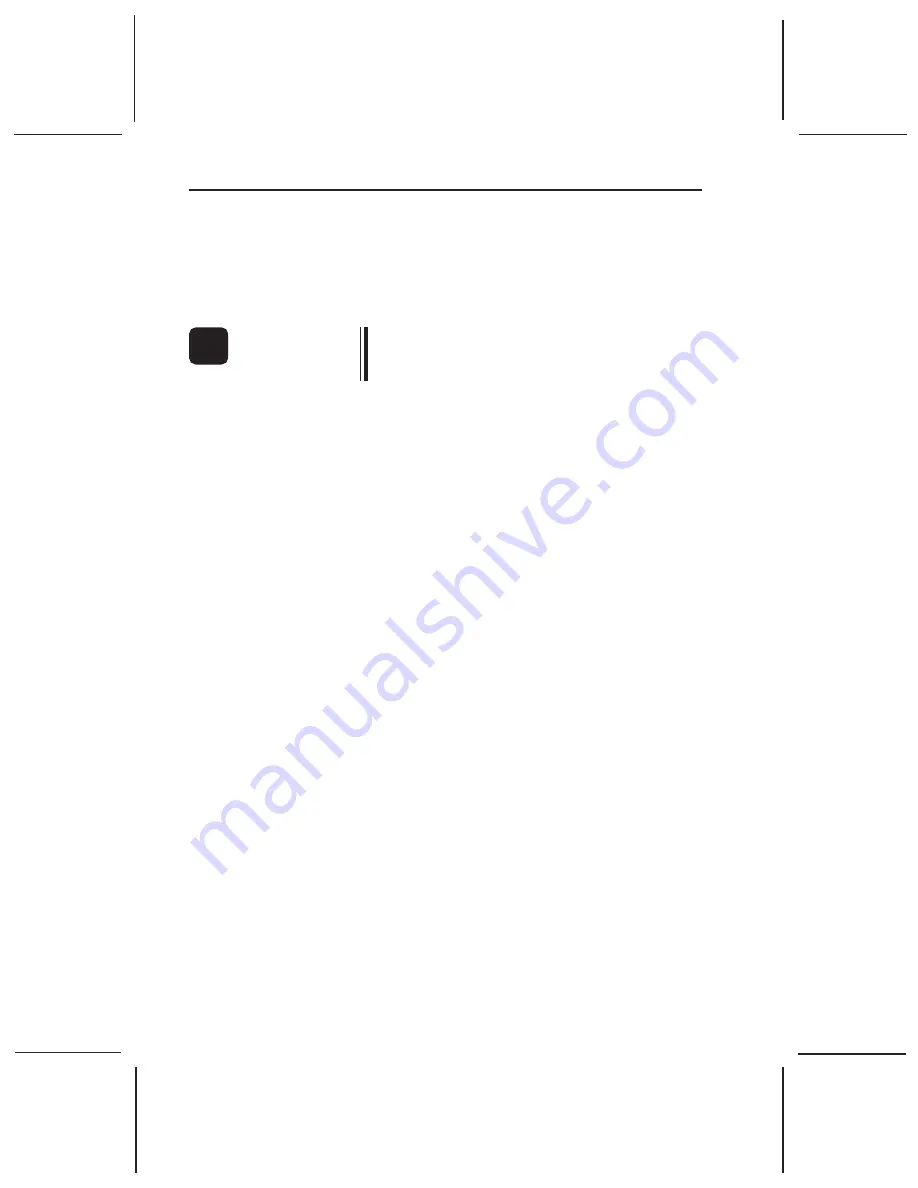
Appendix D
TA I
NSTRUMENTS
TGA 2950
D–20
4. Insert the transfer line and tighten the
Swagelok
TM
nut to seal the connector.
When you tighten the Swagelok
TM
nut, use a
3/8-inch wrench on the exhaust fitting flats
to prevent them from turning.
If the transfer line is not straight, or has
heavy oxide deposits on it, the sample tube
may be broken as the line is inserted.
!
W
ARNING
Summary of Contents for TGA 2950
Page 20: ...TA INSTRUMENTS TGA 2950 xx ...
Page 22: ...Introducing the TGA 2950 TA INSTRUMENTS TGA 2950 1 2 ...
Page 36: ...TA INSTRUMENTS TGA 2950 Installing the 2950 2 2 ...
Page 90: ...Running Experiments TA INSTRUMENTS TGA 2950 3 24 ...
Page 92: ...Technical Reference TA INSTRUMENTS TGA 2950 4 2 ...
Page 112: ...Technical Reference TA INSTRUMENTS TGA 2950 4 22 ...
Page 136: ...TA INSTRUMENTS TGA 2950 Maintenance and Diagnostics 5 24 ...
Page 142: ...Appendix B B 4 TA INSTRUMENTS TGA 2950 ...
Page 152: ...Appendix B B 14 TA INSTRUMENTS TGA 2950 Figure B 2 Figure B 3 ...
Page 153: ...TA INSTRUMENTS TGA 2950 B 15 Hi ResTM Option Figure B 4 Figure B 5 ...
Page 169: ...TA INSTRUMENTS TGA 2950 B 31 Hi ResTM Option Figure B 7 Figure B 8 ...
Page 188: ...Appendix B B 50 TA INSTRUMENTS TGA 2950 Figure B 11 Sensitivity Setting Too High ...
Page 205: ...TA INSTRUMENTS TGA 2950 B 67 Hi ResTM Option Figure B 16 Figure B 17 ...
Page 211: ...TA INSTRUMENTS TGA 2950 B 73 Hi ResTM Option Figure B 22 Figure B 23 ...
Page 212: ...Appendix B B 74 TA INSTRUMENTS TGA 2950 Figure B 24 Figure B 25 ...
Page 214: ...Appendix B B 76 TA INSTRUMENTS TGA 2950 ...
Page 216: ...Appendix C TA INSTRUMENTS TGA 2950 C 2 ...
Page 218: ...Appendix C TA INSTRUMENTS TGA 2950 C 4 Figure C 1 Auto TGA ...
Page 236: ...Appendix D TA INSTRUMENTS TGA 2950 D 2 ...
Page 258: ...Appendix D TA INSTRUMENTS TGA 2950 D 24 ...
Page 264: ...Index TAINSTRUMENTSTGA2950 I 6 ...