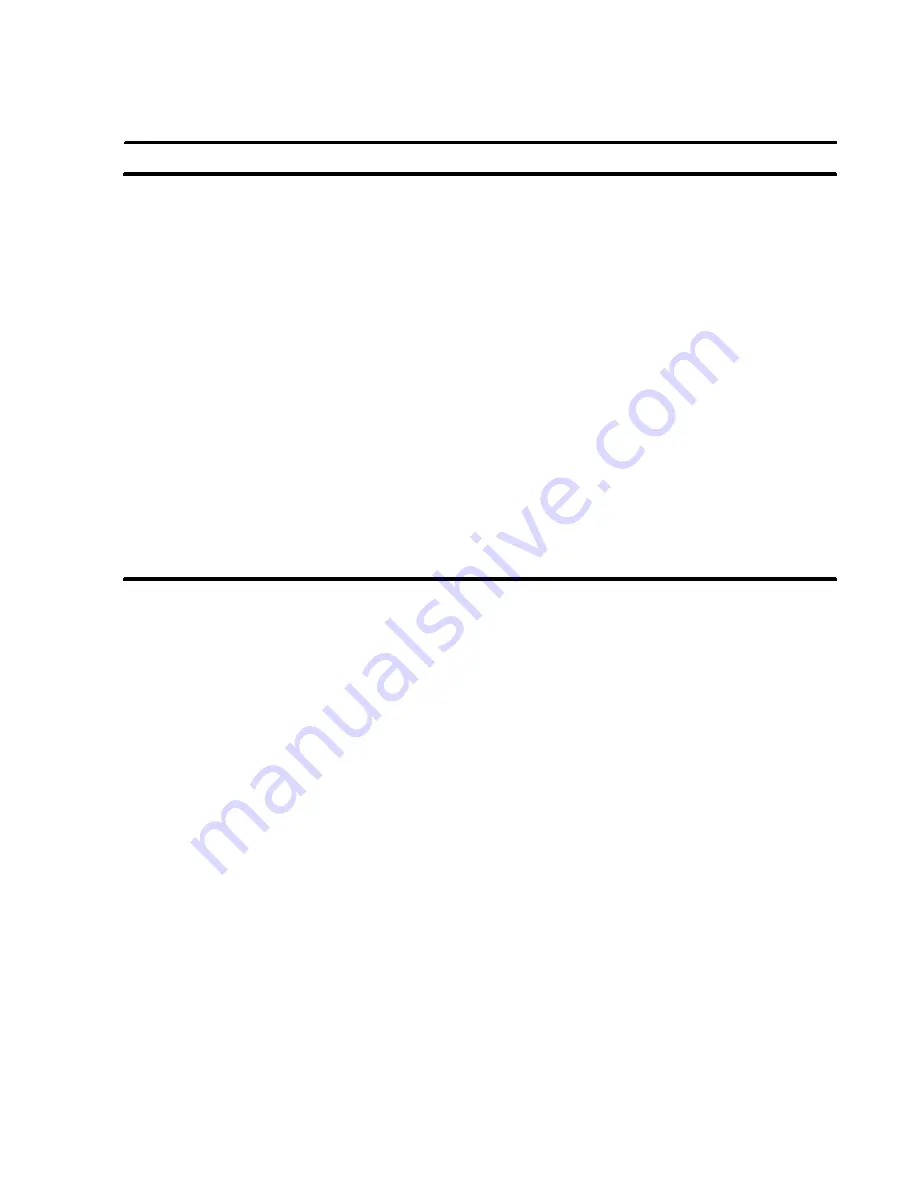
Section 6
COMPRESSOR OPERATION
24
CONTROL OR INDICATOR
PURPOSE
BLOWDOWN VALVE ASSEMBLY
Vents the sump vessel to atmosphere during unload-
ing and shutdown.
THERMAL MIXING VALVE
Bypasses fluid flow around the cooler until the former
reaches a temperature of 180
_
F (82
_
C). Useful for fast
warm--up during start. Maintains a minimum tempera-
ture of 180
_
F (82
_
C) during periods of low load or low
ambient temperatures.
FLUID STOP VALVE
Blocks the flow of fluid to the compressor during shut-
down, thus preventing the discharge of fluid through
the compressor inlet pipework.
