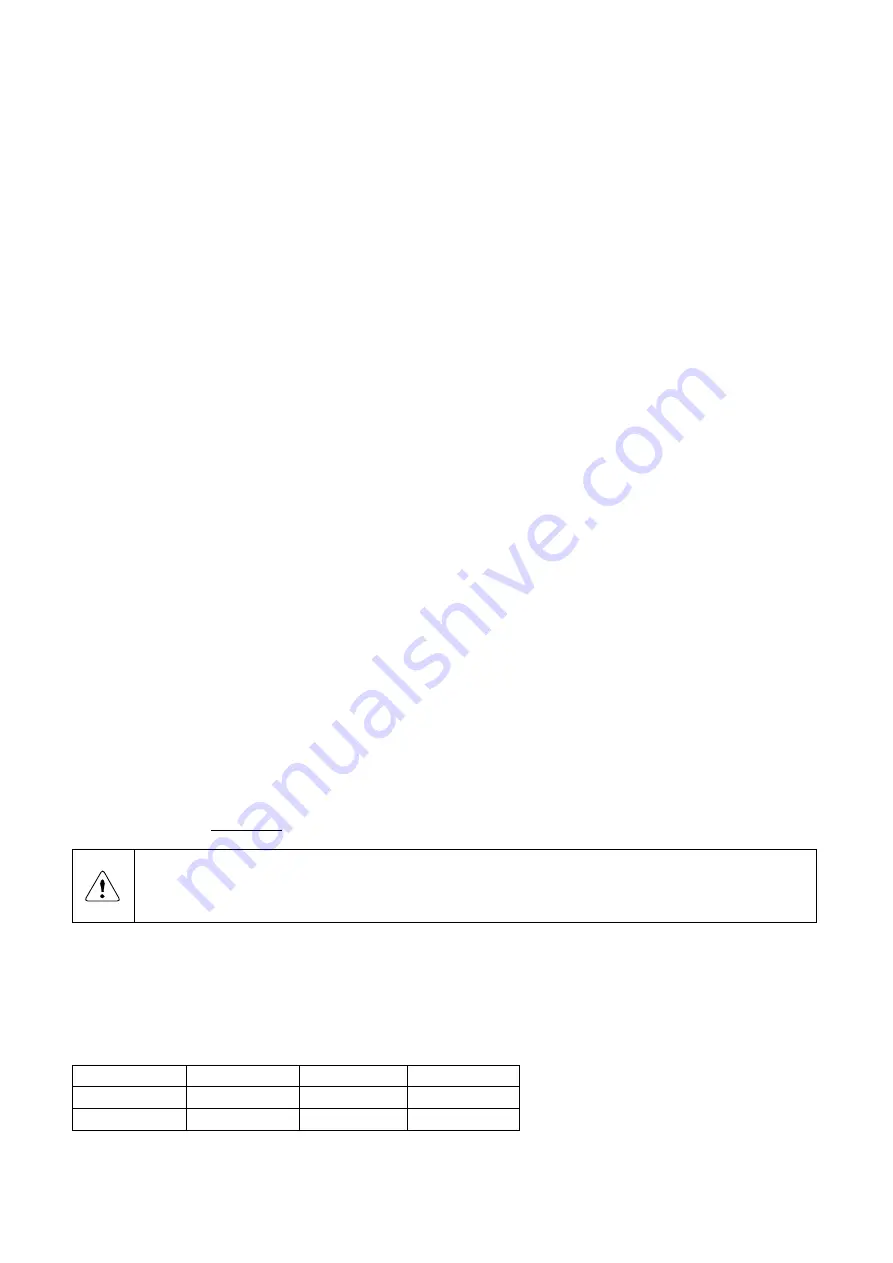
50
13 COMMISSIONING THE BOILER
13.1 First: Flushing the Boiler with Water
After installation of the boiler the first step, before commissioning, is to flush the boiler and the whole heating
installation with fresh water to remove pollution, debris and other materials that might cause a blocking.
This must also be done with heating installations, where only the boiler is replaced.
Existing and new heating systems must be cleaned with an approved system cleaner; see chapter 6.15 "Chemical
water treatment.
” System cleaner must be drained and thoroughly flushed with clean water to remove any residual
cleaner, prior to installing a new boiler. NEVER leave a system cleaner for longer than recommended by the
manufacturer of the cleaner.
13.2 Second: Filling & Venting the Boiler and the System
After flushing the boiler and the installation the system can be filled with fresh water. Fill the boiler and the heating
system by using the appropriate filling valve. The water pressure of the system normally lies between 1,5 and 2,0
bar.
NOTICE: Use the following aspects to prevent corrosion of the central heating system:
•
Filling water: Do not use any additives for the water of the central heating system, except glycol. The pH value
of the water should be more than 5 (If this pH value is less, please contact the supplier).
•
Ensure that any used
“plastic” pipes are oxygen diffusion-proof in accordance with DIN 4726/4729. If not,
make sure that the boiler circuit is separated from the heating circuit by a plate heat exchanger. This way no
oxygen that entered the heating system through these pipes can reach the boiler.
Check the total heating system for any leaks. This to prevent oxygen entering the system through these leaks.
The boiler has an automatic air vent situated inside the boiler. This vent is always open, and the venting outlet
goes via a plastic tube through the bottom to the outside. Shortly after putting the boiler into operation, check the
water pressure and add or remove some water to obtain the required pressure.
During the commissioning, make sure that no water can enter the boiler and make contact with the electrical parts.
13.3 Third: Check the Water Flow
Before starting the boiler ensure the circulating pump(s) installed and operating correctly and that there are no
obstructions or closed valves that could prevent water flow through the heat exchanger.
13.4 Mounting Condensate Trap
When mounting the bottom part of the condensate trap, before commissioning the boiler and/or after maintenance,
it must
ALWAYS
be completely filled with water.
This is a safety measure: The water in the condensate trap keeps the flue gases from
leaking out of the heat exchanger via the condensate drain.
13.5 Checking Gas Pressure
Check the gas pressure available at the gas connection pipe of the boiler. Use the pressure nipple of the gas
safety valve for this measurement.
Min. and max. gas supply pressures:
Type of Gas
p nom [mbar]
p min [mbar]
p max [mbar]
G20
20
18
25
G31
37
25
57.5
Summary of Contents for S-FX 125
Page 2: ......
Page 11: ...11 4 BOILER DIMENSIONS 4 1 S FX 70 4 2 S FX 125 ...
Page 12: ...12 4 3 S FX 220 4 4 S FX 320 ...
Page 28: ...28 9 4 Electrical Schematics S FX 70 ...
Page 29: ...29 S FX 125 ...
Page 30: ...30 S FX 220 320 ...
Page 67: ...67 BLANK PAGE ...