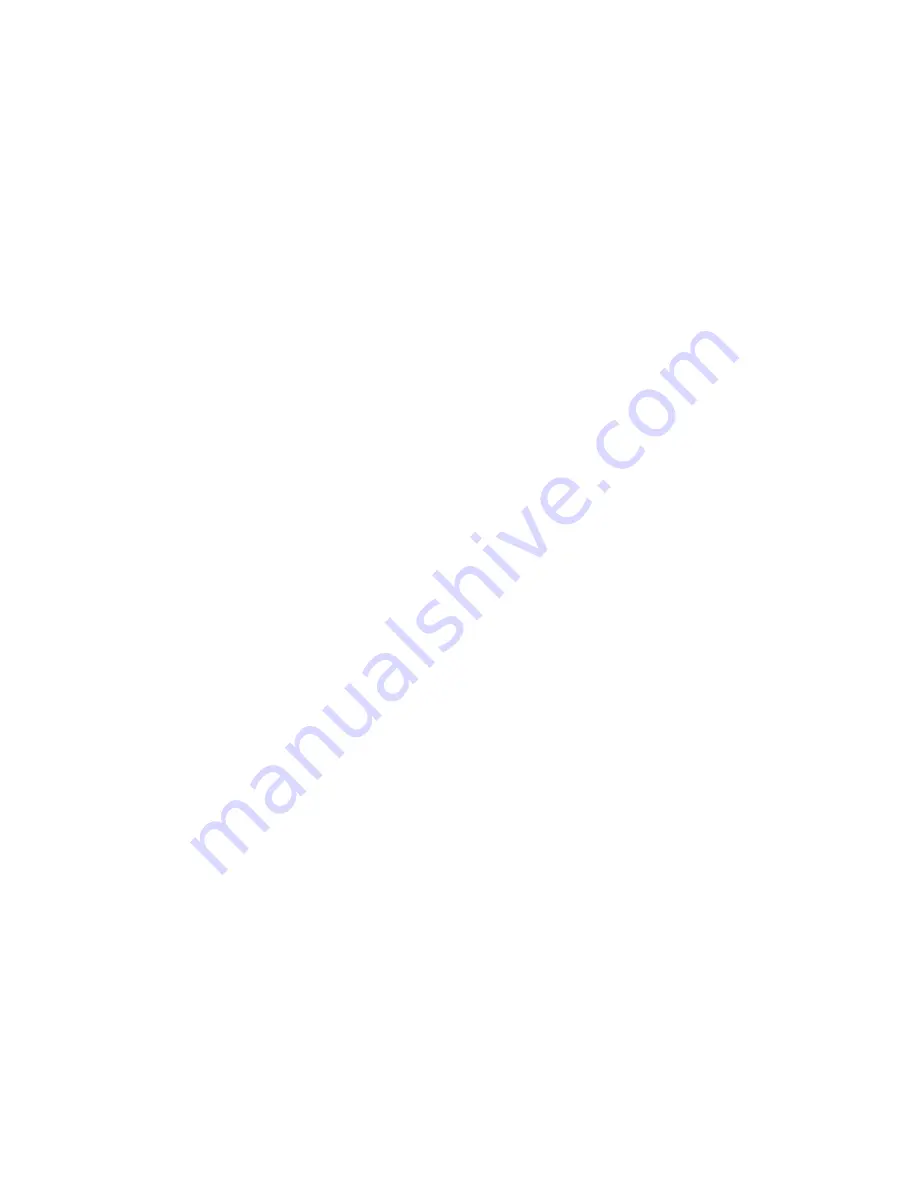
Section 1
SAFETY
3
C.
Operate the compressor only in open or ade-
quately ventilated areas.
D.
Locate the compressor or provide a remote inlet
so that it is not likely to ingest exhaust fumes or other
toxic, noxious or corrosive fumes or substances.
E.
Coolants and lubricants used in this compressor
are typical of the industry. Care should be taken to
avoid accidental ingestion and/or skin contact. In
the event of ingestion, seek medical treatment
promptly. Wash with soap and water in the event of
skin contact. Consult the compressor operator’s
manual lubrication section for information pertaining
to compressor fluid fill.
F.
Wear goggles or a full face shield when adding an-
tifreeze compound to air line anti--icer systems.
G.
If air line anti--icer system antifreeze compound
enters the eyes or if fumes irritate the eyes, they
should be washed with large quantities of clean wa-
ter for 15 minutes. A physician, preferably an eye
specialist, should be contacted immediately.
H. DO NOT
store air line anti--icer system antifreeze
compound in confined areas.
I.
The antifreeze compound used in air line anti-
freeze systems contains methanol and is toxic,
harmful, or fatal if swallowed. Avoid contact with the
skin or eyes and avoid breathing the fumes. If swal-
lowed, induce vomiting by administering a table-
spoon of salt, in each glass of clean, warm water un-
til vomit is clear, then administer two teaspoons of
baking soda in a glass of clean water. Have patient
lay down and cover eyes to exclude light. Call a phy-
sician immediately.
1.8 ELECTRICAL SHOCK
A.
This compressor should be installed and main-
tained in full compliance with all applicable Federal,
State and Local codes, standards and regulations,
including those of the National Electrical Code, and
also including those relative to equipment grounding
conductors, and only by personnel that are trained,
qualified and delegated to do so.
