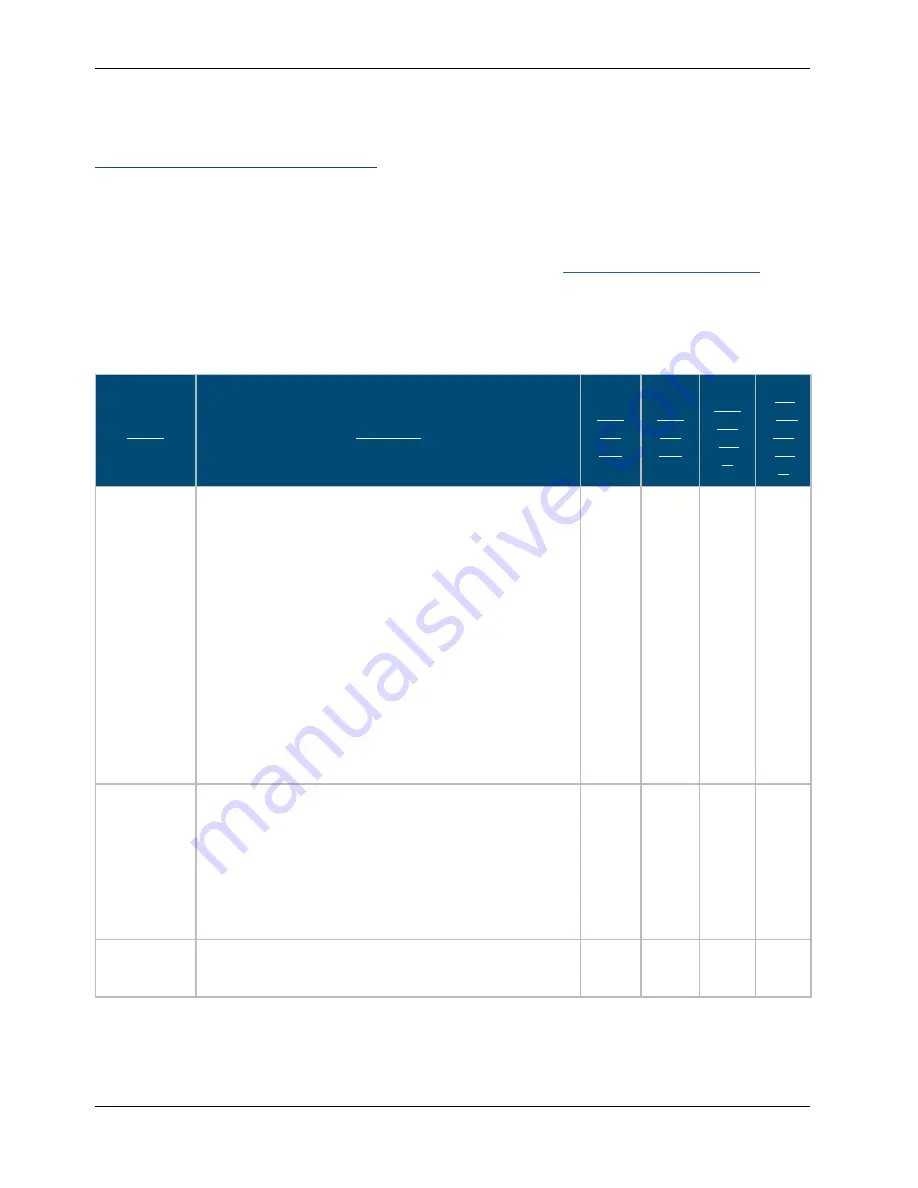
52
SAS UG 202205-01
Maintenance Guide
INSPECTION PROCESS AND SCHEDULE
PREVENTIVE MAINTENANCE PROGRAM
The following inspection routine and schedule is intended as a general guide for preventive maintenance of the Safety
Arm System. Factors such as weather, environment, geographical location, and individual usage will necessitate
different maintenance. If you are unsure as to how to perform these maintenance inspections or at what interval to
perform these inspections, please contact your Technical Support Team at
. Check
each routine and replace damaged or worn out parts if necessary.
Follow timetable below for maintenance (either in months (M) or hours (H)), in accordance with your Services’ current
maintenance practices and protocols.
ITEM
ROUTINE
1 M
OR
2 H
3 M
OR
6 H
6 M
OR
12
H
12
M
OR
24
H
Clamp
Block
9
Inspect the 4 hexagon screws of the clamp block
▪
If loose, or unscrewed, tighten screw
▪
If broken, the screw must be replaced
9
Inspect and tighten the 2 bolts under the clamp block
that hold the system on the cot/stretcher frame
9
Check fixed safety lock
▪
Ensure it is working properly and there are no par
-
ticles, obstacles, or debris
9
Check side safety lock pin
▪
Must be locked properly
9
Verify if the frame of the cot/stretcher is not cracked or
broken around the area of the clamp block
X
Arm -
Tubular
Pole
9
Verify all welds are intact, not cracked or broken
9
Verify not that the Arm is not bent, broken, or has da
-
maged components
9
Verify that the retaining post is secure
9
Verify that there is no excessive damage to Arm
9
Verify the Arm operates properly
X
Surface
Plate
9
Inspect the 4 bolts and nuts to secure the surface base
onto the surface plate
X