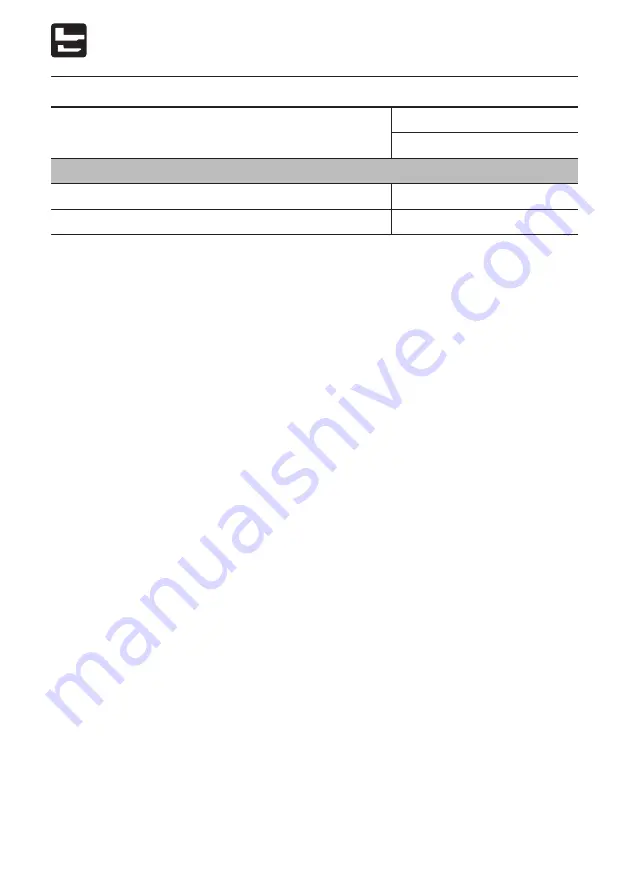
156
OPTIONS
Standard machine mass
(rubber crawlers, not including operator)
Cab
5950 (13120)
OPTION
Short dump body (Short vessel)
-65 (-143)
Air conditioner
15 (33)
Units: kg (lb)
*: Mass of optional equipment is added to the standard machine mass.
*: This table only contains the optional equipment of 10kg (20lb) or more in mass.
Optional Equipment Mass
Summary of Contents for TCR50
Page 6: ...4 ...
Page 8: ...6 ...
Page 35: ...33 SAFETY Safety Signs Decals ...
Page 36: ...34 SAFETY Safety Signs Decals ...
Page 64: ...62 ...
Page 84: ...82 ...
Page 85: ...83 TRANSPORT Loading and Unloading 84 Hoisting the Machine 85 Securing the Machine 86 ...
Page 147: ...145 SPECIFICATIONS Main Specifications 146 Machine Dimensions 148 Operating Range 150 ...
Page 149: ...147 MEMO ...
Page 150: ...148 SPECIFICATIONS Machine Dimensions ...
Page 152: ...150 SPECIFICATIONS Operating Range ...
Page 154: ...152 ...
Page 155: ...153 OPTIONS General Precautions 154 Optional Equipment Mass 156 ...
Page 159: ...157 INDEX ...