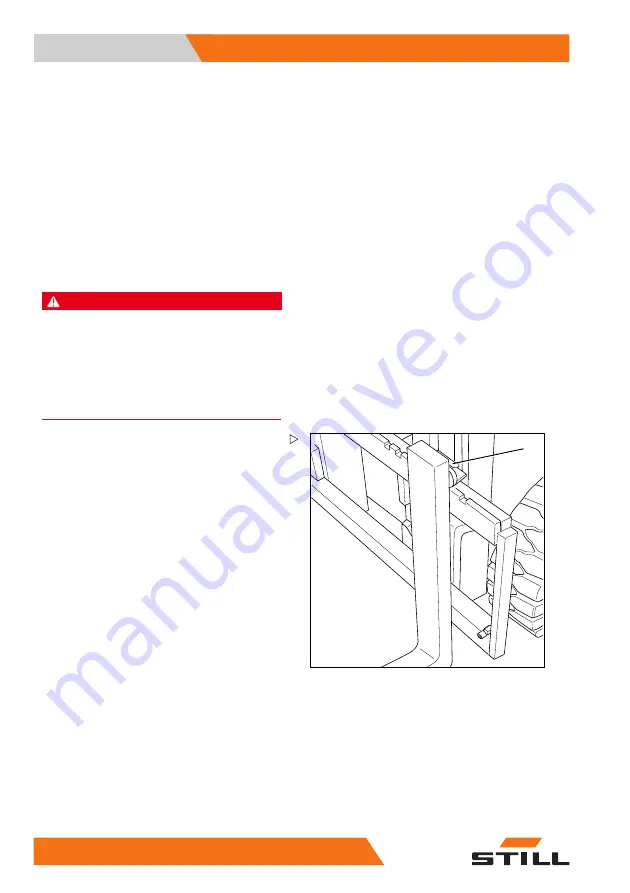
5
Operation
Working with loads
Carrying loading units
To ensure secure supporting of the load, it
must be ensured that the fork arms are suffi-
ciently far apart and are positioned as far as
possible under the load.
If possible, the load should rest on the back of
the fork.
The load may not protrude significantly be-
yond the fork tips and vice versa.
Loads are to be carried and transported as
close to the middle as possible.
DANGER
Risk of accident!
When transporting small items, attach a safety gu-
ard (special equipment) to prevent the load from
falling on the driver.
A closed roof covering (special equipment) should
also be used.
Removable roof segments may not be removed.
1
6210_842-001
Setting forks
– Lift stopping lever (1) and move the fork
arms to the desired position.
– Allow the stopping lever to snap back into
place.
The centre of gravity of the load must be posi-
tioned between the fork arms in the middle.
– Only operate the fork arm adjustment (spe-
cial equipment) when the forks are not
loaded.
Hazard area
The hazard area is the area where persons
are endangered by movements of the forklift
truck, its working equipment, its load-carrying
equipment (e.g. attachments) or the load.
Included in this area is also the area which can
be affected by a falling load, or by lowering or
falling working equipment.
104
171673 [EN]
Summary of Contents for R70-40T
Page 2: ......
Page 11: ...1 Foreword ...
Page 18: ...1 Foreword Environmental considerations 8 171673 EN ...
Page 19: ...2 Introduction ...
Page 25: ...Introduction 2 Residual risk 171673 EN 15 ...
Page 29: ...3 Safety ...
Page 49: ...4 Overviews ...
Page 51: ...Overviews 4 General view 171673 EN 41 ...
Page 63: ...5 Operation ...
Page 186: ...5 Operation Shut down 176 171673 EN ...
Page 187: ...6 Maintenance ...
Page 248: ...6 Maintenance 3000 hour maintenance two year maintenance 238 171673 EN ...
Page 257: ...7 Technical data ...
Page 265: ...8 Circuit diagrams ...
Page 266: ...8 Circuit diagrams Hydraulics Hydraulics Hydraulic circuit diagram 7071_003 083 256 171673 EN ...
Page 280: ...8 Circuit diagrams Electrical equipment 270 171673 EN ...
Page 287: ......
Page 288: ...Still GmbH Berzeliusstrasse 10 D 22113 Hamburg Ident no 171673 EN ...