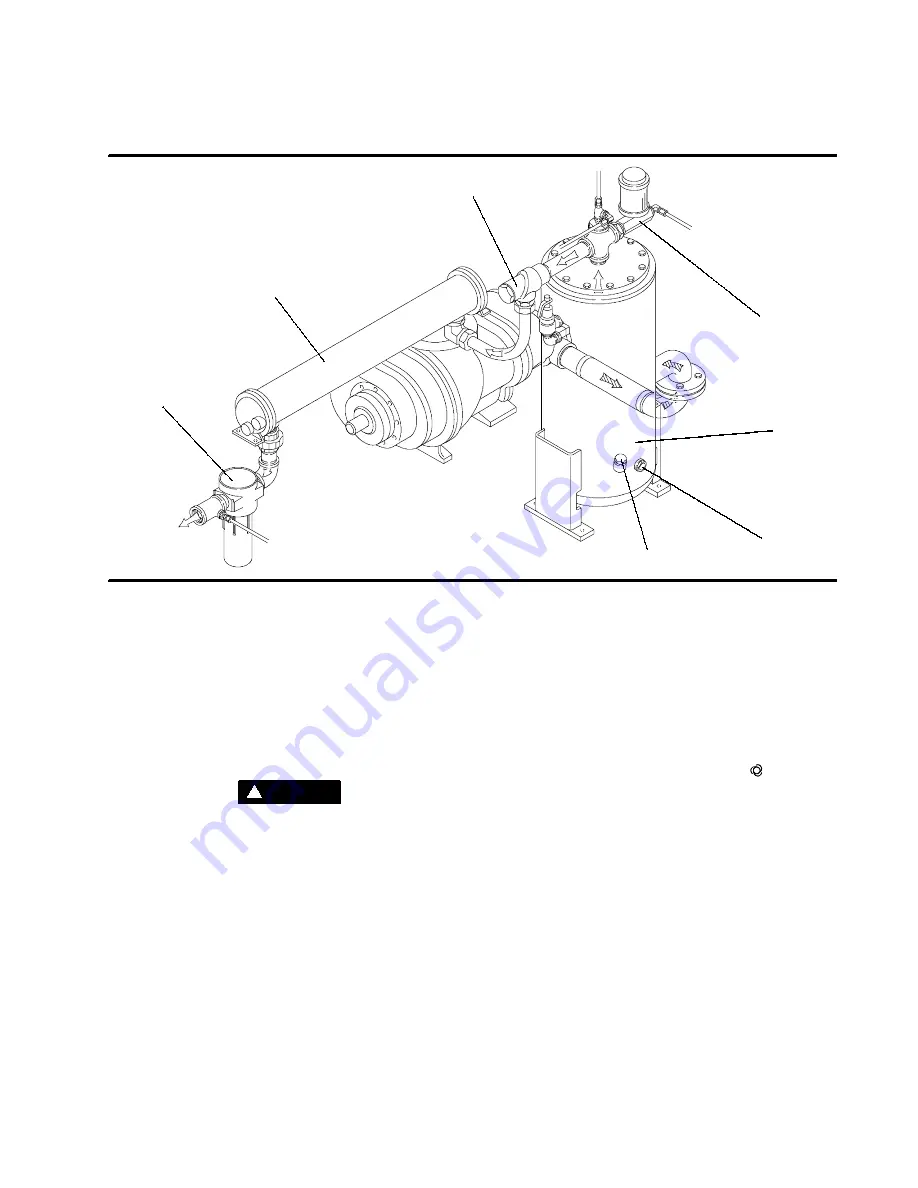
Section 2
DESCRIPTION
10
AFTERCOOLER
MOISTURE
SEPARATOR
SUMP
TANK
BLOWDOWN
VALVE
MINIMUM PRESSURE/
CHECK VALVE
WATER-
COOLED
MACHINES
FLUID FILL
PLUG
FLUID LEVEL
SIGHT GLASS
Figure 2-4B Compressor Discharge System Diagram- Water-cooled Model
See Supervisor II module functional description for
further details on shutdown pressure levels.
All Sullair compressor models are equipped with a
high pressure shutdown protection to shut down the
compressor at 20 psig (1.4 bar). This prevents the
pressure relief valve from opening under routine
conditions, thereby preventing fluid loss through the
pressure relief valve. A temperature switch will shut
down the compressor if the discharge temperature
reaches 240
_
F (115
_
C).
WARNING
!
