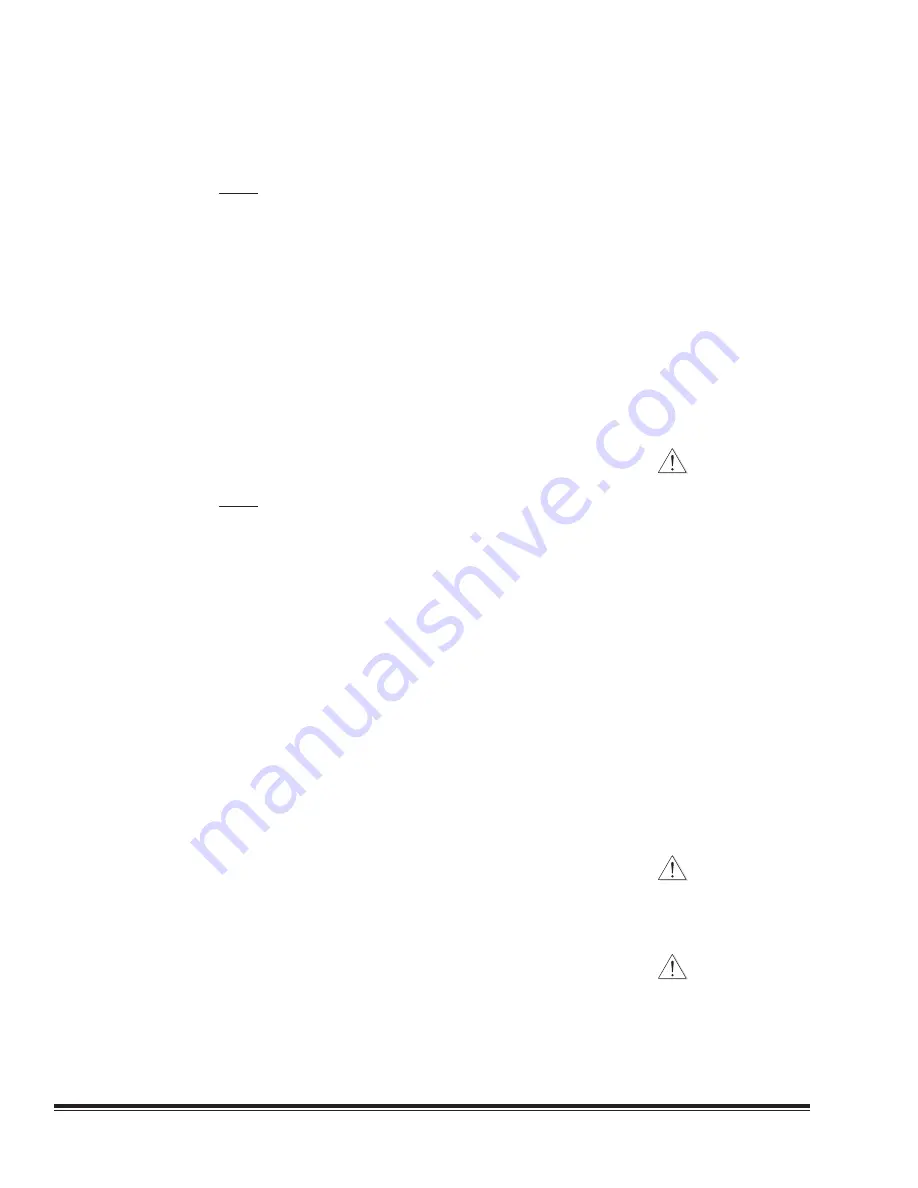
28
M
INI
-S
PACE
EC I
NSTALLATION
, O
PERATION
AND
M
AINTENANCE
M
ANUAL
4.3 Field
Service
NOTE
Do not attempt to make repairs without the proper
tools.
It may be necessary to perform repairs on the refrigeration
system. If fi eld repairs are necessary, the following procedures
apply.
4.3.1 Leak
Detection
Several methods can be used to detect a leak in the
refrigeration system. The most modern and easiest method is
to use an electronic leak detector. Follow the manufacturer’s
directions and any leak can be quickly located. A second
method is to use soap bubbles. Apply a solution of soapy
water with a brush or sponge to the joints and connections
in the refrigeration lines. A leak in the lines will cause bubbles
to form.
NOTE
Use a halogen leak detector capable of detecting
R410A refrigerant.
4.3.2 Leak
Repair
When a leak is located, properly reclaim the remaining
refrigerant charge before beginning repairs. Adjacent piping
must be thoroughly cleaned by removing all paint, dirt and oily
fi lm. Use a wire brush, sandcloth or sandpaper and wipe the
area with clean, dry cloths. Protect nearby parts from heat
damage by wrapping with water-soaked cloths.
4.3.3 Refrigerant
Piping
When replacing components within the cabinet of the unit,
the following solders are recommended: Silfos alloy for
copper-to-copper (piping discharge or suction line repairs);
silver solder (Stay-Silv #45) and fl ux for copper-to-brass or
copper-to-steel repairs; and a 95% tin to 5% antimony solder
with fl ux for liquid line repairs at the drier, strainer, sight glass,
or expansion valve.
When component replacement is complete, remove all traces
of fl ux. After any repair, pressure check the system and ensure
there are no leaks prior to recharging the system.
4.3.4 General Common Repairs/Component
Replacement
4.3.4.1 Compressor
Failure
The compressor is the most important component of a DX
unit. Numerous safety devices are provided to protect the
compressor from failing.
When a compressor fails, determine whether the cause is
electrical or mechanical. An electrical failure is indicated by a
distinct pungent odor once the system has been opened. If a
burnout occurred, the oil will be black and acidic. A mechanical
failure will have no burned odor and the motor will attempt to
run. An abnormal or excessive noise may be present.
Analyzing the oil is the only way to determine the proper
procedure for cleaning the refrigerant system. Acid test kits
are available from several manufacturers for measuring the
acid level in the oil. These are capable of making accurate
acidity measurements, but if they are not available a check
of the oil by sight and smell can give a quick indication if
contamination remains in the system. Since refrigeration
oils vary in color, a sample of the new oil in the replacement
compressor should be removed prior to installation and sealed
in a small glass bottle for comparison purposes. If the oil has
been exposed to refrigerant, the bottle should not be tightly
capped, since the residual refrigerant may create a high
pressure if tightly sealed and exposed to high temperature.
CAUTION
Avoid touching or contacting the gas and oil with
exposed skin. Severe burns will result. Use long
rubber gloves when handling contaminated parts.
All electrical connections should be checked to ensure
they are tight and properly made. Check all circuit breakers,
contactors and wiring. Contactors should be examined and
replaced if the contacts are worn or pitted.
If there is acid in the oil, there has been an electrical failure
which has caused the compressor motor to burn out. The acid
diffuses throughout the refrigeration system and must be
removed by using a burnout fi lter kit before a new compressor
is placed in service. Not only must the compressor be
replaced, but the entire refrigeration circuit must be cleaned
of the harmful contaminants left by the burnout. See section
4.3.4.3, “Burn-Out/Acid Cleanup Procedure” for the proper
procedure.
If there is no acid in the oil, there has been a mechanical failure.
See section 4.3.4.2, “Standard Clean out Procedure” for the
proper cleaning procedure.
CAUTION
Damage to a replacement compressor caused by
improper system cleaning constitutes abuse under
the terms of the warranty and will void the warranty.
CAUTION
POE oil is used in systems with R410A refrigerant. If
a replacement compressor is provided, ensure that
it is fi lled with POE oil before installing.