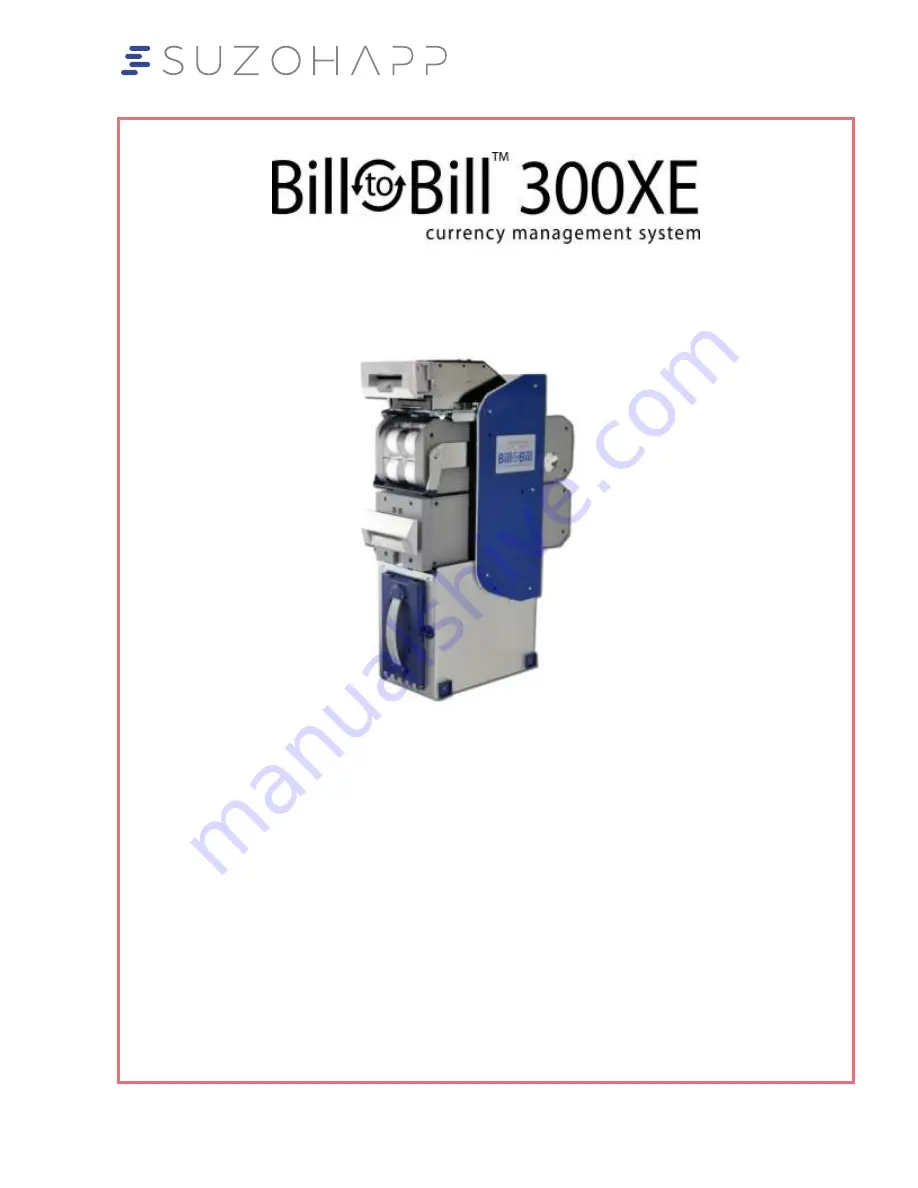
Rev. 2.4
- 1 -
© 2014 Suzo-Happ Group
Serviceability Manual
The information contained here-in is the property of Suzo-Happ Group and is not to be disclosed or used
without the prior written permission of Suzo-Happ Group. This copyright extends to all the media in which
this information may be preserved including electronic, printout or visual display.
Under no circumstances any part of this publication may be copied, transmitted, transcribed or distributed
in any form or by any means, or stored in a database or retrieval system, or translated into any language
(natural or computer) without the prior written permission of Suzo-Happ Group.
Suzo-Happ Group reserves the right to change the product specifications at any time. Also, Suzo-Happ
Group disclaims any liability for any direct or indirect losses arising out of use or reliance on this
information. This information is for guidance only.