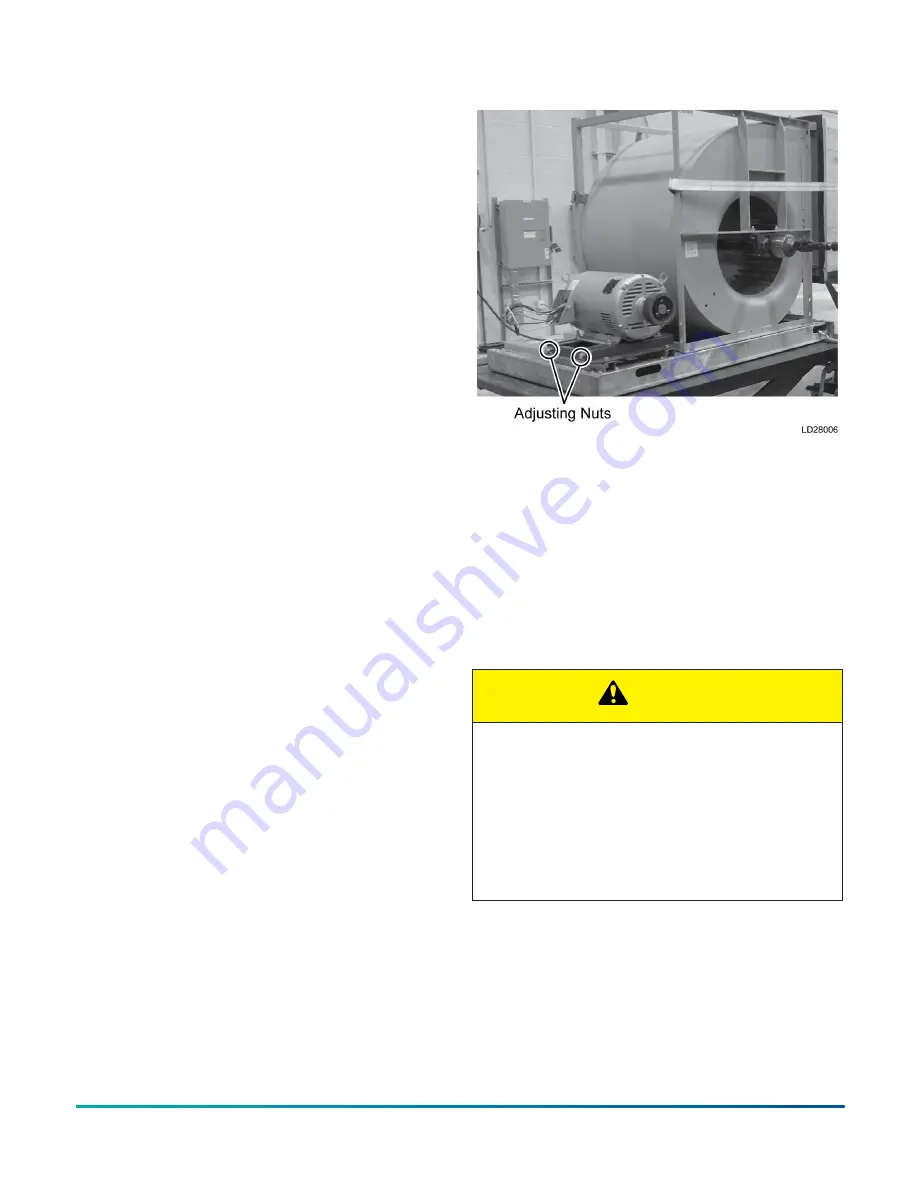
Belts
New belts should be re-checked after 24 hours of
operation. On multiple belt pulleys, the pitch depth
should be checked to ensure identical belt travel,
power transfer, and wear. Adjustable motor bases
are provided for belt adjustment.
Motor pulleys and blower shaft pulleys are locked
in position with either setscrews or split taper lock
bushings. All setscrews and/or taper lock bolts must
be checked for tightness and alignment before
putting equipment into operation.
An incorrectly aligned and tensioned belt
can substantially shorten belt life or overload
blower and motor bearings, shortening their
life expectancy. A belt tensioned too tightly can
overload the motor electrical, causing nuisance
tripping of the motor overloads and/ or motor
failure and/or shaft failure.
For replacement belts, enter the unit’s serial
number in Parts Navigator on the
Navigator
®
customer portal to find the correct, unit-specific
belt.
Belt replacement
Always replace belts as a set. Follow the steps below
to replace belts:
1. Release the tension on the belts by loosening
the adjusting nuts on the motor base (Figure
2. Remove old belts and recheck the sheave
alignment with a straight edge or piece of
string.
3. Install the new belts on the sheaves.
Never use a screwdriver to place the belts on the
sheaves. This can permanently damage the belts.
Figure 66: Loosen adjusting nuts on motor base
Filter drier replacement
The filter drier must be replaced any time work is
performed on the refrigerant circuit. The rooftop
unit comes with sealed type (non-replaceable) core
standard or optional replaceable core.
If the unit is not equipped with the optional valve
package (suction, discharge, and liquid line valves
with replaceable core filter driers), the refrigerant
must be recovered with a recovery machine to
replace the filter drier.
CAUTION
When using the factory installed valve package to
perform a pump-down of the refrigerant system, do
not allow the scroll compressor to pump the low side
into a vacuum. Pump-down should be stopped when
suction pressure reaches 10 psig. The remaining
refrigerant must be removed using proper recovery
methods.Allowing a scroll compressor to pump into
a vacuum causes internal arcing of the compressor
motor, which results in compressor motor failure.
When the unit is equipped with a valve package,
the unit can be pumped down by closing the liquid
line ball valve (prior to the filter drier) while the unit
is running, initiating a unit pump-down. The unit
shuts off when the mechanical low-pressure switch
opens. When the unit shuts down, close the ball
valve located after the filter drier and remove power
from the unit to prevent the unit from running.
Tempmaster
®
Omni™ Premier 25 Ton to 80 Ton Rooftop Units Installation and Maintenance Guide
100
Tempmaster