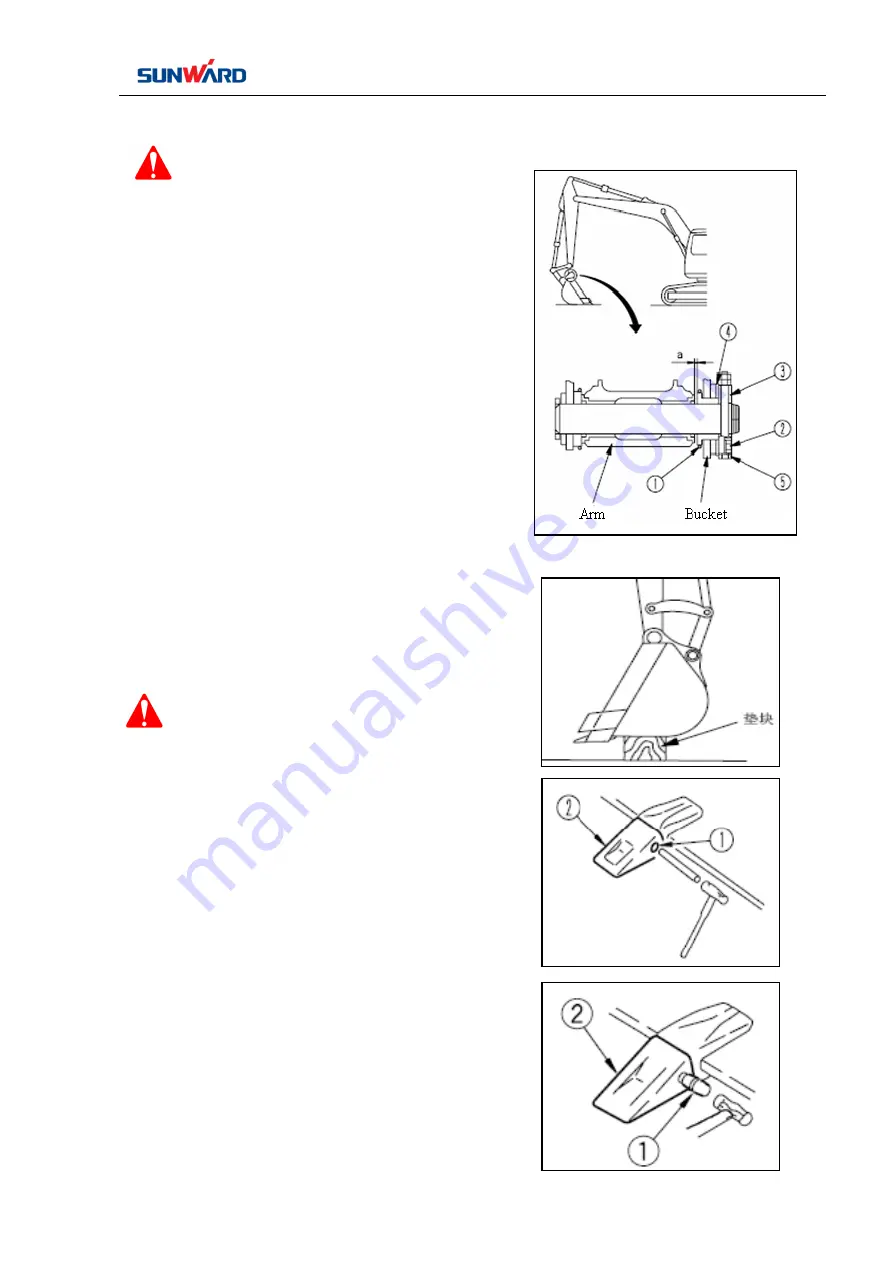
OPERATION & MAINTENANCE MANUAL SWE215F
147
Stop engine, set pilot safety lever to LOCK position.
Remove O-ring of link to measure clearance “a”.
Note
:
Move bucket to one side, or measure overall
clearance at one place, the measurement is a little
bit easy. (The position shown in fig is left position).
It's easy to measure correctly if using pin gauge.
Loosen 4 fixed bolt (2) and plate (3).
Remove shim (4) according to clearance “a” being
measured in previous step.
【
for instance
】
For clearance of 3mm, remove 1 pcs shim of 1.0mm
and 1 pcs shim of 0.5mm. The clearance will become
0.5 mm. for shim (4), use two types of 1.0mm and
0.5mm.
If the clearance is smaller than one shim, do not
attempt any maintenance operation.
Tighten 4 bots (2).
If it’s difficult to tighten bolt (2), to facilitate
tightening, pull out fixing pin bolt (5).
4.5.3.8 Replacing Bucket Teeth
Replace bucket teeth before bucket teeth holder wears out.
Warning
It's dangerous if the work equipment moves by
mistake when the teeth are being replaced. Set
the work equipment in s table condition, stop
the engine, and then set the pilot safety levers
securely to the LOCK position.
If the lock pin is knocked out by force, there is
hazard that pins may fly out. Check to ensure
nobody is in the surrounding area.
During replacement operation, there is hazard
of flying out pieces. So wear protective glasses,
gloves, and other protective equipment.
Lower the bottom surface of the bucket on a block,
check that the work equipment is in a stable condition,
then set pilot safety lever to the LOCK position.
Place a metal rod (diameter is a little smaller than pin)
Summary of Contents for SWE215F-5
Page 137: ...OPERATION MAINTENANCE MANUAL SWE215F 130 4 4 10 Hoses...
Page 170: ...OPERATION MAINTENANCE MANUAL SWE215F 163 5 TECHNICAL SPECIFICATION...
Page 174: ...OPERATION MAINTENANCE MANUAL SWE215F 167 5 1 4 SWE215F 5 Electrical Schematic...
Page 176: ...OPERATION MAINTENANCE MANUAL SWE215F 169 5 1 6 SWE215F 5 Hydraulic Schematic...
Page 178: ...OPERATION MAINTENANCE MANUAL SWE215F 171 6 NOTE FOR SAFETY...