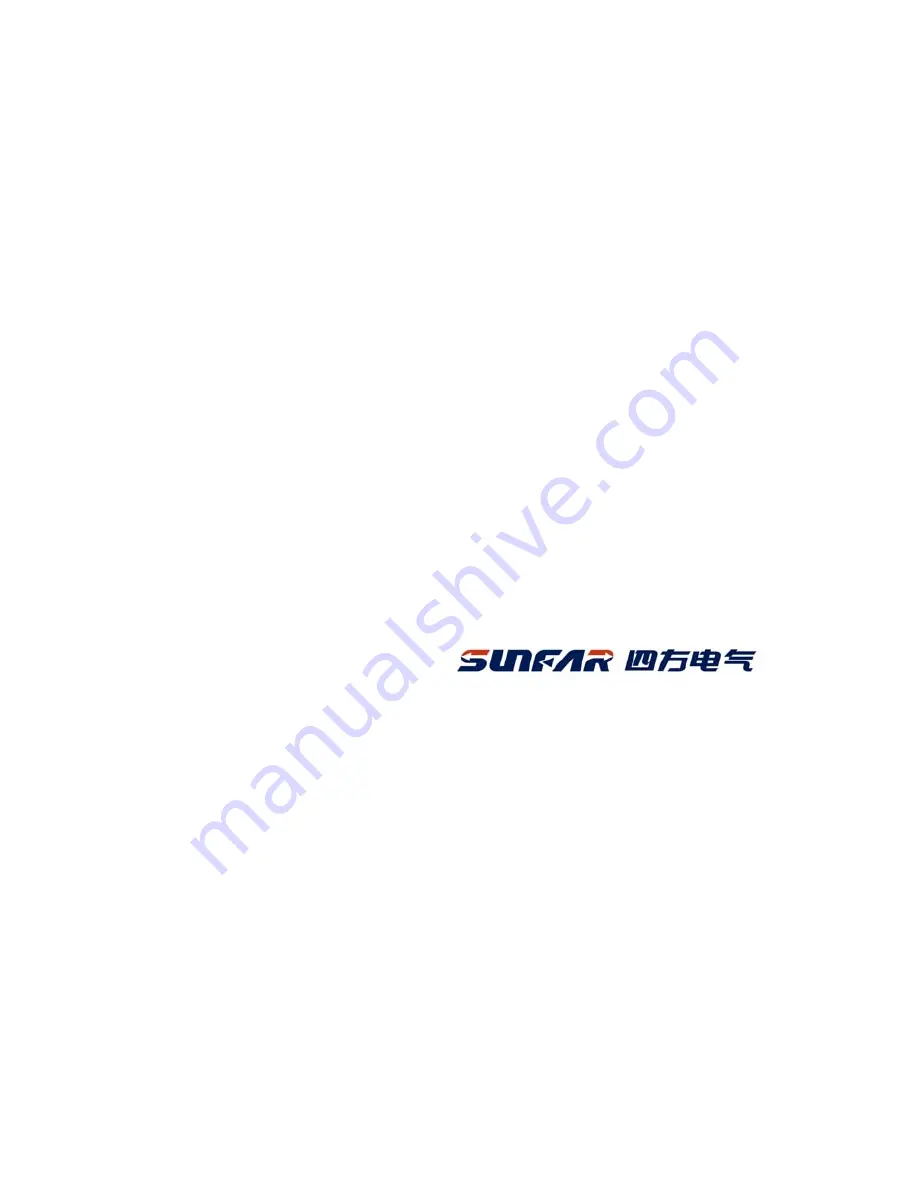
PREFACE
Thanks for choosing V260 Series High Performance Closed-Loop Vector Frequency
Inverter produced by Shenzhen Sunfar Electric Technologies Co, Ltd.
This Manual is the operating manual for V260 series closed-loop vector frequency
inverter. It provides all relevant instructions and precautions for installation, wiring,
functional parameters, daily care and maintenance, fault diagnosis and troubleshooting
of V260 series inverter.
In order to use this product correctly, guarantee product's best performance and ensure
safety of users and equipment, be sure to read this manual carefully before using V260
series inverters. Improper use may cause abnormity and malfunction of the inverter,
reduce its service life and even damage equipments and lead to personal injury and
death, etc.
This user manual is delivered with the device. Please keep it property for future
overhaul and maintenance.
Owing to constant improvement of products, all data may be changed without further
notice.
V260 Series High Performance Closed-Loop Vector Inverter User Manual
Version:
V1.1
Revision Date: JUNE 2015
This Manual is applicable to V6804