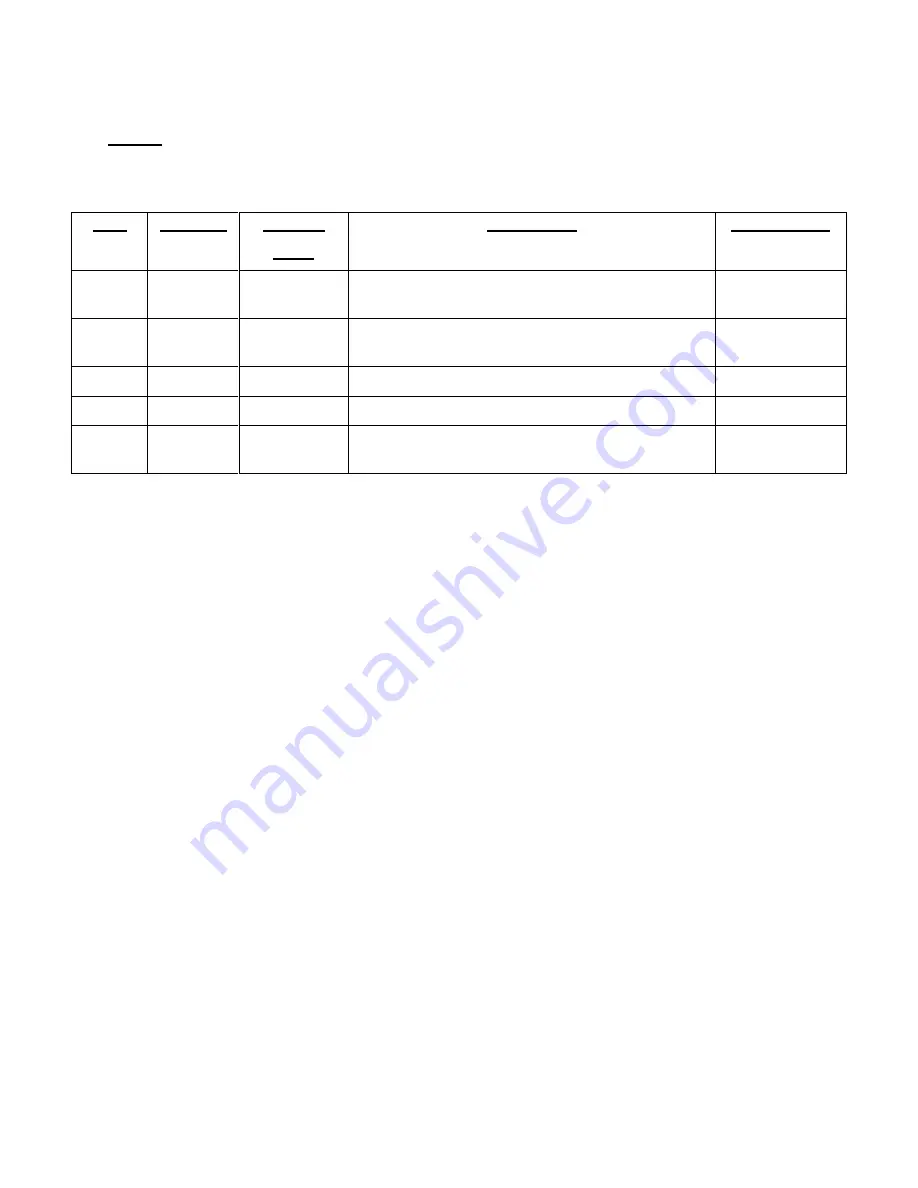
Parts
66
Cables
The following cables are available for use with the HC-4A Series Compressors as accessories
from SCAI.
Item
Quantity
For Use
With:
Description
Part Number
1
1
HC-4A/
HC-4A2
Accessory cable for remote On/Off,
6 m (20 ft.) long.
263887B20
2
1
HC-4A
Cold head cable, DE202/204SL, 3.3 m
(11 ft.) long
263941B11
3
1
HC-4A
Cold head cable, M204S, 3.3 m (11 ft.) long
264187B11
4
1
HC-4A
Cold head cable, CH204S, 3 m (10 ft.) long
267285C11
5
1
HC-4A2
Cold head cable, RDK-101, 3.3 m (11 ft.) long
268094C11
Summary of Contents for HC-4A
Page 2: ......
Page 6: ...iv This page is intentionally blank ...
Page 10: ...4 This page is intentionally blank ...
Page 12: ...6 This page is intentionally blank ...
Page 14: ...8 This page is intentionally blank ...
Page 36: ...30 This page is intentionally blank ...
Page 38: ...32 This page is intentionally blank ...
Page 59: ...Troubleshooting 53 Figure 8 HC 4A Wiring Diagram Main Electrical Chassis and Components ...
Page 60: ...Troubleshooting 54 Figure 9 HC 4A2 Wiring Diagram Main Electrical Chassis and Components ...
Page 61: ...Troubleshooting 55 Figure 10 HC 4A and HC 4A2 Wiring Diagram Air Cooled Unit ...
Page 62: ...Troubleshooting 56 Figure 11 HC 4A Electrical Schematic ...
Page 64: ...Troubleshooting 58 Figure 13 HC 4A2 Electrical Schematic Air Cooled Unit ...
Page 68: ...Parts 62 Figure 15 Parts Identification for HC 4A 12 14 19 23 ...
Page 69: ...Parts 63 Figure 16 Parts Identification for HC 4A2 12 14 19 23 ...
Page 70: ...Parts 64 Figure 17 Parts Identification 29 28 30 31 ...