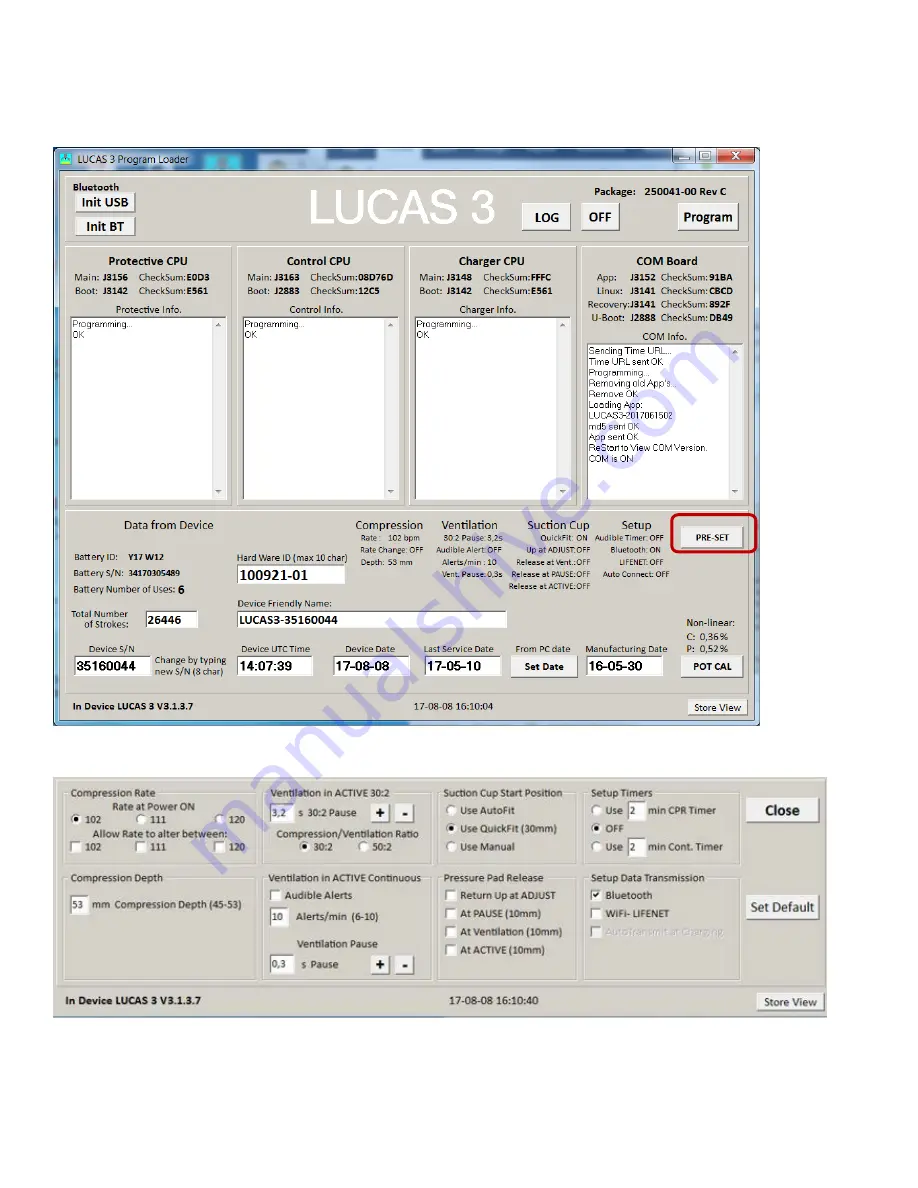
LUCAS
®
3 Chest Compression System –
Service Manual
3328798-002, ©2017 Physio-Control, Inc.
Page
35
of
91
Setup Options - LUCAS 3 Version 3.1 (Part No: 250041-00)
The Setup Options are configurable for a LUCAS 3 Version 3.1 device. To enter the configuration tool press the
“PRE-SET” key.
The preset Options are depicted and described below. To enter the factory default setting, press the key “Set Default”.