DO NOT remove caps, plugs, and/or other com-
ponents when compressor is running or pressur-
ized.
Stop compressor and relieve all internal pressure
before doing so.
Fluid is added to the sump via a capped fluid filler
opening, placed low on the tank to prevent overfilling
of the sump. A sight glass enables the operator to
visually monitor the sump fluid level
2.6 CONTROL SYSTEM, FUNCTIONAL DESCRIP-
TION
. T he pur pos e of t he
compressor control system is to regulate the
amount of air being compressed to match the
amount of compressed air being used. The
capac-
ity control system
consists of a
Sullicon Control
,
a
butterfly valve
(located on the compressor air in-
let), a
pressure switch
,
pilot valve pressure reg-
ulator(s)
and a
control line filter
. The functional
description of the control system is described below
in four distinct phases of operation. For explanation
purposes, this description will apply to a compressor
with an operating range of 100 to 110 psig ( 6.9 to 7.6
bar). A compressor with any other pressure range
would operate in the same manner except stated
pressures.
START MODE -- 0 TO 50 PSIG (0 TO 3.5 BAR)
When the Supervisor II Module “
I
” or “ ” pad is de-
pressed, the unit starts and the pressure quickly
rises from 0 to 50 psig (0 to 3.5 bar). The pressure
regulator(s) and the pilot valve(s) remain closed,
and the Sullicon Control and spiral valve are inop-
erative.The spring on the control holds the butterfly
valve fully open via its spring--loaded lever arm. The
minimum pressure valve (MPV) isolates the com-
pressed air from reaching the service line while
building enough backpressure (40--50 psig [2.8--3.5
bar]) to maintain adequate lubricant fluid flow. If the
optional Closed Inlet Start assembly is provided, a
spring--loaded, single acting pneumatic cylinder
holds the butterfly valve almost fully closed, mini-
mizing the compression load for special drivers (i.e.,
Wye--Delta electric motors) during the start--up
phase. After a pre--determined amount of time, a so-
lenoid valve energizes the pneumatic cylinder and
the butterfly valve is thus opened fully. All further
Sullicon Control operation takes place with the
pneumatic cylinder energized.
Summary of Contents for LS-20S
Page 6: ...NOTES...
Page 23: ...Section 3 SPECIFICATIONS 17 Figure 3 1A Identification Air cooled Model Prior to June 1 2000...
Page 24: ...Section 3 SPECIFICATIONS 18 Figure 3 1B Identification Air cooled Model After June 1 2000...
Page 25: ...Section 3 SPECIFICATIONS 19 Figure 3 1C Identification Water cooled Model...
Page 26: ...20 NOTES...
Page 31: ...25 NOTES...
Page 76: ...Section 8 PARTS LIST 70 8 16 ELECTRICAL BOX 1 2 3 4 5 6 7 8 9 10 11 12 13 14 15 16...
Page 84: ...Section 8 PARTS LIST 78 8 20 DECAL GROUP 1 2 3 4 5 6 7 8 9 10 11 12 13 14...
Page 86: ...Section 8 PARTS LIST 80 8 20 DECAL GROUP 15 16 17 18 19 20 21 22 23 24...
Page 88: ...Section 8 PARTS LIST 82 8 20 DECAL GROUP 25 26 27 28 29...
Page 90: ...Section 8 PARTS LIST 84 8 20 DECAL GROUP 30 31 32...
Page 92: ...Section 8 PARTS LIST 86 8 21 DECAL LOCATIONS 1 2 3 4 5 6 7 8 9 10 12 11 15 16 17 18 12 13 14...
Page 94: ...Section 8 PARTS LIST 88 8 21 DECAL LOCATIONS 9 1 2 3 4 5 6 7 8 10 11 WATER COOLED MODEL 12 13...
Page 96: ...Section 8 PARTS LIST 90 8 21 DECAL LOCATIONS 1 2 3 5 6 7 4...
Page 98: ...Section 8 PARTS LIST 92 8 22 WIRING DIAGRAM STANDARD FULL VOLTAGE SUPERVISOR II DELUXE...
Page 99: ...Section 8 PARTS LIST 93 8 23 WIRING DIAGRAM STANDARD WYE DELTA SUPERVISOR II DELUXE...
Page 100: ...Section 8 PARTS LIST 94 8 24 WIRING DIAGRAM STANDARD WYE DELTA SUPERVISOR II DELUXE EUROPE...
Page 101: ...NOTES...