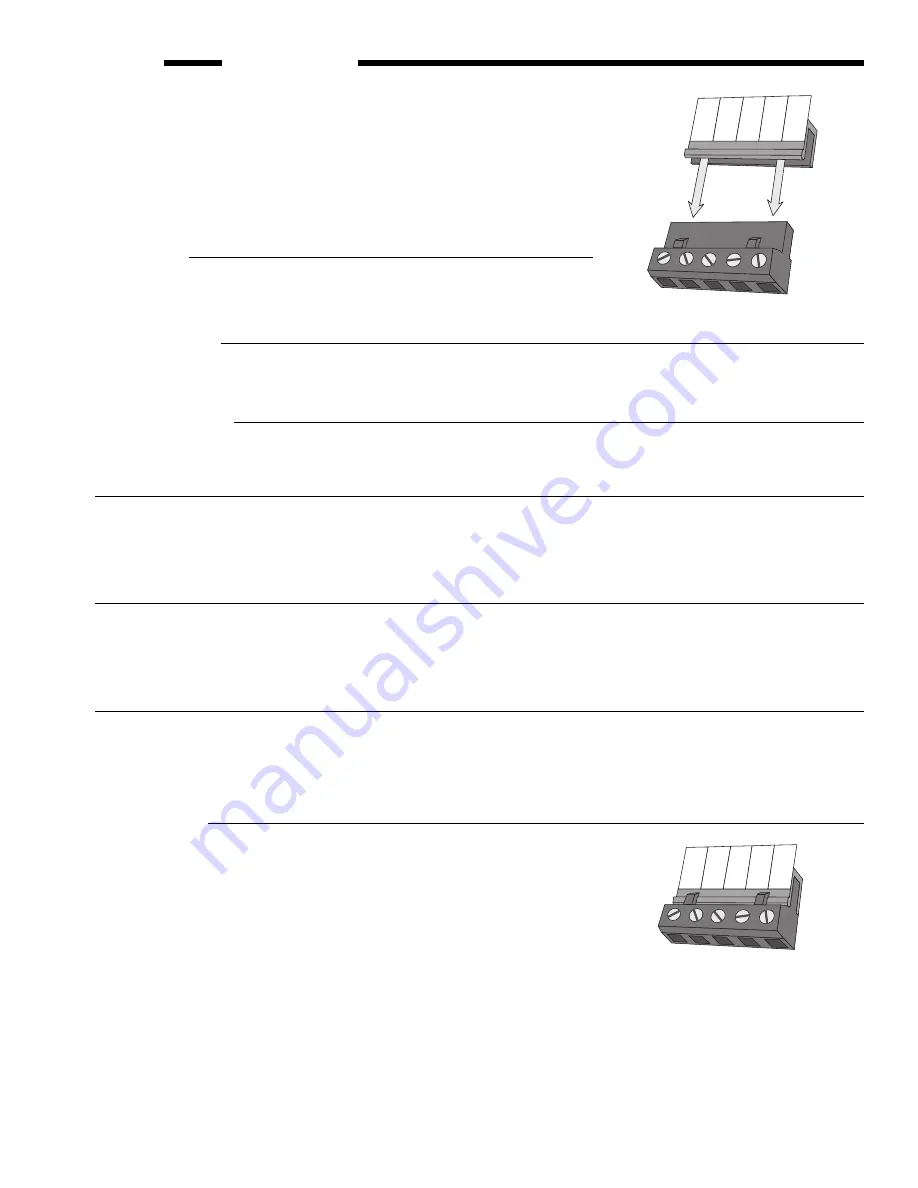
Step Five
Testing the wiring
Caution
• These tests are to be performed using standard testing practices and
procedures and should only be carried out by properly trained and
experienced persons.
• Before applying power to the control for testing, each terminal plug must be
unplugged from its header on the control. Pull straight down to unplug.
• A good quality electrical test meter, capable of reading from at least
0 — 200 Volts AC, and at least 0 — 1,000,000 Ohms, is essential to properly
test this control.
Test the sensors
• These tests must be made
before turning on the power supply, and with the
terminals unplugged.
• The sensors are to be tested according to the instructions in Brochure D 001.
Test the power supply
Make sure exposed wiring or bare terminals are not in contact with any other wires or grounded surfaces. Turn on the power to the
transformer and use an AC voltmeter to measure the voltage between terminals
Power C — R (1 and 2). 22 to 26 Volts AC should be
measured at these terminals.
Test the powered inputs
If an external Heat Demand or Setpoint Demand signal is used, power up the Heat or Setpoint Demand circuit and supply a Demand
signal to the control. Use an AC voltmeter to measure the voltage between terminals
Heat Dem (5 and 6). 22 to 26 Volts AC should be
measured at these terminals.
If a system pump circuit is connected to the
System Pmp (3 and 4) terminals; make sure power to the circuit is off and install a jumper
in the terminal plug between terminals (3 and 4). When the circuit is powered-up, the pump should operate. If it does not come on,
check the circuit wiring for errors and ensure that it is powered up and the voltage is correct. Check the devices in the circuit (pump,
switching relay, etc.) for faults. If the pump operates properly when the circuit is powered up, disconnect the power, remove the jumper
and proceed to the next step.
If a combustion air damper circuit is connected to the
Comb. Air (7 and 8) terminals; make sure power to the circuit is off and install
a jumper in the terminal plug between terminals (7 and 8). When the circuit is powered-up, the combustion air damper should operate.
If it does not come on, check the circuit wiring for errors and ensure that it is powered up and the voltage is correct. Check the devices
in the circuit (damper motor, switching relay, etc.) for faults. If the damper operates properly when the circuit is powered up, disconnect
the power, remove the jumper and proceed to the next step.
Make sure power to the Stage 1 boiler circuit is off and install a jumper in the terminal plug between the
Stage 1 (9 and 10) terminals.
When the circuit is powered-up, the boiler should operate. If it does not come on, check the circuit wiring for errors and ensure that
it is powered up and the voltage is correct. Check the devices in the circuit (limits, flow switches, etc.) for faults. If the boiler operates
properly when the circuit is powered up, disconnect the power, remove the jumper and check the remaining stages in the same way.
If all stages operate correctly, proceed to the next step.
9
Connect the control
Turn the power off and make sure all test jumpers have been removed from
the plugs.
Connect the plugs to the control by carefully aligning them with their respective headers
and pushing them upwards into the headers. The plugs should snap firmly into place.
The control wiring is now complete and has been tested. The control is ready for set-up
and operation.
Terminal plug pushed into
its header on the control
26
28
27
29 30
Com
Sen
UnO
Sw
Out
Sen
10K
Zone
Sup
Sen
Terminal plug disconnected
from its header on the control
26
28
27
29 30
Com
Sen
UnO
Sw
Out
Sen
10K
Zone
Sup
Sen
Caution
The tekmar Eight Stage Boiler Control 258 is an operating control and is not certified or intended for
use as a safety device.
Under no circumstances should safety limit devices be left disconnected after
installation of this control. The installer shall check all applicable code requirements and obtain
necessary inspections to ensure that the installation is in compliance with those requirements.
This Control operates remote devices such as pumps and combustion air dampers as well as the
boilers, and these devices may be started by the control at any time. Installers must install approved
electrical disconnects at these locations to allow these devices to be serviced safely.