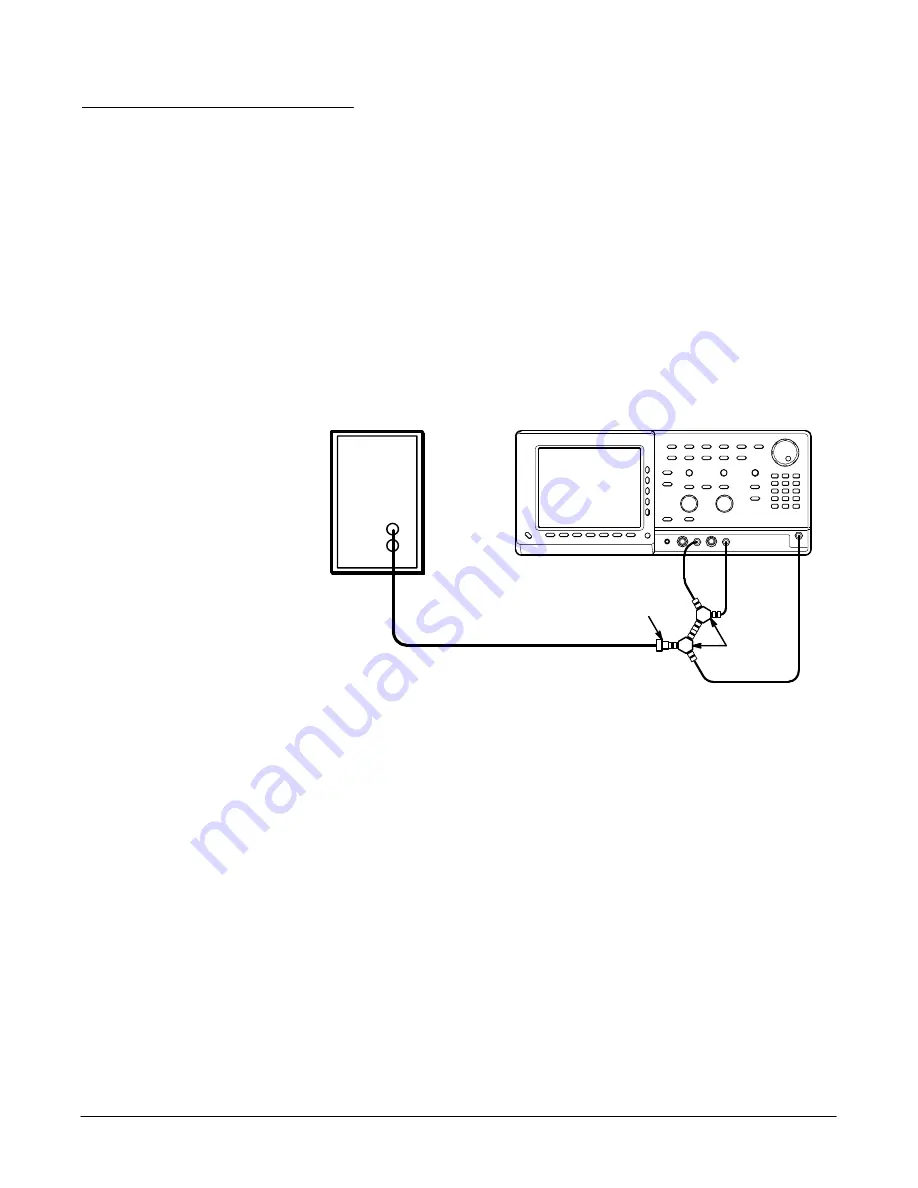
Performance Tests
TDS 820 Performance Verification
1Ć31
These procedures check those characteristics that relate to the Main and
Delayed time base system and are listed as checked under
Warranted Char-
acteristics in Section 1, Specification.
Check Accuracy of Delta Time Measurement Between
Channels
Equipment Required:
One high-frequency sine-wave generator (Item 15),
three 50
W
SMA cables (Items 3 and 4), two 50
W
power dividers (Item 12),
one SMA male to male adapter (Item 10), one BNC to SMA adapter (Item 8),
one N to BNC adapter (Item 11), and one precision coaxial cable (Item 2).
Prerequisites:
See page 1-11.
Procedure:
High
Frequency
Sine Wave
Generator
Output
SMA
Power
Dividers
BNC to SMA Adapter
Coaxial Cable
Figure 1-11: Initial Test Hookup
1.
Install the test hookup and preset the instrument controls:
NOTE
The two cables going to the CH 1 and CH 2 inputs must be the
same length and they must both connect to the same power divider.
a.
Hook up the test-signal source:
H
Connect, through an N to BNC adapter, a coaxial cable, and a
BNC to SMA adapter, the sine wave generator to 50
W
power
divider.
Time Base System
Checks
Summary of Contents for TDS 820
Page 4: ......
Page 6: ...Preface ii...
Page 12: ...Safety viii...
Page 13: ...Performance Verification Procedures...
Page 14: ......
Page 70: ...Performance Tests Performance Verification 1 56...
Page 71: ...Performance Tests TDS 820 Performance Verification 1 57...
Page 72: ...Specifications Replace this page with the tab divider of the same name...
Page 73: ......
Page 74: ...TDS 820 Performance Verification 2 1 Appendix B Specification...
Page 80: ...Product Description Appendix B Specification TDS 820 Performance Verification 2 7...
Page 81: ...Product Description Appendix B Specification Specification 2 8...
Page 91: ...Warranted Characteristics Appendix B Specification Specification 2 18...
Page 94: ...Typical Characteristics Appendix B Specification TDS 820 Performance Verification 2 21...