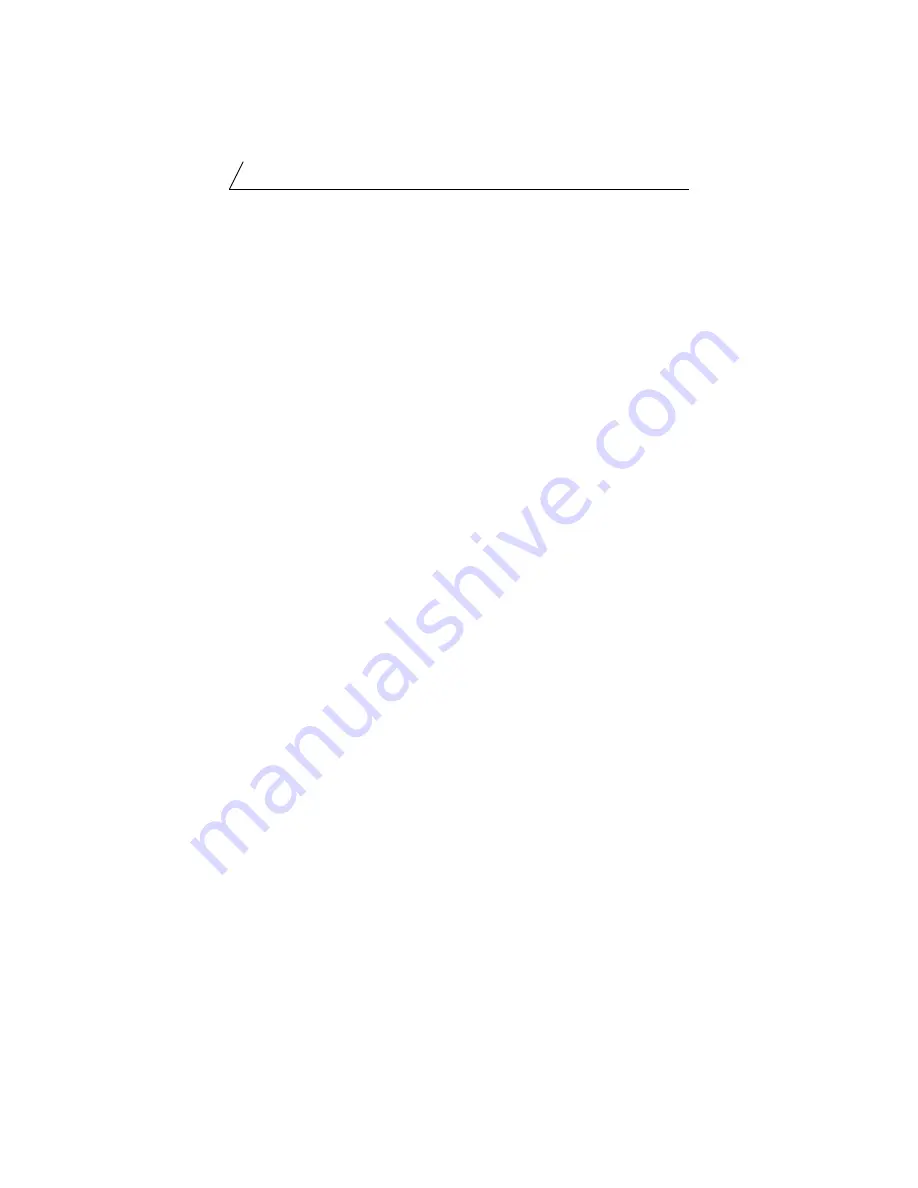
SST-ASI-SLC User’s Guide
54
9.3
Slave Failure
9.3.1 Single Slave Failure
In the event of a single slave failure, Auto Address Programming may be
available if you have enabled it in the G file. If you have enabled Auto
Address Programming, the COMM LED on the affected channel flashes
green and the SLC faults with error code 62h (refer to the table in section
9.1).
If you are going to replace the slave using Auto Address Programming, you
must replace the defective slave with a slave at address 0 and with an I/O type
and ID code that match the defective slave’s. Once this has been done, the
SLC can be toggled from program to run and the network should return to
normal operation.
If the M files have been scanned recently (i.e. immediately before the fault
occurred), the slave delta list (SDL) will reflect which slave has failed.
9.3.2 Multiple Slave Failure
In the event of multiple slave failure, if the M files have been scanned
recently (i.e. immediately before the fault occurred), the SDL in the M files
will indicate which slaves have failed.
9.4
An Important Note on AS-i Faults
This information applies to hardware version 1.0 only.
With some versions of the SLC, if your program clears the main error flag
(S2:1/13), it is possible that subsequent faults on other scanners or SLC
processors might not be reported to the scanner and the scanner will continue
scanning even if the SLC is faulted. Refer to section 4.8 for complete details.
Summary of Contents for SST-ASI-SLC
Page 6: ...SST ASI SLC User s Guide vi Conformance Statement 63 CE Notice 67 C D...
Page 13: ...7 This chapter contains a system overview information on hardware features 2 Overview...
Page 20: ...SST ASI SLC User s Guide 14...
Page 30: ...SST ASI SLC User s Guide 24 IOM Ladder Logic Instruction...
Page 44: ...SST ASI SLC User s Guide 38...
Page 66: ...SST ASI SLC User s Guide 60...
Page 72: ...SST ASI SLC User s Guide 66...
Page 74: ...SST ASI SLC User s Guide 68...