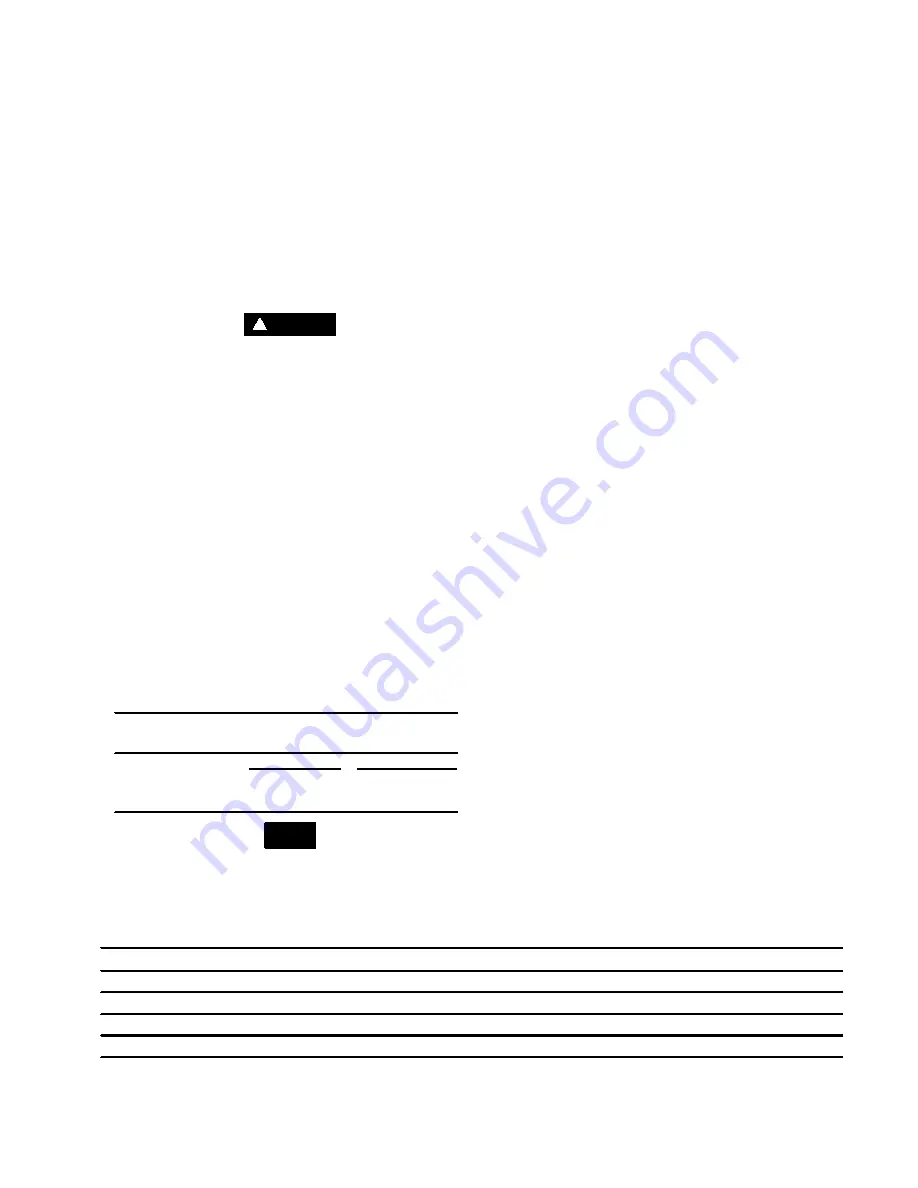
Section 4
INSTALLATION
21
4.1 MOUNTING OF COMPRESSOR PACKAGE
The compressor package should be placed over a
surface or foundation that is capable of supporting
its weight, while remaining level and free of deflec-
tions which may affect the driveline mounts or the in-
board pipework.
It is recommended that the package frame be lev-
eled and secured to the foundation with adequate
anchorage, and that a good grade grouting be used
to insure full contact between the load bearing sur-
faces.
DANGER
!
Do not twist frame.
The compressor/motor driveline is self--aligned by
the use of a rigid distance piece and supported by
flexible vibration isolation mounts. Poor leveling or
excessive deflections may adversely affect the op-
eration and longevity of these devices.
No piping loads should be transmitted to the air and
water connections provided with the package.
4.2 VENTILATION AND COOLING
For air--cooled compressors, select a location to
permit a sufficient unobstructed flow of air through
the compressor to keep the operating temperature
stable. The minimum distance that the compressor
should be from surrounding walls is three (3) feet
(0.91m). To prevent excessive ambient temperature
rise, it is imperative to provide adequate ventilation.
If ductwork is attached to cooler air discharge, the
high static fan option should be selected.
For water--cooled compressors, it is necessary to
check the cooling water supply. The water system
must be capable of supplying the following flows:
WATER TEMP.