SUMP SIGHT GLASS
Indicates level of lubricant in the sump. Located on the
sump side, it should show half--full (compressor
stopped) for proper fluid level.
SEPARATOR RETURN LINE SIGHT GLASSES
Indicate fluid flow in the separator return lines. Large
flow should be visible during full load operation; little to
no flow during unloaded operation. Sluggish flow dur-
ing full load operation indicates the need to clean the
strainers fitted to the return lines.
WATER PRESSURE SWITCH
De--energizes the starter, via the Supervisor, if the wa-
ter pressure falls below 10 psig (0.7 bar). This switch is
not adjustable. Used on water--cooled packages only.
DRAIN VALVES
Lubricant sump drain valve.
5.3 INITIAL START-UP PROCEDURE
The following procedure should be used to make the
initial start--up of the compressor.
1. Read the preceding pages of this manual thor-
oughly.
2. Jog motor to check for correct rotation of fan (re-
fer to Section 2.6).
3. Be sure that all preparations and checks de-
scribed in the Installation Section have been
made.
4. Open the shut--off valve to the service line.
5. Check for possible leaks in piping.
7. Slowly close the shut--off valve to assure proper
nameplate pressure unload setting is correct.
The compressor will unload at nameplate pres-
sure. If adjustments are necessary, see Control
System Adjustments.
7. Observe the operating temperature. If the operat-
ing temperature exceeds 200
_
F (93
_
C), the
cooling system and installation environment
should be checked.
8. Open shut--off valve to the service line.
9. Reinspect the compressor for temperature and
leaks the following day.
5.4 SUBSEQUENT START-UP PROCEDURE
On subsequent start--ups, check that the proper
level is visible in the fluid sight glass and simply
press the START button. When the compressor is
running, observe the instrument panel and mainte-
nance indicators.
5.5 SHUTDOWN PROCEDURE
To shut the compressor down, simply press the
STOP button.
Summary of Contents for LS-20S
Page 6: ...NOTES...
Page 23: ...Section 3 SPECIFICATIONS 17 Figure 3 1A Identification Air cooled Model Prior to June 1 2000...
Page 24: ...Section 3 SPECIFICATIONS 18 Figure 3 1B Identification Air cooled Model After June 1 2000...
Page 25: ...Section 3 SPECIFICATIONS 19 Figure 3 1C Identification Water cooled Model...
Page 26: ...20 NOTES...
Page 31: ...25 NOTES...
Page 76: ...Section 8 PARTS LIST 70 8 16 ELECTRICAL BOX 1 2 3 4 5 6 7 8 9 10 11 12 13 14 15 16...
Page 84: ...Section 8 PARTS LIST 78 8 20 DECAL GROUP 1 2 3 4 5 6 7 8 9 10 11 12 13 14...
Page 86: ...Section 8 PARTS LIST 80 8 20 DECAL GROUP 15 16 17 18 19 20 21 22 23 24...
Page 88: ...Section 8 PARTS LIST 82 8 20 DECAL GROUP 25 26 27 28 29...
Page 90: ...Section 8 PARTS LIST 84 8 20 DECAL GROUP 30 31 32...
Page 92: ...Section 8 PARTS LIST 86 8 21 DECAL LOCATIONS 1 2 3 4 5 6 7 8 9 10 12 11 15 16 17 18 12 13 14...
Page 94: ...Section 8 PARTS LIST 88 8 21 DECAL LOCATIONS 9 1 2 3 4 5 6 7 8 10 11 WATER COOLED MODEL 12 13...
Page 96: ...Section 8 PARTS LIST 90 8 21 DECAL LOCATIONS 1 2 3 5 6 7 4...
Page 98: ...Section 8 PARTS LIST 92 8 22 WIRING DIAGRAM STANDARD FULL VOLTAGE SUPERVISOR II DELUXE...
Page 99: ...Section 8 PARTS LIST 93 8 23 WIRING DIAGRAM STANDARD WYE DELTA SUPERVISOR II DELUXE...
Page 100: ...Section 8 PARTS LIST 94 8 24 WIRING DIAGRAM STANDARD WYE DELTA SUPERVISOR II DELUXE EUROPE...
Page 101: ...NOTES...