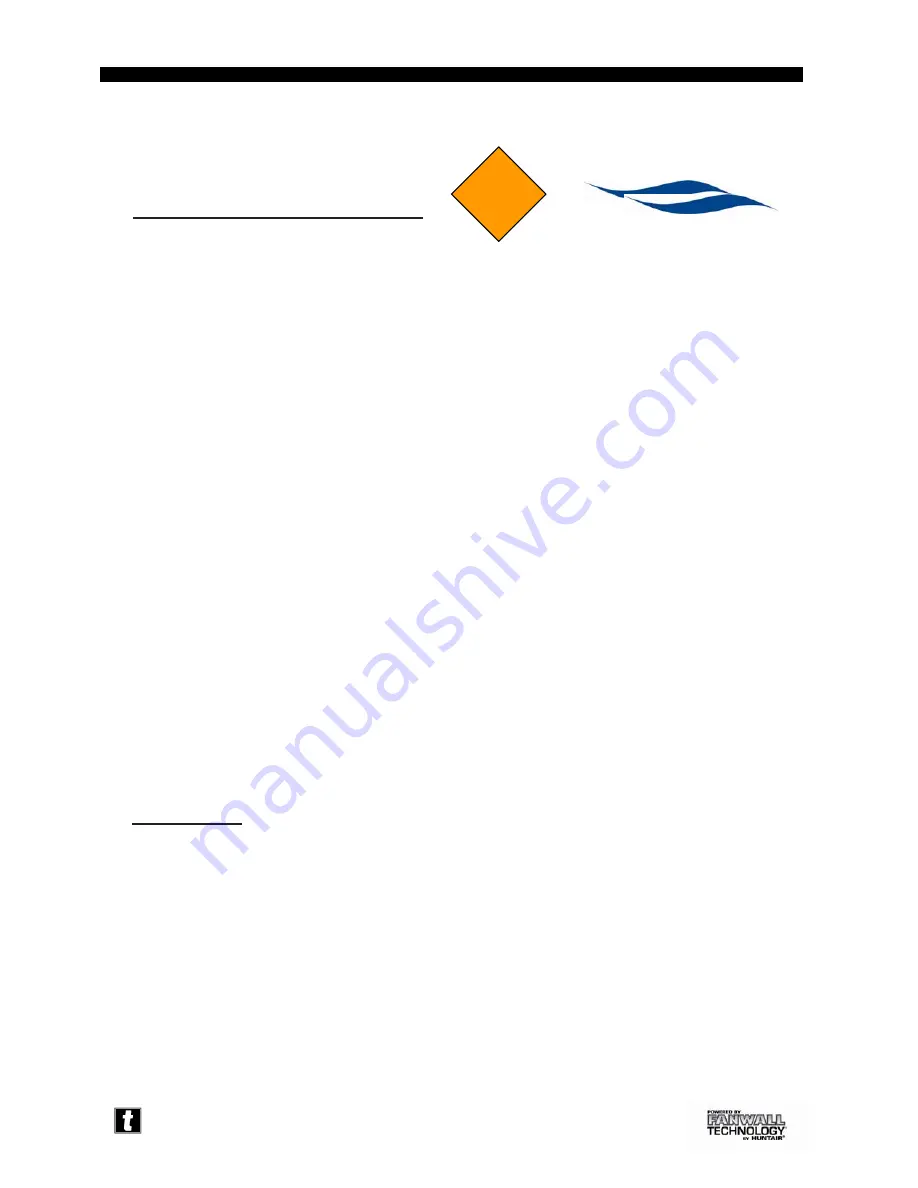
FWR/FWT 10
Page
7
Temtrol, Inc
.
®
Manufacturers of ….. Customized Air Handling Units
(D) INSTALLATION CODES / PRECAUTIONS
Installation Codes:
(1) Electrical characteristics are shown on each motor nameplate and inside left hand corner of
motor starter protector (MSP) lid for complete system.
(2) The unit shall be carefully installed in accordance with the standards of the National Fire
Protection Association (National Electrical Code). Authorities having jurisdiction should
be consulted before installations are made to verify local codes and installation procedures.
Installation Precautions:
(1) The services of qualified field service personnel are mandatory for safe and proper installation of
this equipment.
(2) The following clearances from combustible materials are to be maintained:
Top - 6", control side – 48" opposite controls - 6", bottom - 0".
If roof curb is provided by others, it must be at least 4" high and constructed from
non-combustible material.
(3) This unit is designed for installation on a level surface.
This is especially true if provided with an evaporative cooler.
(4) Do not locate the supply inlet opening within 10' of any exhaust discharge point or within 24" of
any obstruction.
(E) INSTALLATION
(1) Electrical Connections:
All electrical wiring and connections including electrical grounding must be made in
accordance with the latest edition of the National Electric Code . There may also be local
codes that apply.
a. The FWR/FWT nameplate and the drawings state the line voltage
and minimum ampacity requirements for this unit.
b. All external wiring must be within approved conduit and have a minimum
temperature rating of 75°C.
IMPORTANT:
If any of the original wire supplied with the unit must be
replaced, it must be replaced with type THHN 75°C wire
or its equivalent.
FWR
FWT