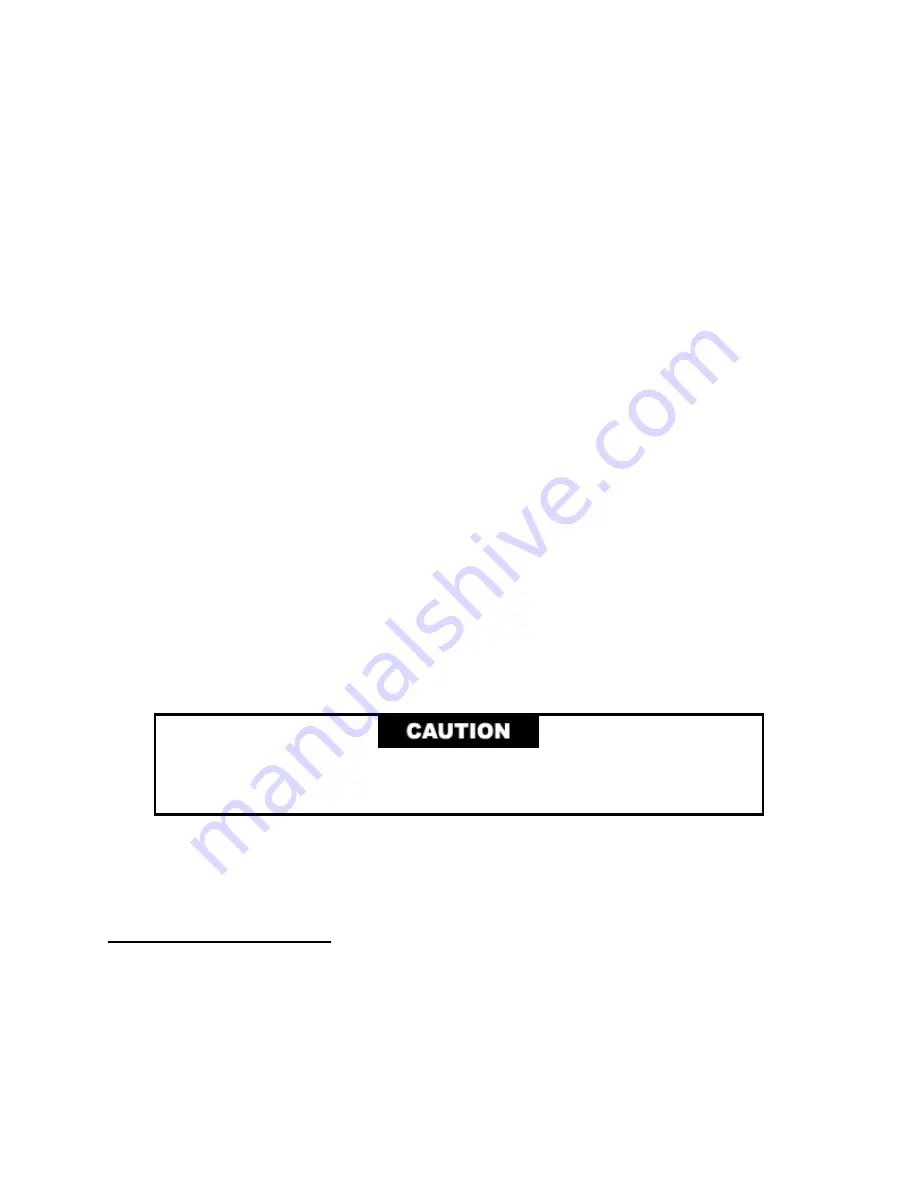
Maintenance
41
Leaks at welded joints require special skills to repair. Consult a SCAI Service Center.
Replacing worn or damaged parts can repair leaks at the self-sealing couplings. Vent the
compressor before beginning to disassemble it.
Tightening the coupling frequently stops leaks at threaded joints. Continued leakage after
tightening requires coupling repair. Install new O-rings or Teflon tape as required.
To repair a compressor coupling:
1.
Stop the compressor and disconnect the power to the compressor.
2.
Disconnect the gas line from the compressor coupling to be repaired.
3.
Install dust caps on all disconnected gas couplings except the one to be repaired.
4.
Remove the compressor’s cover.
5.
Use the Venting Procedure to Vent to Atmospheric Pressure to discharge all gas from
the
compressor. This procedure includes disconnecting
the
adsorber to prevent venting it.
6.
At the coupling to be repaired, hold the stationary part with one wrench. Use a second
wrench to disassemble the coupling.
7.
Remove the old O-ring.
8.
Wipe the O-ring groove to be sure it is clean. Lightly coat a new O-ring with vacuum grease.
Install the new O-ring.
9.
For a threaded joint sealed with Teflon tape, remove all old tape and apply new tape.
10.
Reassemble the coupling using two wrenches.
11.
Perform the Gas Cleanup procedure.
AVOID CONTAMINATION.
A leaking coupling on an adsorber should not be
repaired in the field. Consult a SCAI Service Center. Venting the adsorber will
introduce contaminants to the system that cannot be removed in the field.
NOTE
To repair a manifold assembly coupling, vent the manifold to atmospheric
pressure using adapter fitting P/N 266395C or 255919B2. Follow steps 6 to 11
above.
Coolant System Leak Repair
NOTE
Coolant system is sealed. For normal operation, no filling or draining
maintenance is required.
Summary of Contents for HC-4A
Page 2: ......
Page 6: ...iv This page is intentionally blank ...
Page 10: ...4 This page is intentionally blank ...
Page 12: ...6 This page is intentionally blank ...
Page 14: ...8 This page is intentionally blank ...
Page 36: ...30 This page is intentionally blank ...
Page 38: ...32 This page is intentionally blank ...
Page 59: ...Troubleshooting 53 Figure 8 HC 4A Wiring Diagram Main Electrical Chassis and Components ...
Page 60: ...Troubleshooting 54 Figure 9 HC 4A2 Wiring Diagram Main Electrical Chassis and Components ...
Page 61: ...Troubleshooting 55 Figure 10 HC 4A and HC 4A2 Wiring Diagram Air Cooled Unit ...
Page 62: ...Troubleshooting 56 Figure 11 HC 4A Electrical Schematic ...
Page 64: ...Troubleshooting 58 Figure 13 HC 4A2 Electrical Schematic Air Cooled Unit ...
Page 68: ...Parts 62 Figure 15 Parts Identification for HC 4A 12 14 19 23 ...
Page 69: ...Parts 63 Figure 16 Parts Identification for HC 4A2 12 14 19 23 ...
Page 70: ...Parts 64 Figure 17 Parts Identification 29 28 30 31 ...