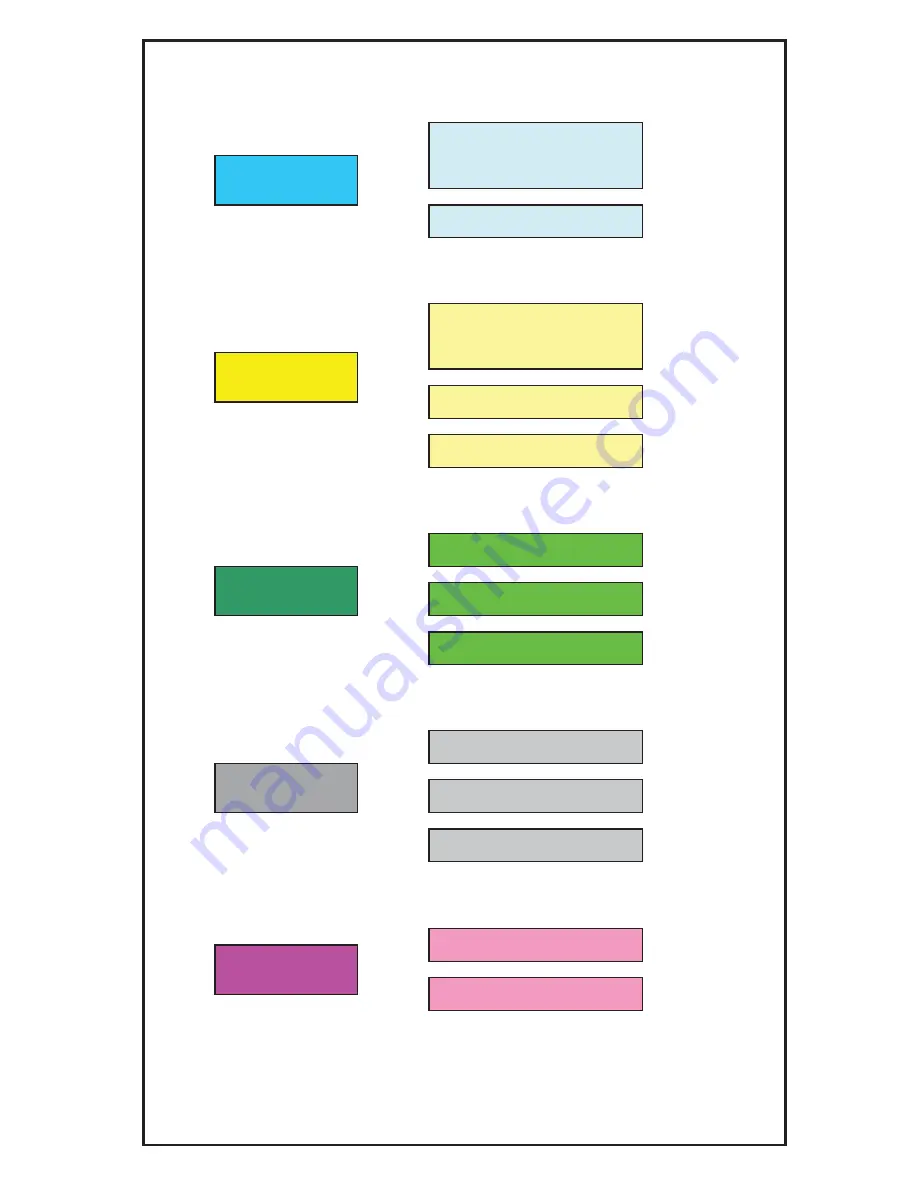
A
B
C
D
E
E1
Error codes
D2
Main Wiring Traction Version
Main Wiring Pad Assist
Relay and drive motor
electrical connections
Circuit boards
Electrical system
D3
Wiring diagram
D1
Brush head
A2
Replacing the brush motor
Checking brush motor current
imput,
Replacing the carbon brushes
A1
Measuring current draw and
replacing the carbon brushes
Replacing the suction motor
B1
Error codes
Troubleshooting
E2
Troubleshooting
Drive assembly
B2
Adjusting and replacing the
squeegee
Checking and replacing the
float
Tanks / Suction
Assembly
Drive motor - Idle wheels
B3
C1
Instrument panel board
C2
C3