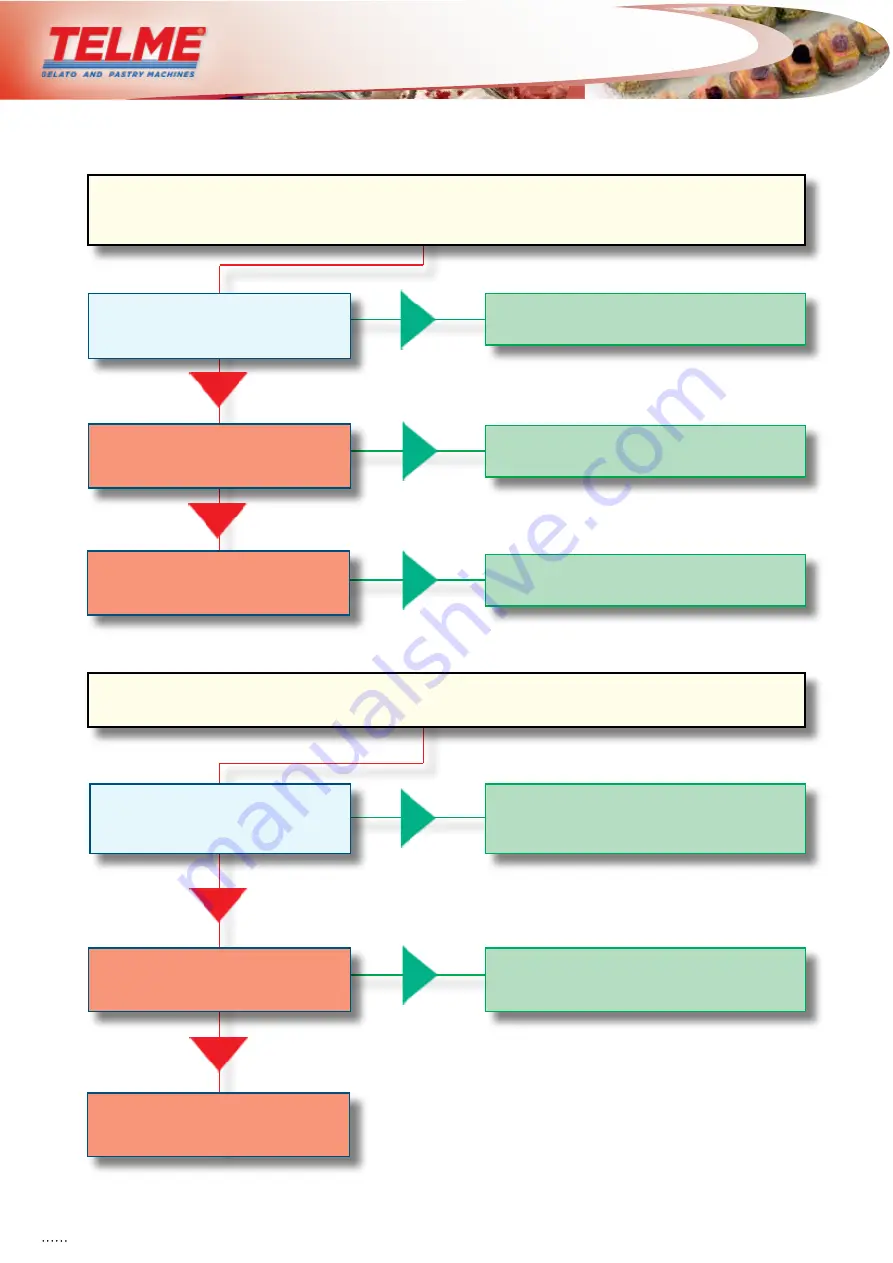
56
56
MACHINE REPEATEDLY TRIPS THE
ELECTRIC OVERLOAD SWITCHES OR BLOWS THE MAINS FUSES.
The capacity of the electrical sys-
tem is not sufficient to power the
machine.
Contact the Technical assistance
service.
YES
The electrical specifications of the
overload switches or fuses are not
suitable.
NO
YES
Machine internal fault.
NO
Contact the Technical assistance
service.
YES
Contact the Technical assistance
service.
UNUSUAL NOISE
Presence of solid products and/or
hardened deposits in the tank.
Stop the machine, wait until the mixture
has cooled, then empty the tank and
remove them.
YES
The mixing impeller motor is faulty.
NO
YES
NO
Stop the machine and contact the
Technical Assistance Service.
Contact the Technical assistance
service.
Summary of Contents for EVOPASTO 120
Page 2: ...2...