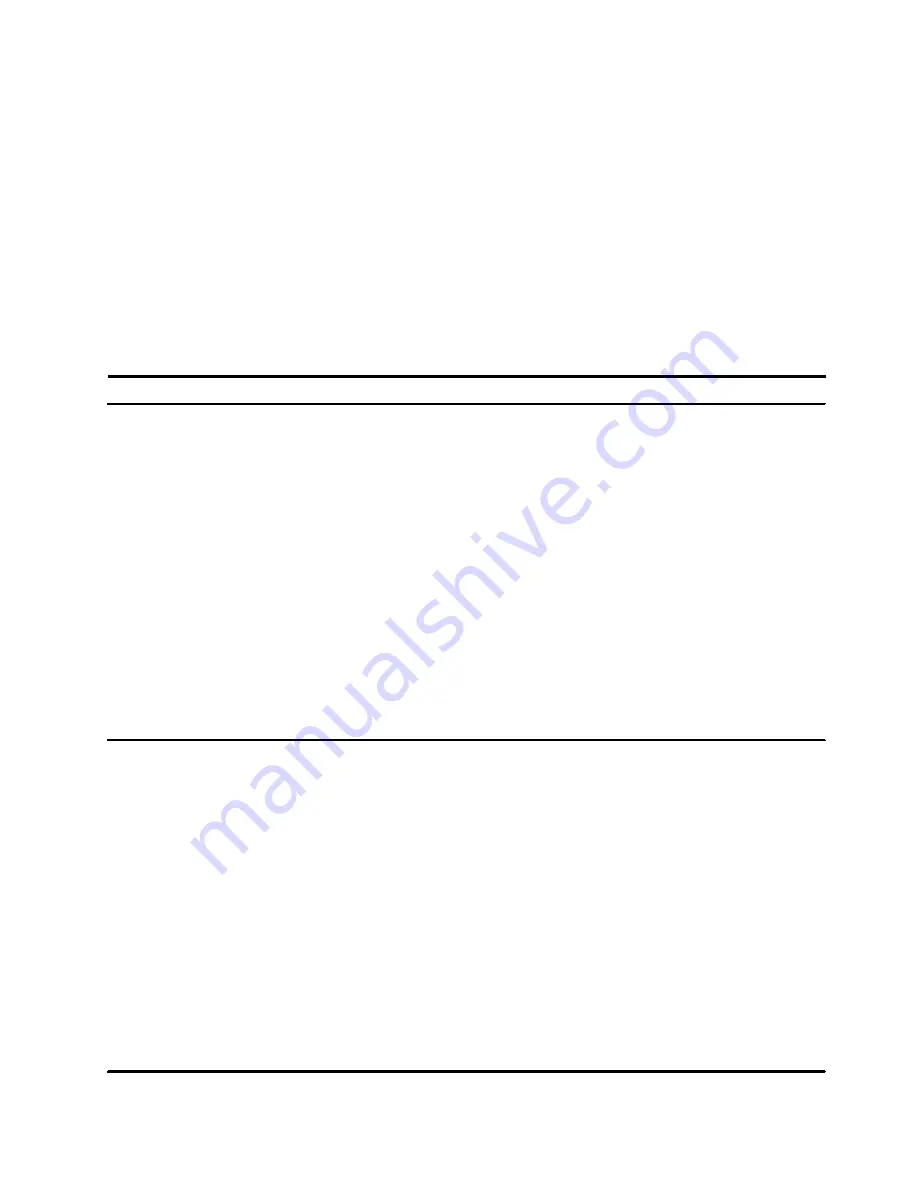
Section 7
MAINTENANCE
37
7.6 TROUBLESHOOTING
The foregoing information has been compiled from
operational experience with your package. It identi-
fies symptoms and diagnosis of SEVERAL probable
difficulties, but NOT ALL of those possible.
The systematic collection of operational data cannot
be over--emphasized, as it may give evidence of the
presence (or not) of a fault before it turns into a seri-
ous breakdown -- for example, the vibrations signa-
ture increase of a damaged bearing, or the efficiency
decrease of a dirty heat exchanger.
A detailed visual inspection is worth performing for
almost all problems and may avoid unnecessary ad-
ditional damage to the compressor. Always remem-
ber to:
1. Check for loose wiring.
2. Check for damaged piping.
3. Check for parts damaged by heat or an electrical
short circuit, usually apparent by discoloration or a
burnt odor.
Should your problem persist after making the recom-
mended check, consult your nearest Sullair repre-
sentative or the Sullair Corporation factory toll free at
1--800--SULLAIR.
