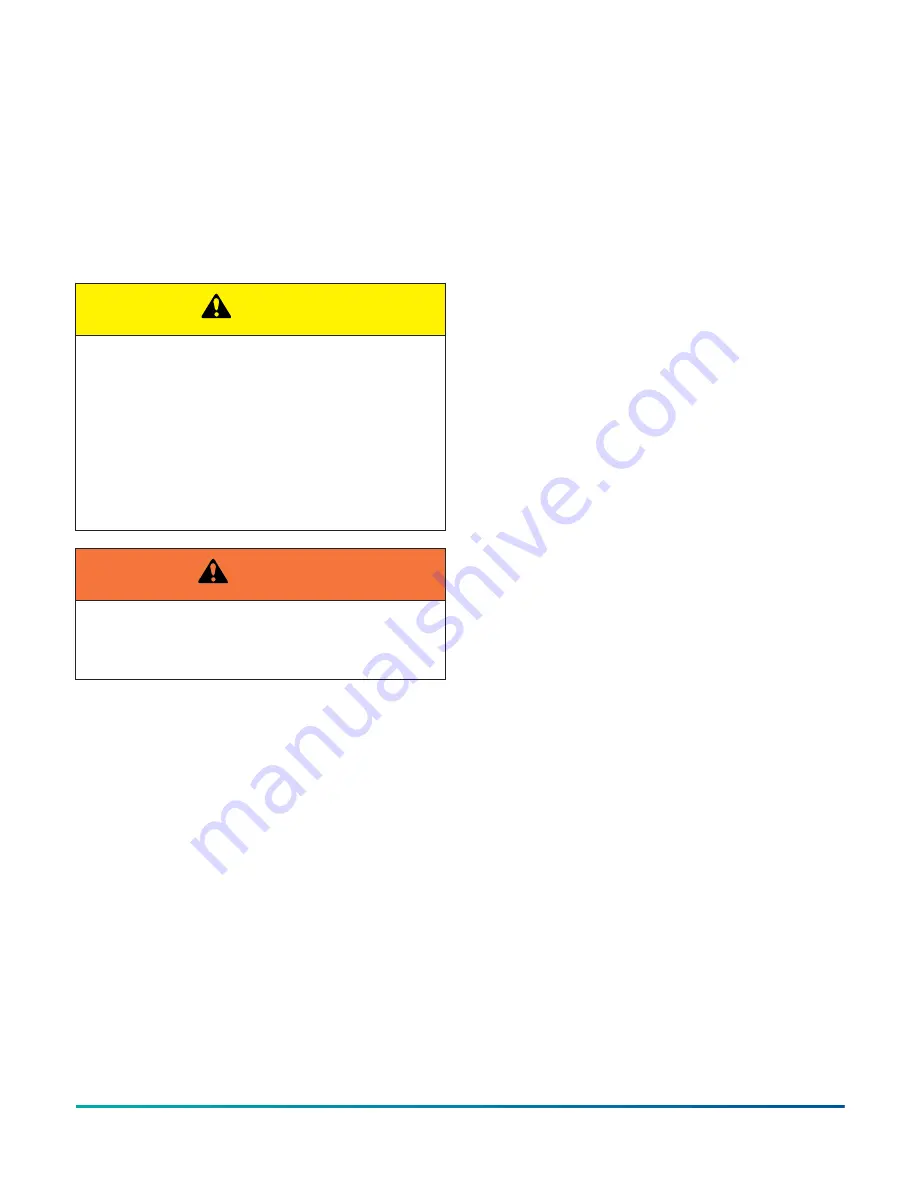
Installation
Unit inspection
Immediately upon receiving the unit, it should
be inspected for possible damage that may have
occurred during transit. If damage is evident,
it should be noted in the carrier's freight bill. A
separate written request for inspection by the
carrier's agent should be made.
CAUTION
To ensure warranty coverage, this equipment must be
commissioned and serviced by an authorized/ certified
Johnson Controls service mechanic or qualified
service person experienced in rooftop installation.
Installation must comply with all applicable codes,
particularly in regard to electrical wiring and other
safety elements such as relief valves, horsepower cut-
out settings, design working pressures, and ventilation
requirements consistent with the amount and type of
refrigerant charge.
WARNING
Lethal voltages exist within the control panels. Before
servicing, open and lockout-tag out all disconnect
switches.
Long term storage
When a unit(s) is stored for an extended period of
time, conduct a visual inspection of the entire unit
prior to start-up to ensure there are no signs of
damage, visible leaks, or obstructions.
Unit placement
If the unit installation will be elevated, consider the
following points:
•
Elevated roof curbs or dunnage steel can be
used to support the unit in order to raise it to
a specific height.
•
Catwalks or other forms of unit access may be
required to allow for ease of service.
•
Service clearances must be maintained at all
times.
•
Check with local officials to ensure the
application conforms to local codes and
regulations.
If the unit installation will be at ground level,
consider the following points:
•
Install the unit on a substantial base that will
not settle. Settling causes undue stress and
strain on refrigerant lines, which could cause
costly leaks in the refrigeration systems.
•
A one-piece concrete slab with footers
that extend below the frost line is highly
recommended.
•
The slab should be isolated from the main
building foundation. This helps to minimize
noise and vibration transmission into the
building.
•
The unit must be raised off the slab when
installing. This allows for the proper drainage
of condensate from the unit. The unit can be
permanently installed on top of the slab, if
the drain connection to the unit is connected
appropriately. No curb is required for slab
installation.
•
Service clearances must be maintained at all
times.
•
Check with local officials to ensure the
application conforms to local codes and
regulations.
Roof curb
Clearances and locations
•
Tempmaster offers an optional roof curb that
is specially designed for the Omni™ Premier
unit footprint.
•
If selected during the ordering process, the
roof curb is shipped to the site before the
unit. This allows time for curb assembly and
installation.
•
The curb must be properly sealed to prevent
air and water leakage.
•
Flexible collars must be used when connecting
the ductwork to the unit to prevent noise and
vibration being transmitted into the building.
•
The roof curb drawings contained in the
Tempmaster Omni™ Premier literature are not
intended as construction documents for field
fabricated curbs. Construction documents
for field fabricated curbs are available upon
request.
Tempmaster
®
Omni™ Premier 25 Ton to 80 Ton Rooftop Units Installation and Maintenance Guide
24
Tempmaster