WATER FLOW
_
F/
_
C
GPM/ LPM
125HP/90KW 150HP/110KW
70/ 21
80/ 27
18/ 68
22/ 83
25/ 95
30/ 114
NOTE
Water flow requirements are based on 80
_
F to
85
_
F (27
_
C to 29
_
C) water inlet temperature.
Recommended water pressure range is 25 to 75
psig (1.7 to 5.2 bar).
The table below indicates the ventilation require-
ments necessary to keep the compressor running at
a normal operating temperature. The fan air require-
ment is the volume of air which must flow through
the compressor for proper ventilation. The specified
heat rejection requirement is the amount of heat that
is radiated by the compressor. This heat must be re-
moved to assure a normal operating temperature.
With air--cooled compressors it is possible to use
this heat for space heating, providing no additional
pressure drop is created across the fan. Consult a
Sullair representative for assistance in utilizing this
heat.
DO NOT
install a water--cooled or an air--cooled/af-
tercooled compressor where it will be exposed to
temperature less than 32
_
F(0
_
C).
4.3 SERVICE AIR PIPING
Service air piping should be installed as shown in
. A s hut -- off v alv e s hould be ins t alled t o
isolate the compressor from the service line if re-
quired. Also notice that the service line should be
equipped with water legs and condensate drains
throughout the system.
4.4 SHAFT COUPLING CHECK
The compressor unit and motor are rigidly con-
nected via a cast adaptor piece which maintains the
shaft coupling in proper alignment. It is recom-
mended that prior to initial startup, all coupling fas-
teners are checked for proper tensioning. Refer to
Coupling S er v ic e P r oc edur es
Maintenance section of this manual.
4.5 FLUID LEVEL CHECK
The air compressor is also supplied with the proper
amount of fluid. However, it is necessary to check
the fluid level at installation. The level is checked by
looking at the sight glass located near the sump. If
the sump is properly filled, the fluid level should be
visible in the sight glass.
4.6 MOTOR ROTATION CHECK
After the electrical installation has been done, it is
necessary to check the direction of motor rotation.
Pull out the
EMERGENCY STOP
button and press
once, quickly and in succession, the
(START)
“
I
”
and
(STOP)
“
O
” pads. This action will “bump start”
the motor for a very short time. When looking at the
motor rear end, the driveline should be rotating
clockwise. If the reversed rotation is noted, discon-
nect the power to the starter and exchange any two
of the three power input leads, then re--check rota-
Cooling Type
Motor HP
Fan Air CFM
Heat Rejection to ventilating air BTU/min.
Applies to compressors with canopy only (vent fan).
125
150
16,400
16,400
6,081
7,527
125
150
2,845
2,845
1,340
1,340
(I)
(I)
VENTILATION REQUIREMENTS
(I)
(I)
6,081
7,527
Heat Rejection to water, BTU/min.
Air-cooled
Water-cooled
Summary of Contents for LS-20S
Page 6: ...NOTES...
Page 23: ...Section 3 SPECIFICATIONS 17 Figure 3 1A Identification Air cooled Model Prior to June 1 2000...
Page 24: ...Section 3 SPECIFICATIONS 18 Figure 3 1B Identification Air cooled Model After June 1 2000...
Page 25: ...Section 3 SPECIFICATIONS 19 Figure 3 1C Identification Water cooled Model...
Page 26: ...20 NOTES...
Page 31: ...25 NOTES...
Page 76: ...Section 8 PARTS LIST 70 8 16 ELECTRICAL BOX 1 2 3 4 5 6 7 8 9 10 11 12 13 14 15 16...
Page 84: ...Section 8 PARTS LIST 78 8 20 DECAL GROUP 1 2 3 4 5 6 7 8 9 10 11 12 13 14...
Page 86: ...Section 8 PARTS LIST 80 8 20 DECAL GROUP 15 16 17 18 19 20 21 22 23 24...
Page 88: ...Section 8 PARTS LIST 82 8 20 DECAL GROUP 25 26 27 28 29...
Page 90: ...Section 8 PARTS LIST 84 8 20 DECAL GROUP 30 31 32...
Page 92: ...Section 8 PARTS LIST 86 8 21 DECAL LOCATIONS 1 2 3 4 5 6 7 8 9 10 12 11 15 16 17 18 12 13 14...
Page 94: ...Section 8 PARTS LIST 88 8 21 DECAL LOCATIONS 9 1 2 3 4 5 6 7 8 10 11 WATER COOLED MODEL 12 13...
Page 96: ...Section 8 PARTS LIST 90 8 21 DECAL LOCATIONS 1 2 3 5 6 7 4...
Page 98: ...Section 8 PARTS LIST 92 8 22 WIRING DIAGRAM STANDARD FULL VOLTAGE SUPERVISOR II DELUXE...
Page 99: ...Section 8 PARTS LIST 93 8 23 WIRING DIAGRAM STANDARD WYE DELTA SUPERVISOR II DELUXE...
Page 100: ...Section 8 PARTS LIST 94 8 24 WIRING DIAGRAM STANDARD WYE DELTA SUPERVISOR II DELUXE EUROPE...
Page 101: ...NOTES...