7.7 TROUBLESHOOTING GUIDE
SYMPTOM
PROBABLE CAUSE
REMEDY
COMPRESSOR WILL NOT START:
Main Disconnect Switch Open
Close switch.
POWER LED OFF
Line Fuse Blown
Replace fuse.
Control Transformer Fuse Blown
Replace fuse.
MOTOR OL MESSAGE
Motor Starter Overloads Tripped
Reset after heater elements cool
down. Should trouble persist,
check whether motor starter
contacts are functioning
properly.
Low Incoming Line Voltage
Check voltage. Should voltage
check low, consult power
company.
T--1, T--2 FAIL MESSAGE
Temperature Transducer Failure
Check connections from
transducer. If adequate,
replace transducer.
P-1, P-2, P-3, P-4
Pressure Transducer Failure
Check connections from
FAIL MESSAGE
transducer. If adequate,
replace transducer.
MOTOR WILL NOT START,
Emergency Switch Open
Close switch (pull).
E--STOP MESSAGE
(depressed)
LO WATER MESSAGE
Water Pressure Feed Below 10 psig
Check cooling water supply (i.e.,
(Water--cooled packages only)
(0.7 bar)
closed valves).
COMPRESSOR SHUTS DOWN
Motor Starter Overloads Tripped
Reset after heater elements cool
WITH AIR DEMAND:
down. Should trouble persist,
MOTOR OL MESSAGE
check whether motor starter
contacts are functioning properly.
Low Incoming Line Voltage
Check voltage. Should voltage
check low, consult power com--
pany.
P1--LO
P1 is Less Than 10 psig (0.7 bar)
First, check starter wiring. If dis--
charge pressure above 10 psig
(0.7 bar) was evident, then sensor
is at fault -- check connections
from transducer. If adequate,
replace transducer.
P3-LO
Loss of Oil
Check oil level.
Plugged Oil Filter
Replace filter.
P3 is Less Than One Half of P1
HI T1, HI T2 MESSAGE
Discharge Temperature Exceeded
235
_
F (113
_
C) Because:
Ambient temperature exceeded
Improve local ventilation (i.e.,
105
_
F (41
_
C)
remote intake of process and/or
cooling air.
Summary of Contents for LS-20S
Page 6: ...NOTES...
Page 23: ...Section 3 SPECIFICATIONS 17 Figure 3 1A Identification Air cooled Model Prior to June 1 2000...
Page 24: ...Section 3 SPECIFICATIONS 18 Figure 3 1B Identification Air cooled Model After June 1 2000...
Page 25: ...Section 3 SPECIFICATIONS 19 Figure 3 1C Identification Water cooled Model...
Page 26: ...20 NOTES...
Page 31: ...25 NOTES...
Page 76: ...Section 8 PARTS LIST 70 8 16 ELECTRICAL BOX 1 2 3 4 5 6 7 8 9 10 11 12 13 14 15 16...
Page 84: ...Section 8 PARTS LIST 78 8 20 DECAL GROUP 1 2 3 4 5 6 7 8 9 10 11 12 13 14...
Page 86: ...Section 8 PARTS LIST 80 8 20 DECAL GROUP 15 16 17 18 19 20 21 22 23 24...
Page 88: ...Section 8 PARTS LIST 82 8 20 DECAL GROUP 25 26 27 28 29...
Page 90: ...Section 8 PARTS LIST 84 8 20 DECAL GROUP 30 31 32...
Page 92: ...Section 8 PARTS LIST 86 8 21 DECAL LOCATIONS 1 2 3 4 5 6 7 8 9 10 12 11 15 16 17 18 12 13 14...
Page 94: ...Section 8 PARTS LIST 88 8 21 DECAL LOCATIONS 9 1 2 3 4 5 6 7 8 10 11 WATER COOLED MODEL 12 13...
Page 96: ...Section 8 PARTS LIST 90 8 21 DECAL LOCATIONS 1 2 3 5 6 7 4...
Page 98: ...Section 8 PARTS LIST 92 8 22 WIRING DIAGRAM STANDARD FULL VOLTAGE SUPERVISOR II DELUXE...
Page 99: ...Section 8 PARTS LIST 93 8 23 WIRING DIAGRAM STANDARD WYE DELTA SUPERVISOR II DELUXE...
Page 100: ...Section 8 PARTS LIST 94 8 24 WIRING DIAGRAM STANDARD WYE DELTA SUPERVISOR II DELUXE EUROPE...
Page 101: ...NOTES...