B.
Keep all parts of the body and any hand--held
tools or other conductive objects away from ex-
posed live parts of electrical system. Maintain dry
footing, stand on insulating surfaces and
DO NOT
contact any other portion of the compressor when
making adjustments or repairs to exposed live parts
of the electrical system. Make all such adjustments
or repairs with one hand only, so as to minimize the
possibility of creating a current path through the
heart.
C.
Attempt repairs in clean, dry and well lighted and
ventilated areas only.
D. DO NOT
leave the compressor unattended with
open electrical enclosures. If necessary to do so,
then disconnect, lock out and tag all power at source
so others will not inadvertently restore power.
E.
Disconnect, lock out, and tag all power at source
prior to attempting repairs or adjustments to rotating
machinery and prior to handling any ungrounded
conductors.
F.
Dry test all shutdown circuits prior to starting the
compressor after installation.
1.9 LIFTING
A.
If the compressor is provided with a lifting bail,
then lift by the bail provided. If no bail is provided,
then lift by sling. Compressors to be air lifted by heli-
copter must not be supported by the lifting bail but by
slings instead. In any event, lift and/or handle only in
full compliance with Federal, State and Local codes.
B.
Inspect points of attachment for cracked welds
and for cracked, bent, corroded or otherwise de-
graded members and for loose bolts or nuts prior to
lifting.
C.
Make sure entire lifting, rigging and supporting
structure has been inspected, is in good condition
and has a rated capacity of at least the weight of the
compressor. If you are unsure of the weight, then
weigh compressor before lifting.
D.
Make sure lifting hook has a functional safety
latch or equivalent, and is fully engaged and latched
on the bail or slings.
E.
Use guide ropes or equivalent to prevent twisting
or swinging of the compressor once it has been lifted
clear of the ground.
F. DO NOT
attempt to lift in high winds.
G.
Keep all personnel out from under and away from
the compressor whenever it is suspended.
H.
Lift compressor no higher than necessary.
I.
Keep lift operator in constant attendance whenev-
er compressor is suspended.
J.
Set compressor down only on a level surface ca-
pable of safely supporting at least its weight and its
loading unit.
K.
When moving compressors by forklift truck, uti-
lize fork pockets if provided. Otherwise, utilize pallet
if provided. If neither fork pockets or pallet are pro-
vided, then make sure compressor is secure and
well balanced on forks before attempting to raise or
transport it any significant distance.
L.
Make sure forklift truck forks are fully engaged
and tipped back prior to lifting or transporting the
compressor.
M.
Forklift no higher than necessary to clear ob-
stacles at floor level and transport and corner at
minimum practical speeds.
N.
Make sure pallet--mounted compressors are
firmly bolted or otherwise secured to the pallet prior
to attempting to forklift or transport them.
NEVER
attempt to forklift a compressor that is not secured to
its pallet, as uneven floors or sudden stops may
cause the compressor to tumble off, possibly caus-
ing serious injury or property damage in the process.
Summary of Contents for LS-20S
Page 6: ...NOTES...
Page 23: ...Section 3 SPECIFICATIONS 17 Figure 3 1A Identification Air cooled Model Prior to June 1 2000...
Page 24: ...Section 3 SPECIFICATIONS 18 Figure 3 1B Identification Air cooled Model After June 1 2000...
Page 25: ...Section 3 SPECIFICATIONS 19 Figure 3 1C Identification Water cooled Model...
Page 26: ...20 NOTES...
Page 31: ...25 NOTES...
Page 76: ...Section 8 PARTS LIST 70 8 16 ELECTRICAL BOX 1 2 3 4 5 6 7 8 9 10 11 12 13 14 15 16...
Page 84: ...Section 8 PARTS LIST 78 8 20 DECAL GROUP 1 2 3 4 5 6 7 8 9 10 11 12 13 14...
Page 86: ...Section 8 PARTS LIST 80 8 20 DECAL GROUP 15 16 17 18 19 20 21 22 23 24...
Page 88: ...Section 8 PARTS LIST 82 8 20 DECAL GROUP 25 26 27 28 29...
Page 90: ...Section 8 PARTS LIST 84 8 20 DECAL GROUP 30 31 32...
Page 92: ...Section 8 PARTS LIST 86 8 21 DECAL LOCATIONS 1 2 3 4 5 6 7 8 9 10 12 11 15 16 17 18 12 13 14...
Page 94: ...Section 8 PARTS LIST 88 8 21 DECAL LOCATIONS 9 1 2 3 4 5 6 7 8 10 11 WATER COOLED MODEL 12 13...
Page 96: ...Section 8 PARTS LIST 90 8 21 DECAL LOCATIONS 1 2 3 5 6 7 4...
Page 98: ...Section 8 PARTS LIST 92 8 22 WIRING DIAGRAM STANDARD FULL VOLTAGE SUPERVISOR II DELUXE...
Page 99: ...Section 8 PARTS LIST 93 8 23 WIRING DIAGRAM STANDARD WYE DELTA SUPERVISOR II DELUXE...
Page 100: ...Section 8 PARTS LIST 94 8 24 WIRING DIAGRAM STANDARD WYE DELTA SUPERVISOR II DELUXE EUROPE...
Page 101: ...NOTES...